Regolith Rotary-Percussive Drill
For my senior capstone design project, I was fortunate to be selected to develop a novel regolith drill along with four other classmates. Sponsored by Techno Planet Inc., The Regolith Drill capstone team designed a prototype assembly of a variable speed rotary-percussive drill and drill-bit to be capable of drilling a one meter hole into the permafrost layer on terrestrial and extraterrestrial surfaces. It is capable of heating the drilled hole using an integrated heating rod in the center of the drill bit to allow for the capture of vaporous substances released after heating. The design includes two separate motors to control the rotary and percussive motion independently, so that the ratio of beats per minute to rotations per minute can be optimized.
During the first phase of the project, I researched existing rotary-percussive drill mechanisms, which typically included masonry and hammer drills. I came to learn that the existing designs were not suitable for our application as the percussive motion and rotational motion were typically fixed, with the exception of oil drills. This irrelevance led to the novel design of an independent rotary-percussive mechanism. This was crucial as there exists a great variance in the consolidation of regolith across different celestial bodies and atmospheric conditions, leading to their respective optimal drilling ratios.
It was decided a barrel cam was our best option to produce the percussive motion, while the rotation would simply be driven by a gear at the top of the drill shaft. The independence of motion was allowed through a floating jaw coupler, with the aid of thrust needle bearings. The mechanism had to be designed with longevity and efficiency in mind given the nature of the applications. After multiple iterations of the barrel cam, a final design greatly reduced friction and wear on the part to maintain the requirements of mechanism efficiency and lifespan.
Due to the harsh conditions of space, it was imperative that the drill be isolated from any foreign debris. I led the group in material selection for the seals, mechanism components, and housing to best ensure reliable and cost effective operation. To best capture all potential particles, a series of ring and brush seals of varying materials were selected.
Some of the Process
Testing the best bit heads and flute configurations
Observing a sample Cartridge Heater
Our first discovery of a Jaw Coupler (a Hoorah Moment)



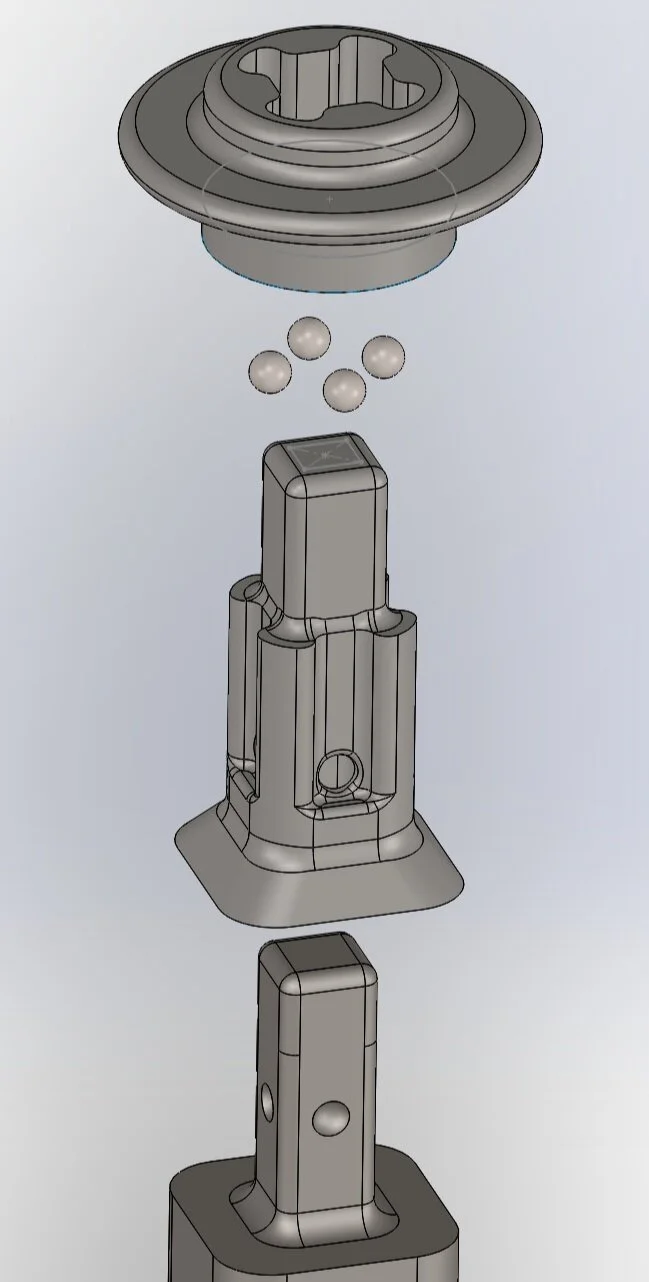
The Takeaways
I learned more than I ever could have dreamt of upon tackling this project. The thrill of research to conception is something that I thrive on and hope to continue doing in my career.
I was fortunate to be able to work hand in hand with my university’s machinist to best design for ease of manufacture, something that is now instilled in my engineering mindset.
This project further demonstrated to me the joy of working with great people to accomplish a huge task. I was able to talk to industry specialists and manufacturers, giving me insight on how to operate efficiently in compliance with respective guidelines. My capstone partners and I were able to challenge each other and arrive upon the best solutions, while maintaining an eagerness for each other and the project.
I also learned that I don’t think I will ever get tired of doing 3D Modeling! If it were to happen it would definitely have been so within this project, but I came out with an even greater understanding and appreciation for SolidWorks.
Now to the sad news…
While our part orders and final designs were ready, we were unable to return to campus to assemble and test the drill due to the campus shutting down for COVID-19. We were extremely disappointed to hear this news and not see all of our hard work come to physical fruition. Despite this, we could not have asked for a more engaging, challenging, and satisfying project to participate in.