Hello Tushy
Position: Product Development Intern
Role: Research, Design, Prototyping & Validation, Packaging, Rendering
Project Timeline: Feb 2021 - Mar 2021
Ottoman Leg Packaging
When I first had the privilege of working with the Tushy Product team, I was tasked with revamping the leg packaging for their elegant toilet stool, the Ottoman.
The existing packaging exhibited a protection deficit, lack of sophistication, and assembly miscues. This entailed placing the 4 unique legs in identical paper bags with a white sticker label; the unconstrained configuration deprecated the aesthetic of the otherwise stunning product, was inefficient to package and unbox, and led to customers receiving duplicate legs.
To give the Ottoman the justice it deserved, I designed a single-piece molded fiber insert with four unique ribbed bosses and a living hinge.
-
The Old
-
The New
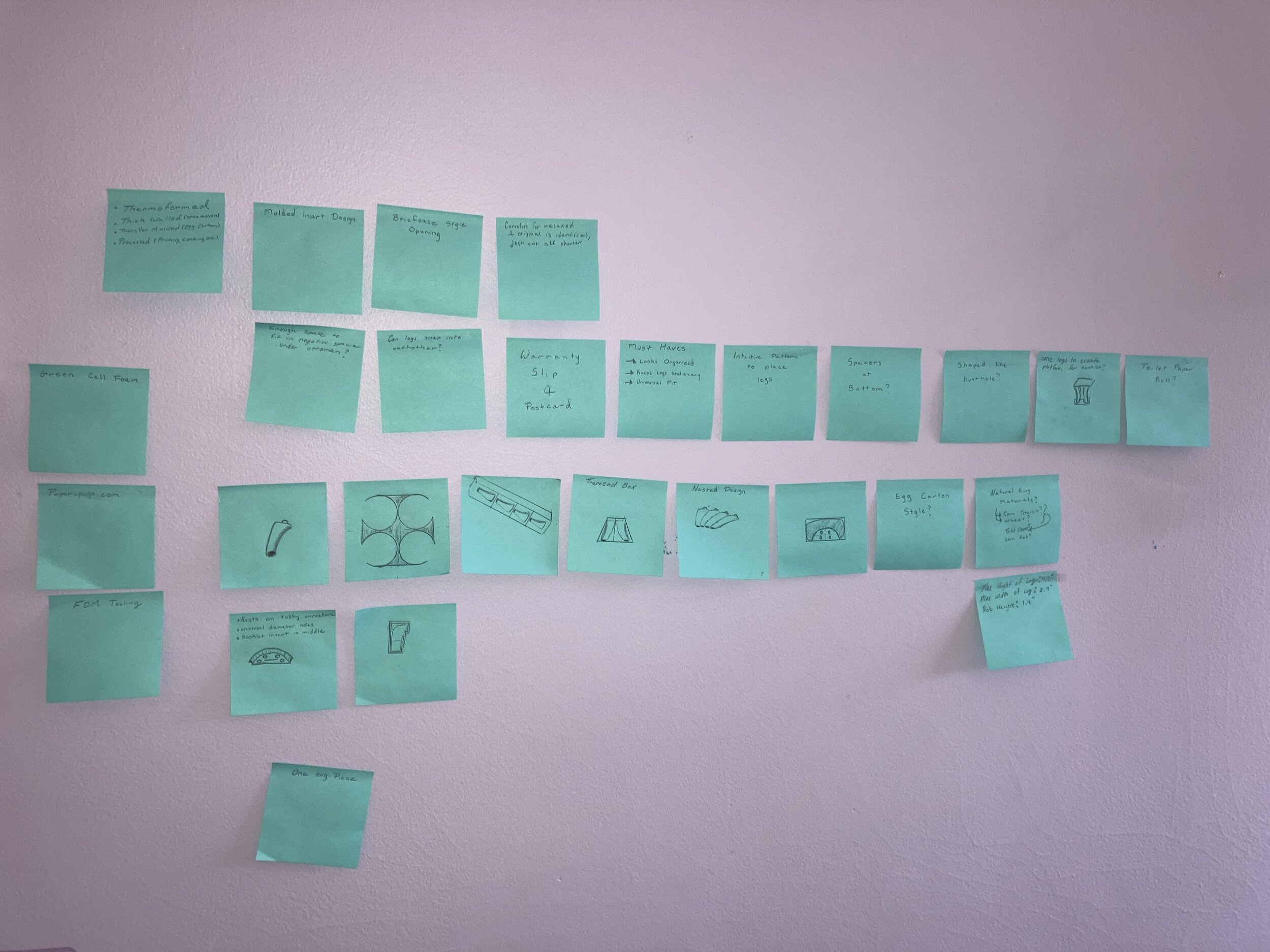
The Concept Phase
-
Moodboard
Inspiration for the final design was gathered by exploring existing sustainable packaging methods. Researching similarly shaped products influenced the final packing configuration to achieve a confident presentation.
-
Insights
Along the way, I wrote down ideas and learnings to not leave anything on the table. Sticky notes are a great visual aid to digest these.
Design and Prototyping
After conducting my preliminary research, I established my product design requirements:
Eliminates opportunity for miss-assembly
Provides sufficient protection
Fits both the short and long versions of the legs
One-piece molded pulp design
Cost efficient
Smooth unboxing experience
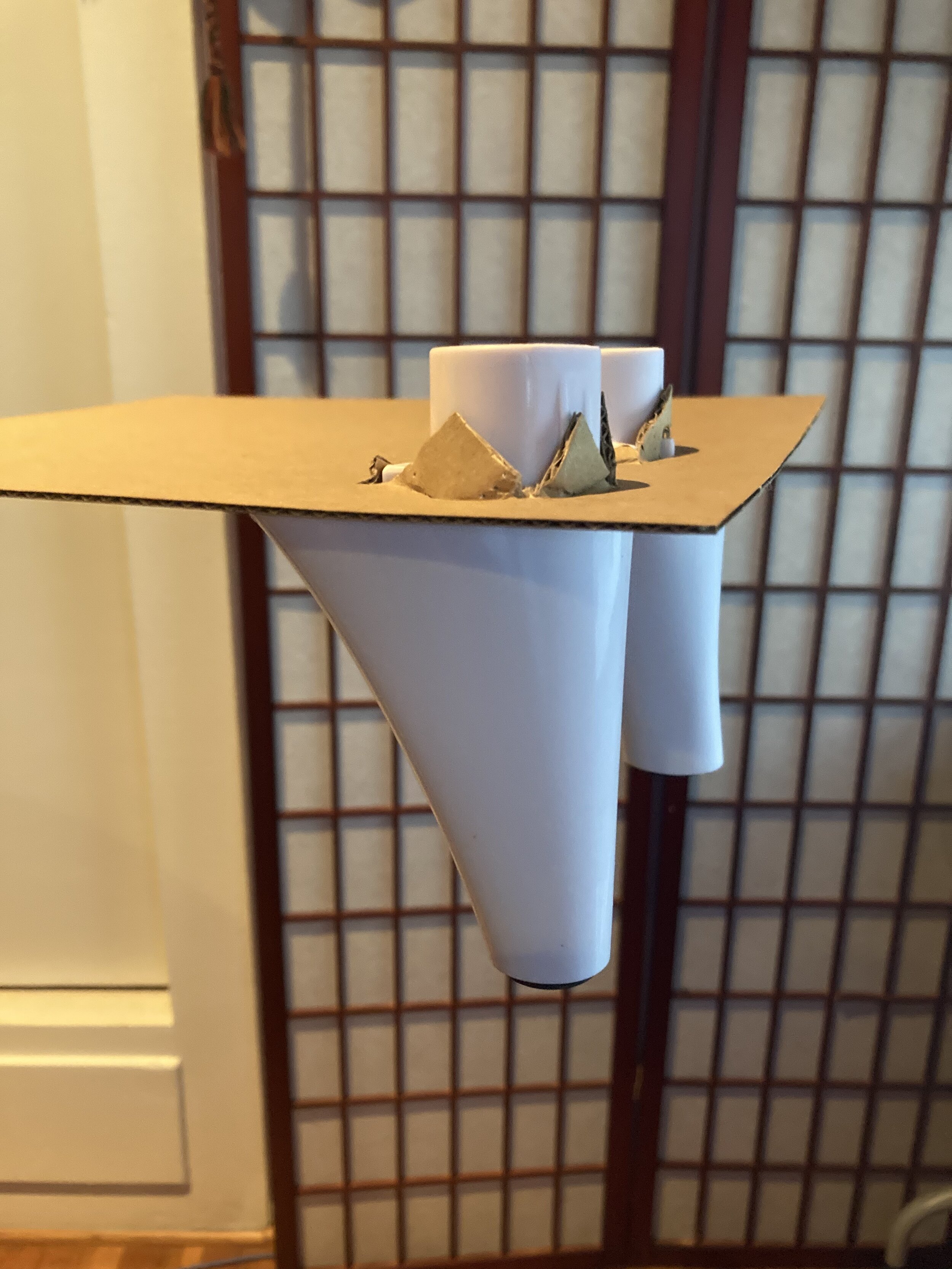
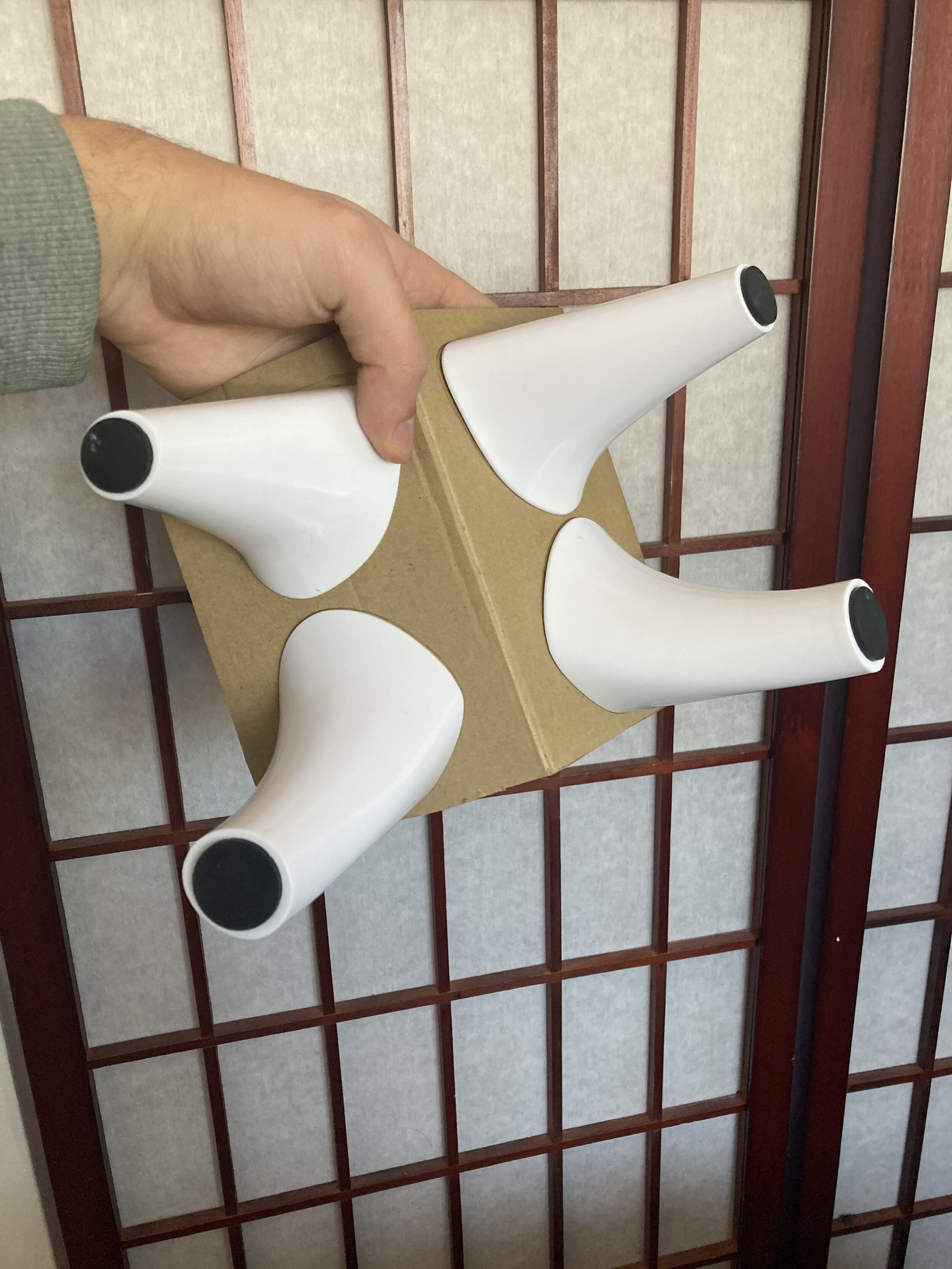
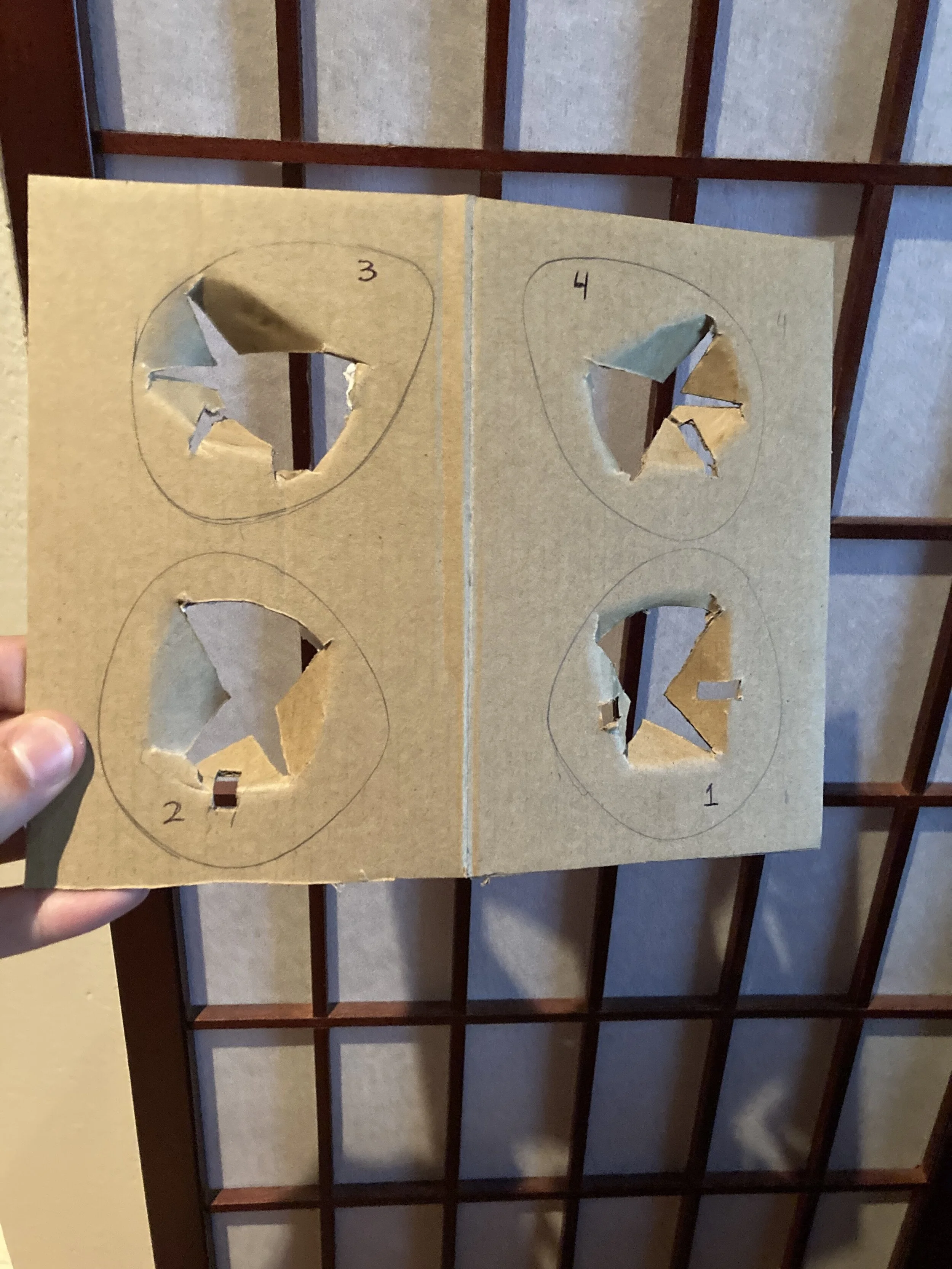

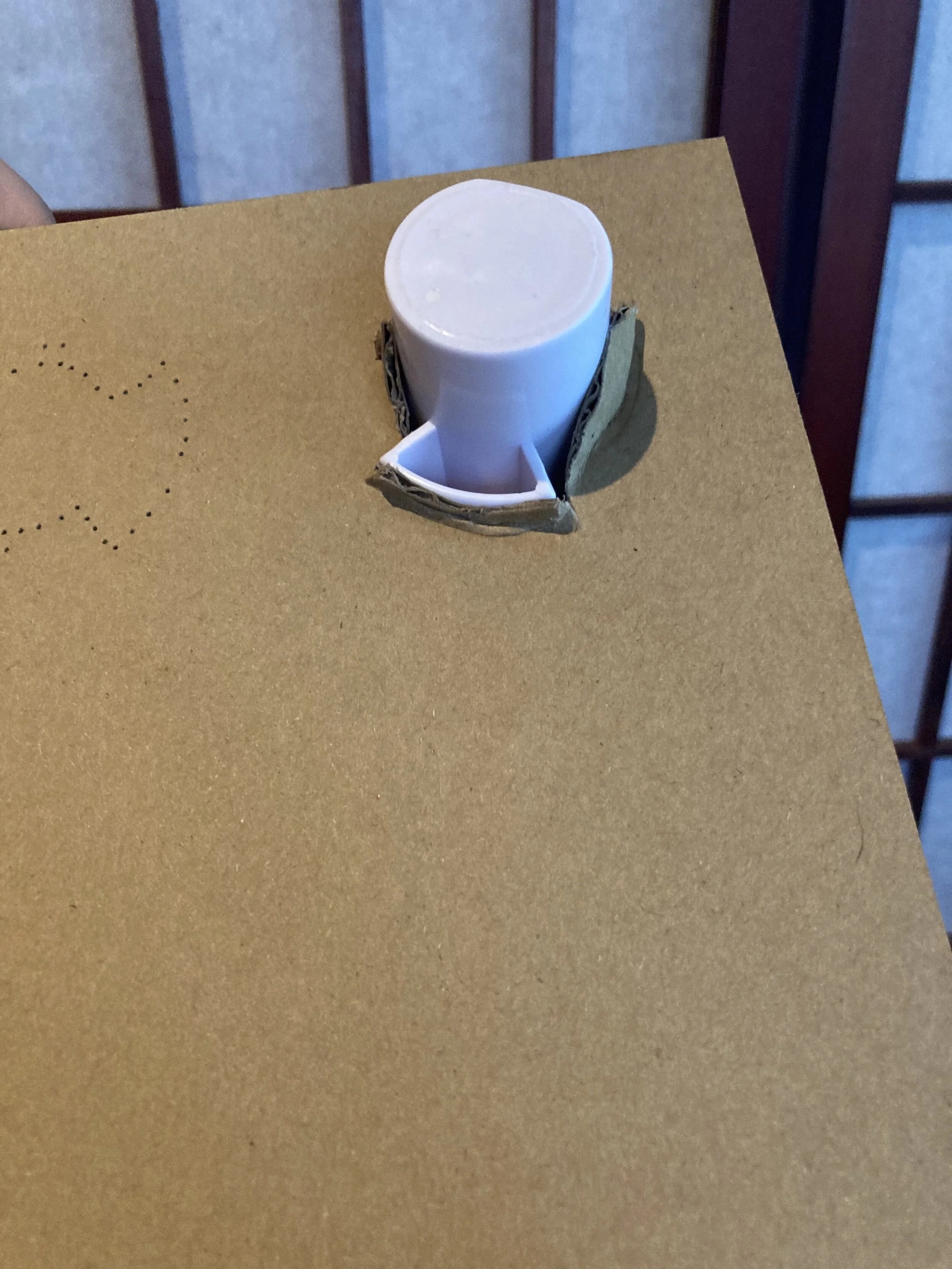
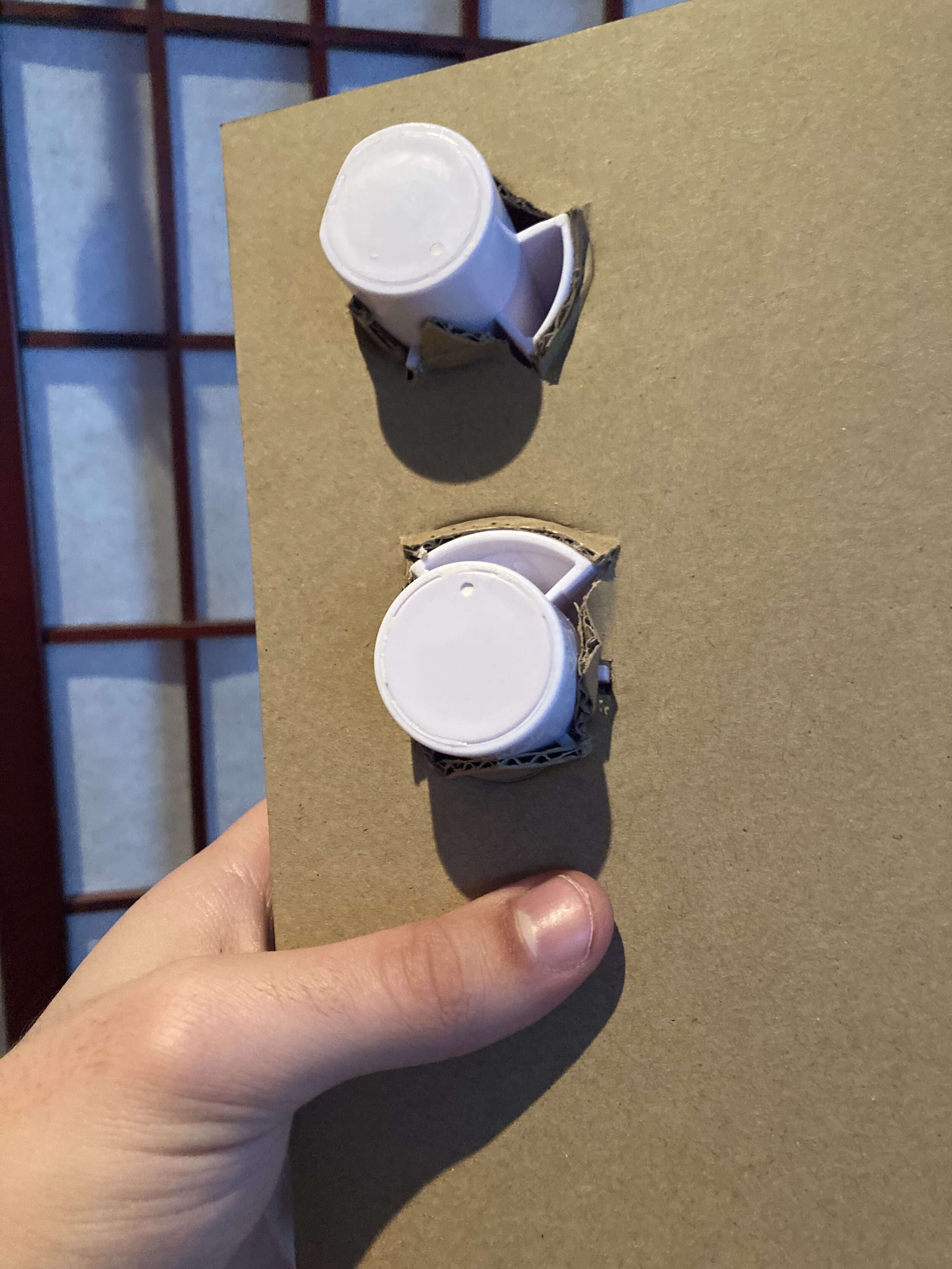
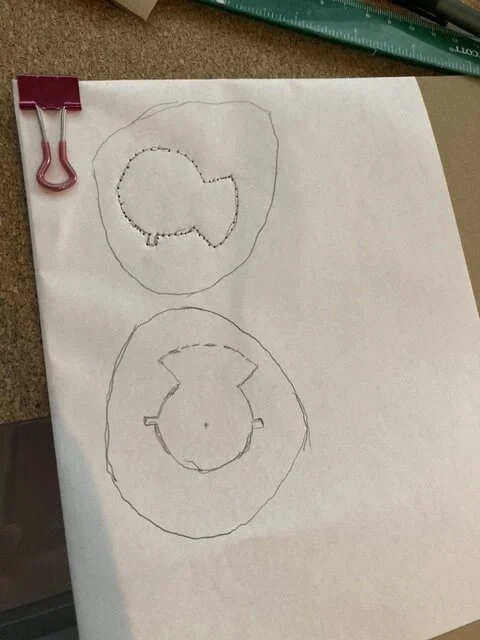
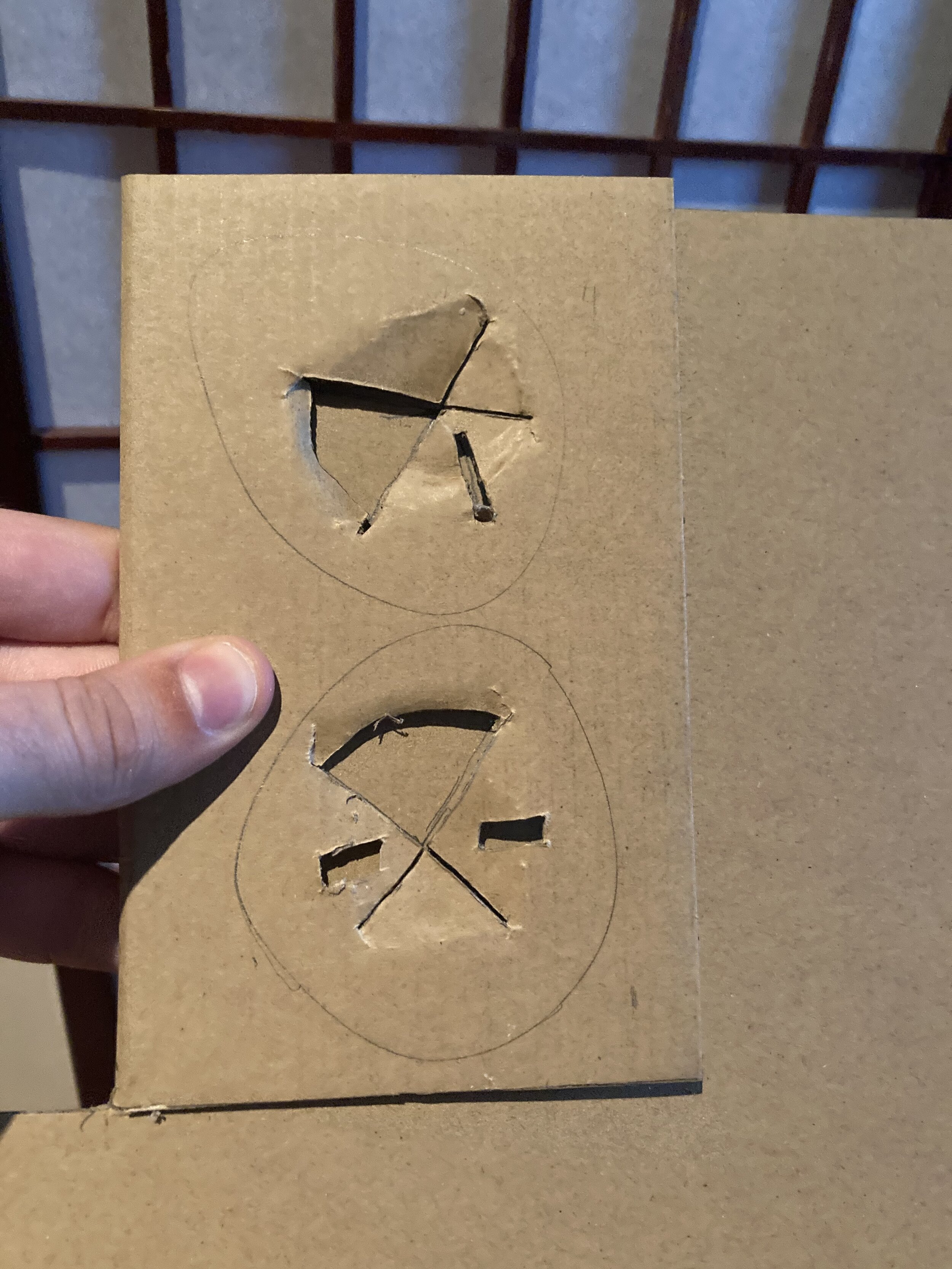
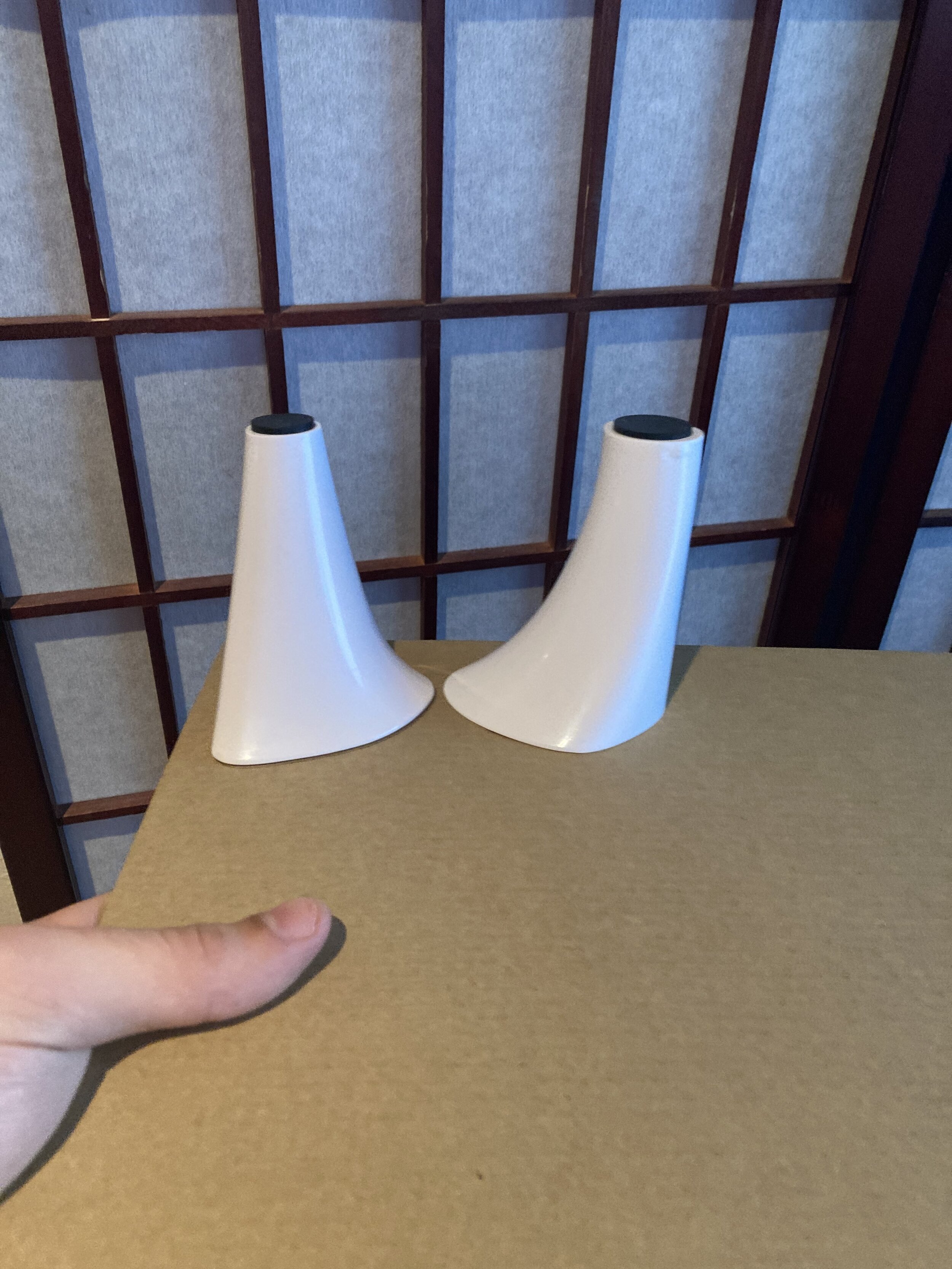
Using SolidWorks and physical mockups, I began the design process by exploring the possible layout configurations with the allowed space. After determining a horn-like configuration was the most effective and sleek candidate to package the legs, I took to modeling clay to choose the optimal placement and orientation angle of the legs.
My first prototype was creased and hand-cut cardboard, with the cut-out geometry allowing only a specific leg in a specific orientation to be inserted. After performing an initial feasibility check with a series of these hand-cut prototypes, I designed and 3D modeled a molded-pulp version. This considered ease of manufacturing and the specifications of molded pulp design. I incorporated four bosses, two per wing with each having it’s own unique pattern. These boss pairs were bridged together to improve the rigidity of the structure. They also possess crush ribs to keep the legs in place once inserted. The piece is molded flat with all bosses being perpendicular; a living hinge was added to allow for this simple to manufacture design. Once molded, the piece can be bent along the hinge to the appropriate packing angle. Embossed by each cavity is the respective leg number. Lastly, crescent lifts were added to promote the unboxing experience.
To present my design and move on to higher fidelity prototyping, I created renders in KeyShot to further garner approval.
Validation and Iteration
Once I received our product team’s and manufacturer’s go ahead, it was time to test the protective capabilities of the design. Using SolidWorks and RDWorks, lasercut prototypes were made. Drop and vibration tests were then performed according to ASTM standards. The results were documented, and adjustments were made for following iterations. The major flaw was a lack of constraint as the hinge had a range to bend within. Additional flaps and living hinges were added to maintain the same cost-friendly design, effectively constrain the legs, and provide extra rigidity to the structure.
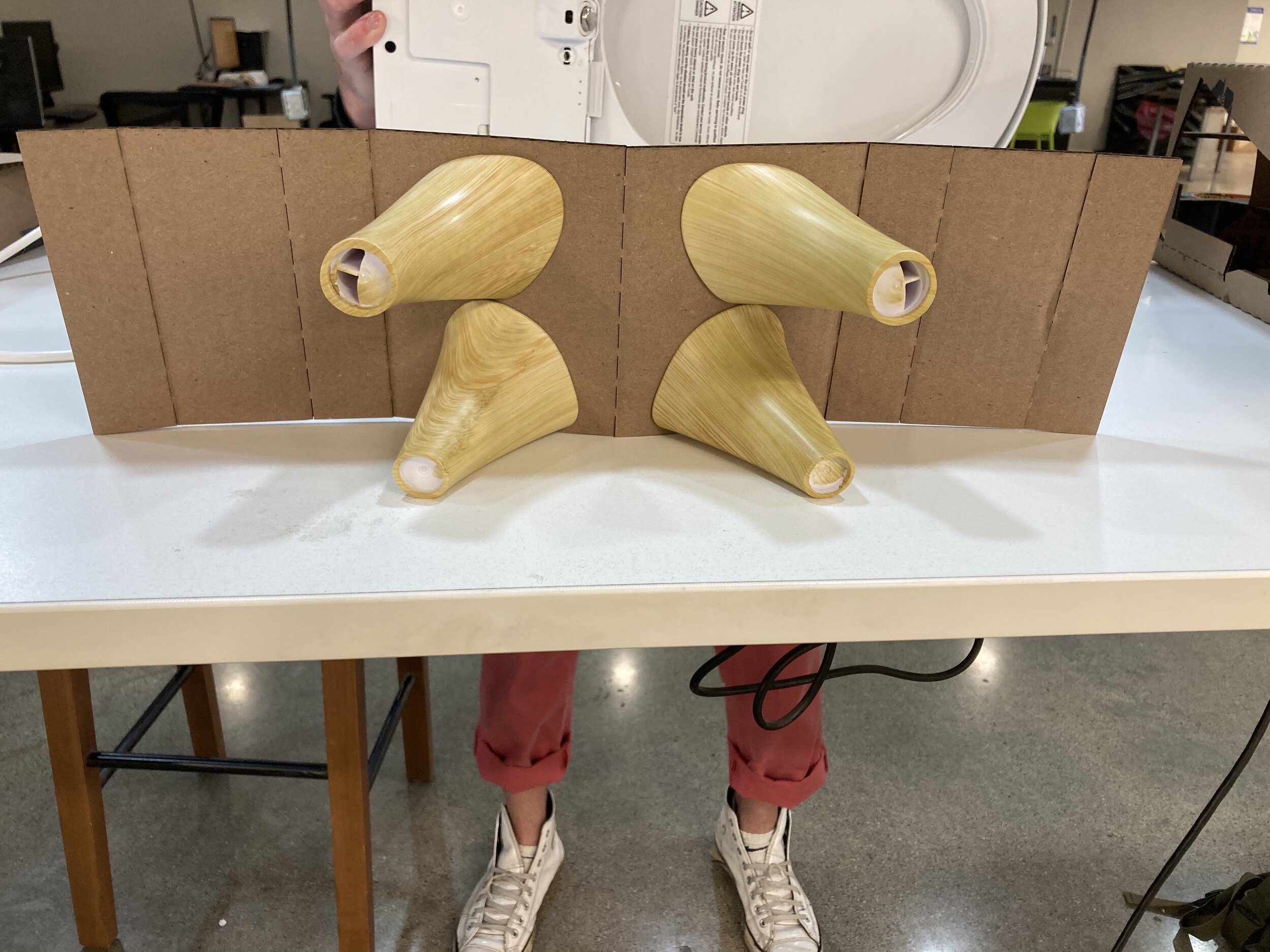
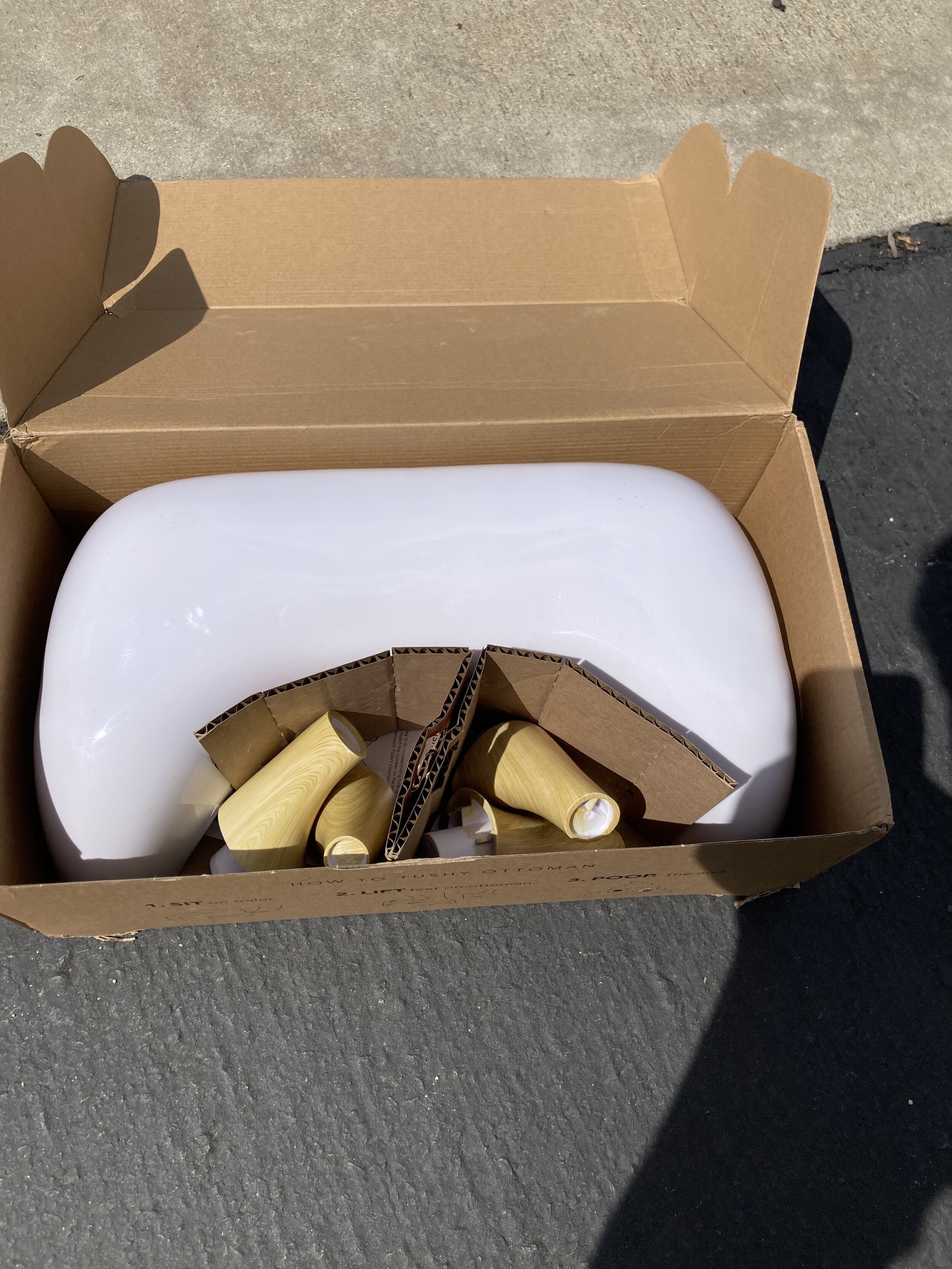
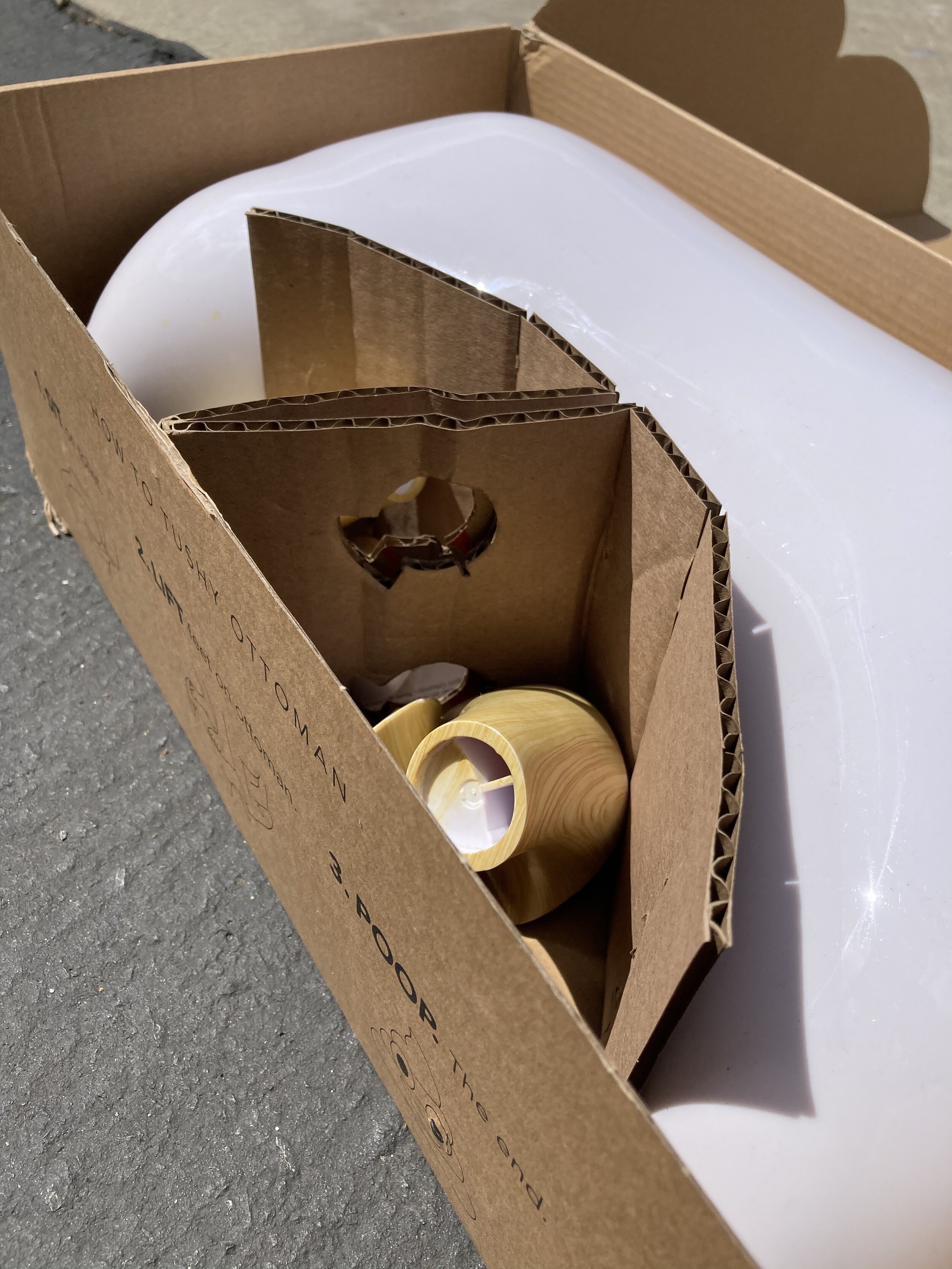
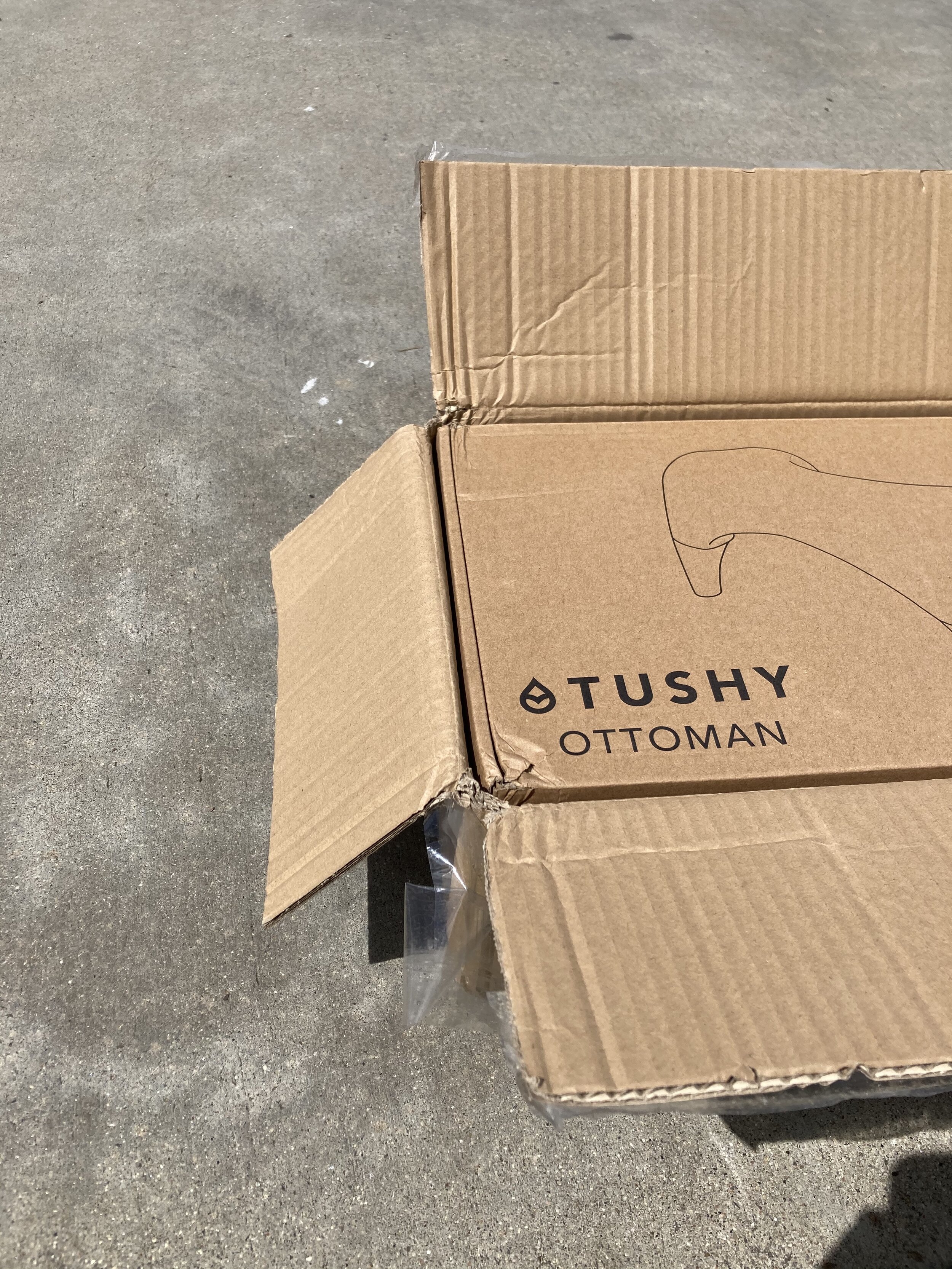
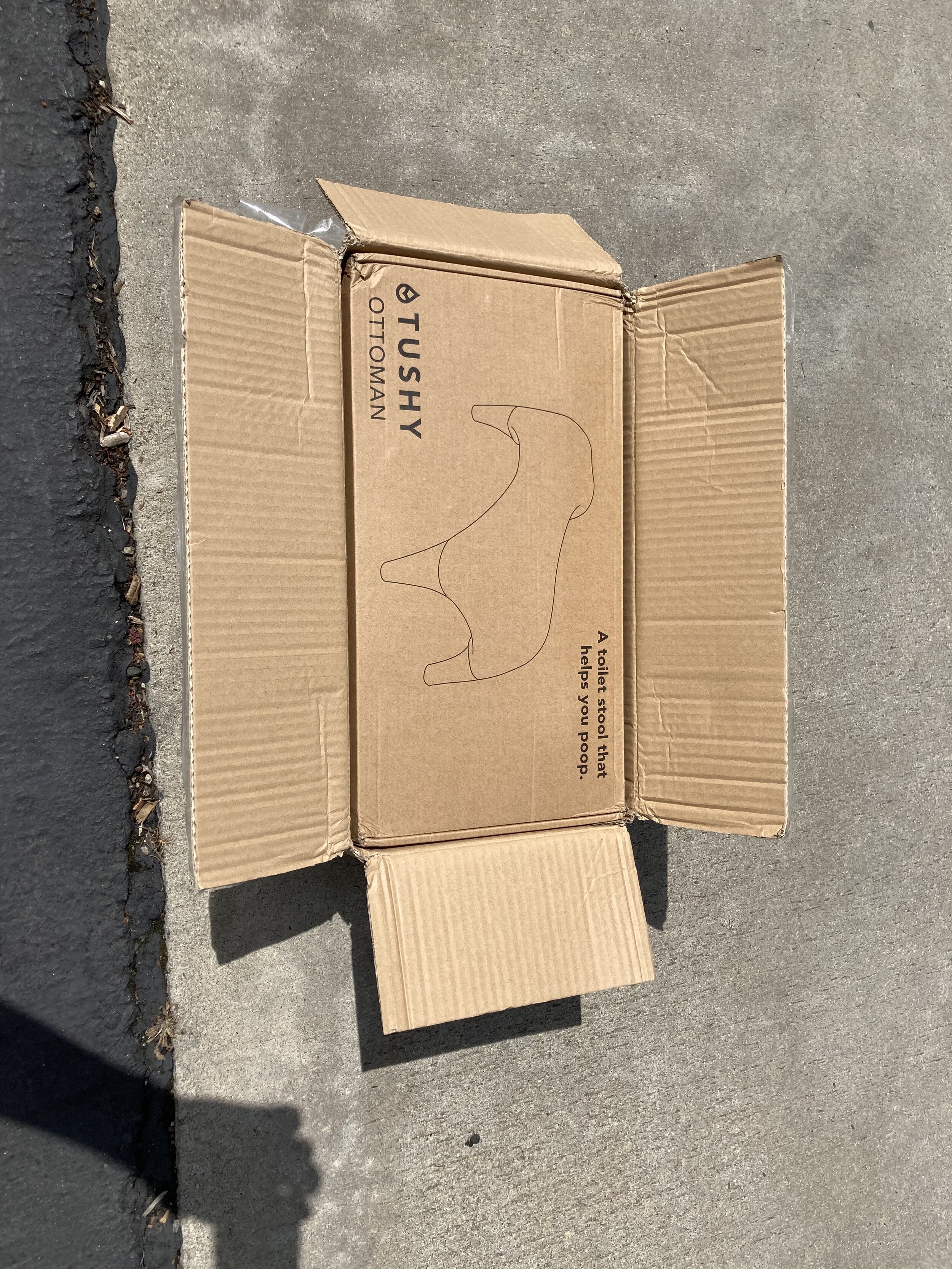
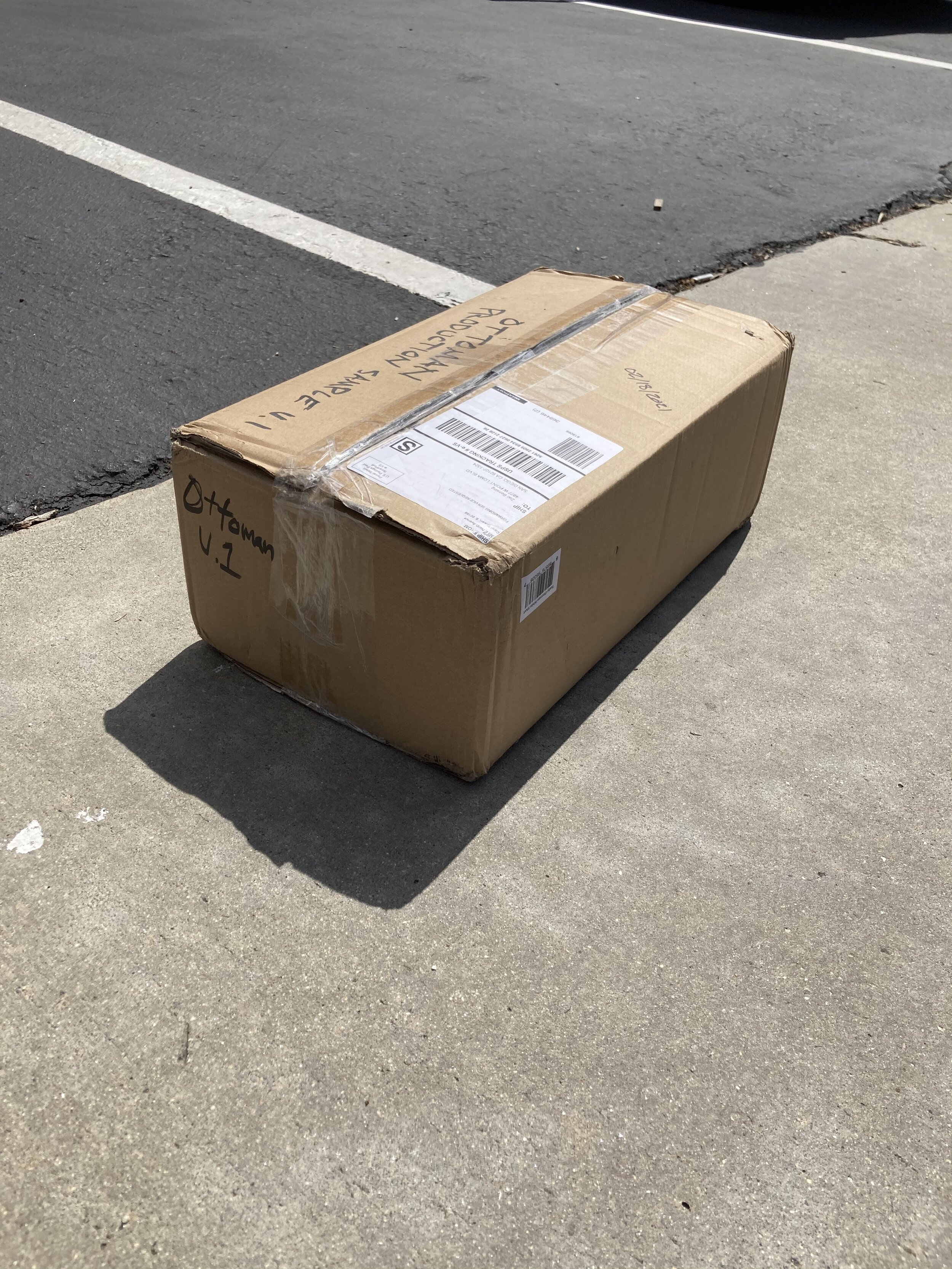
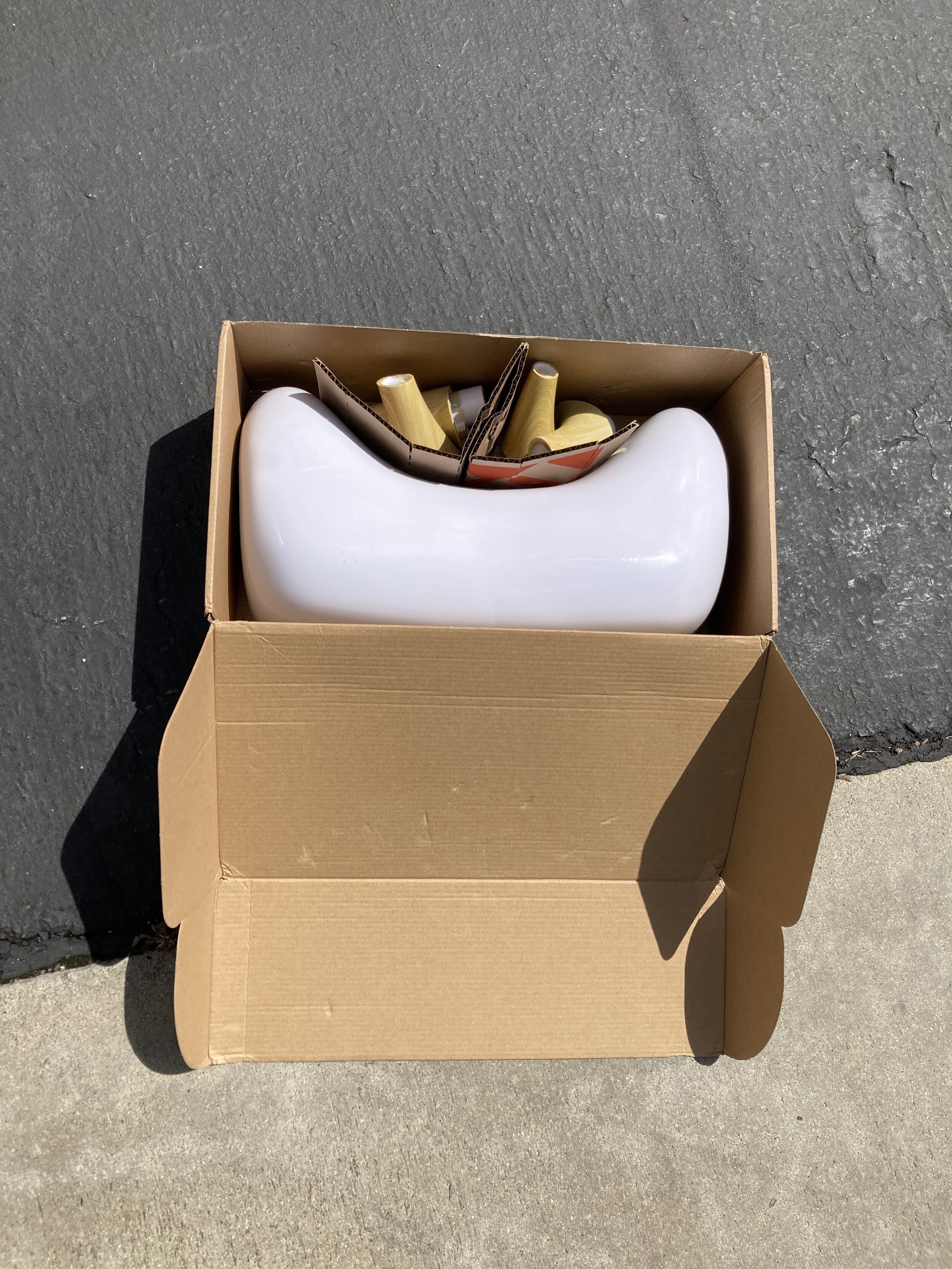
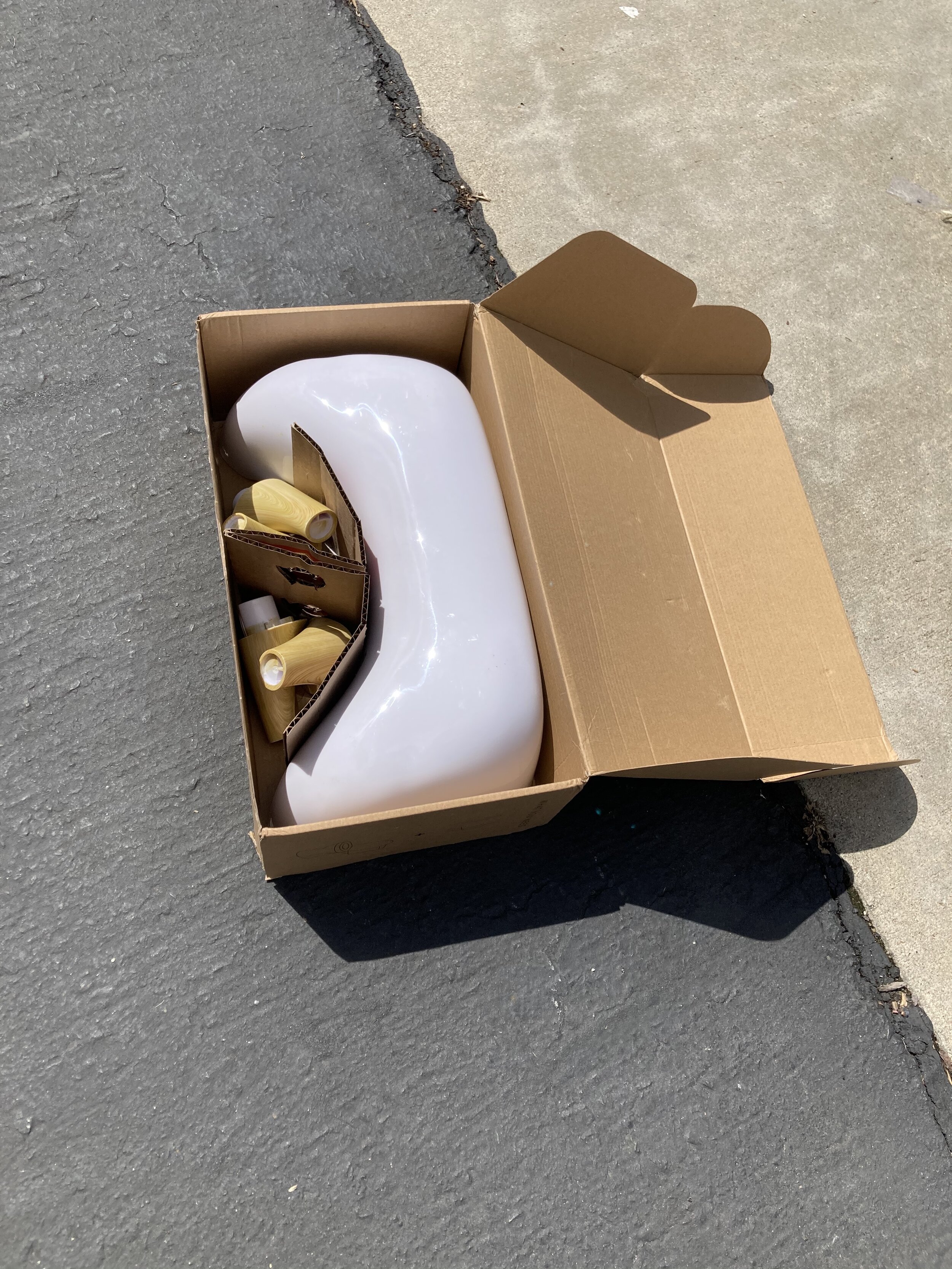
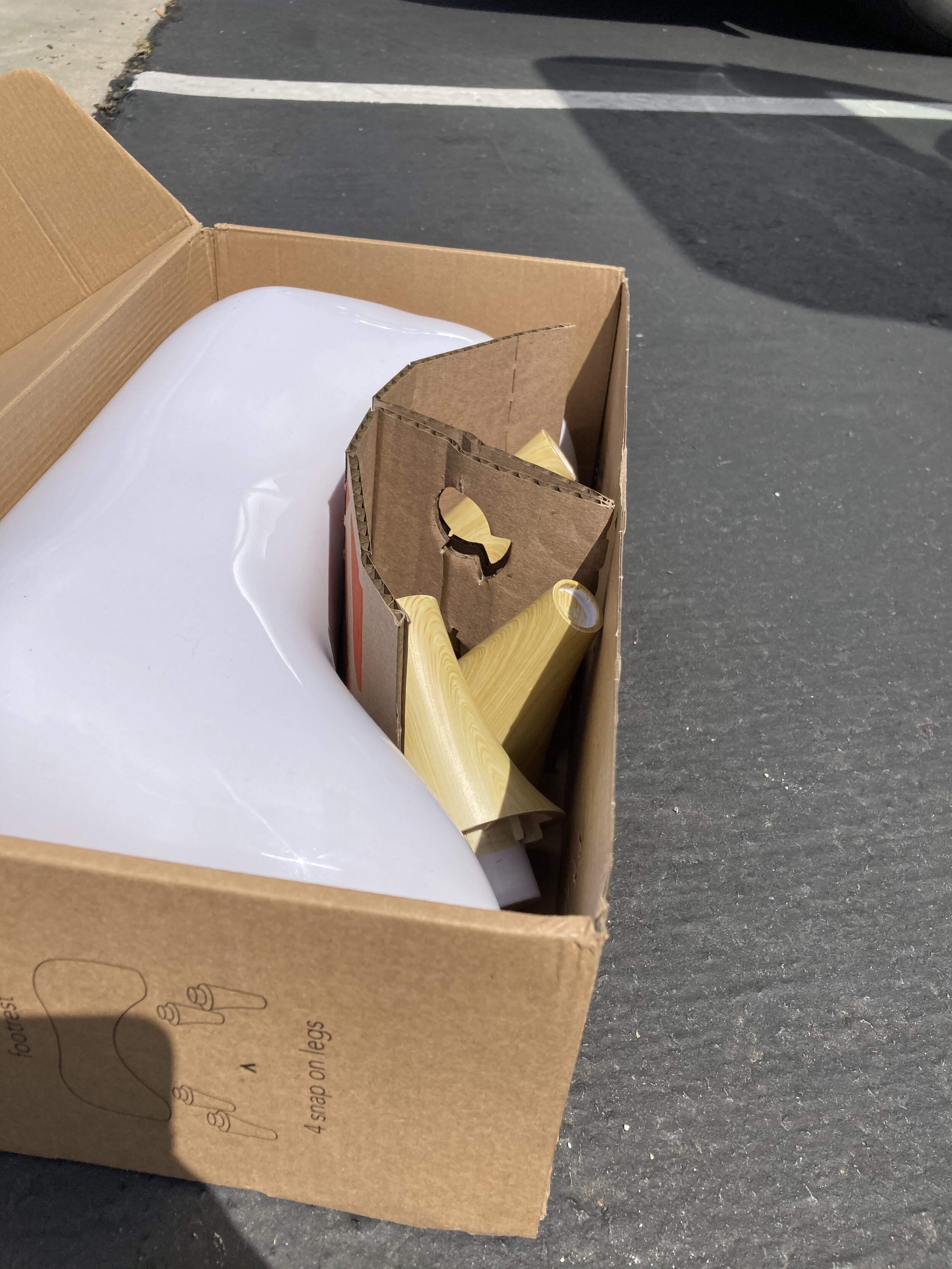
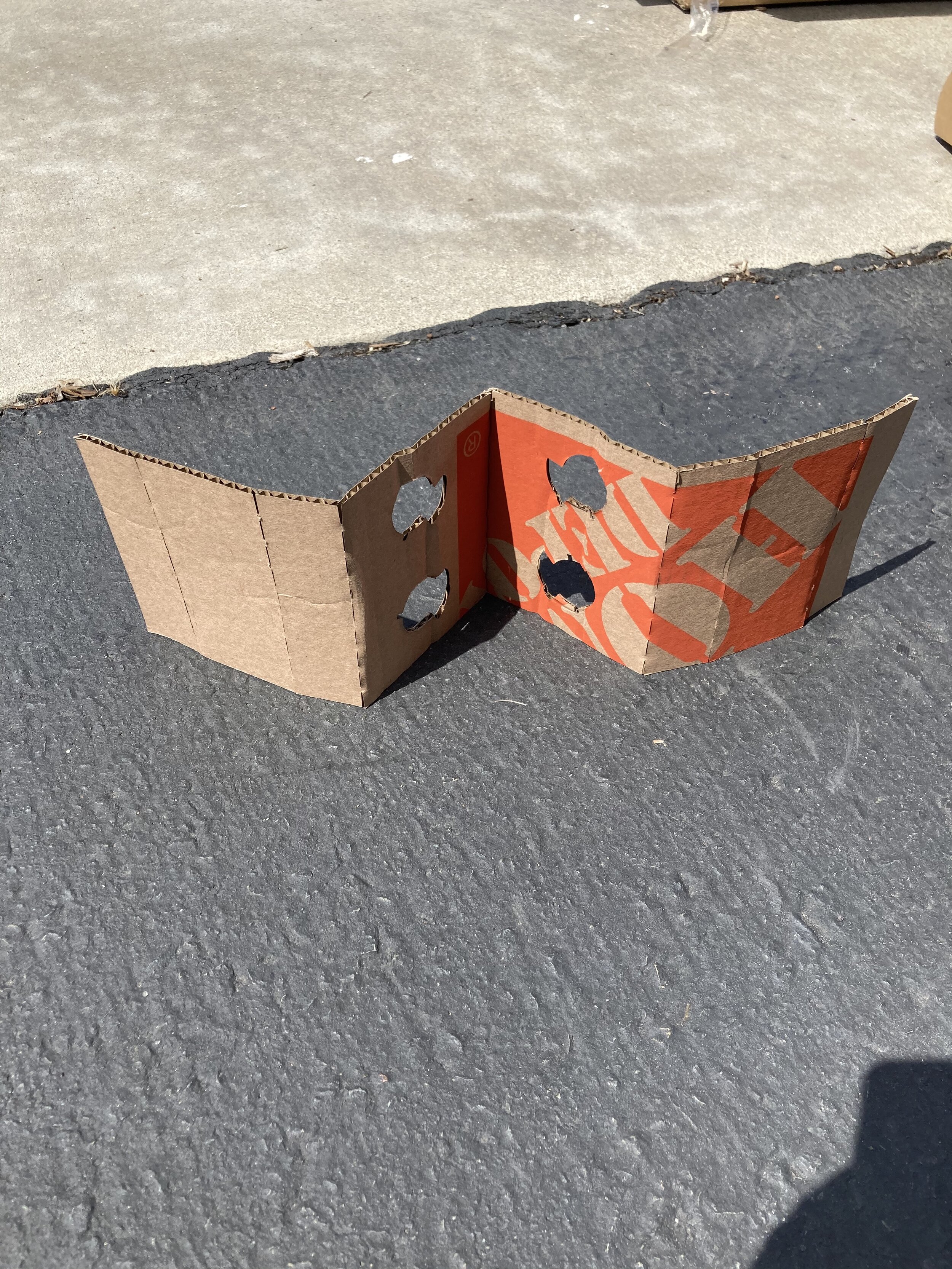
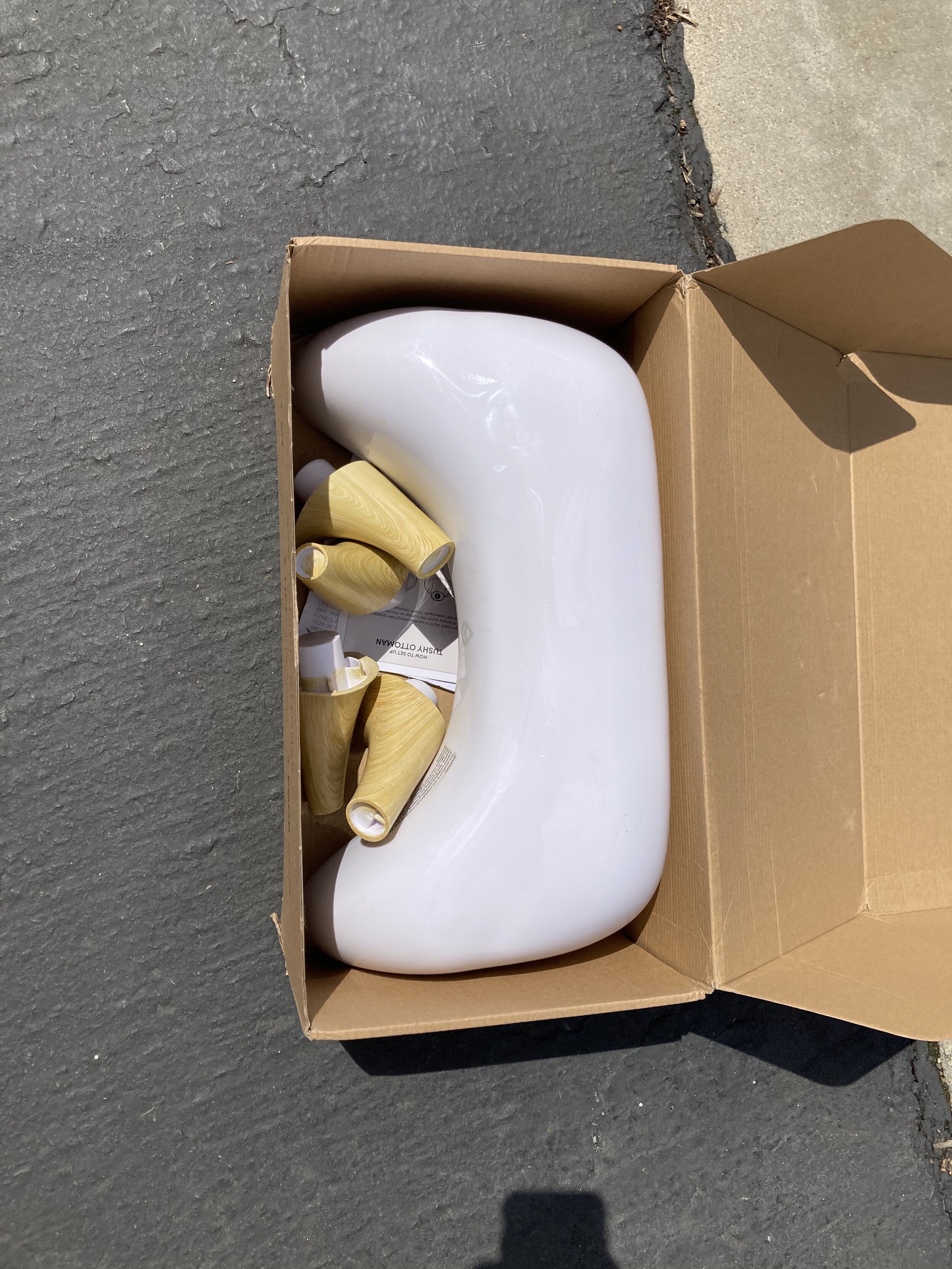
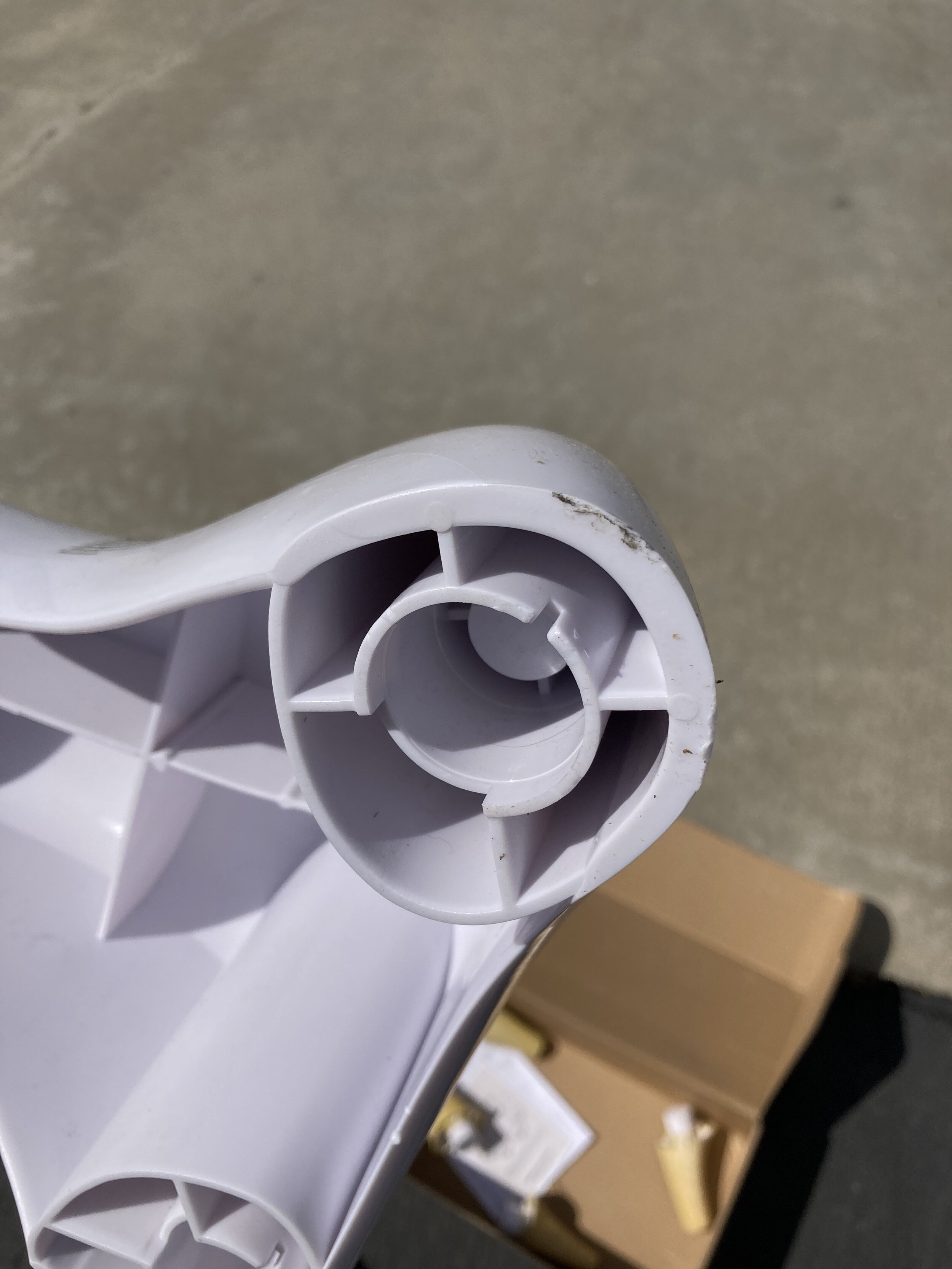
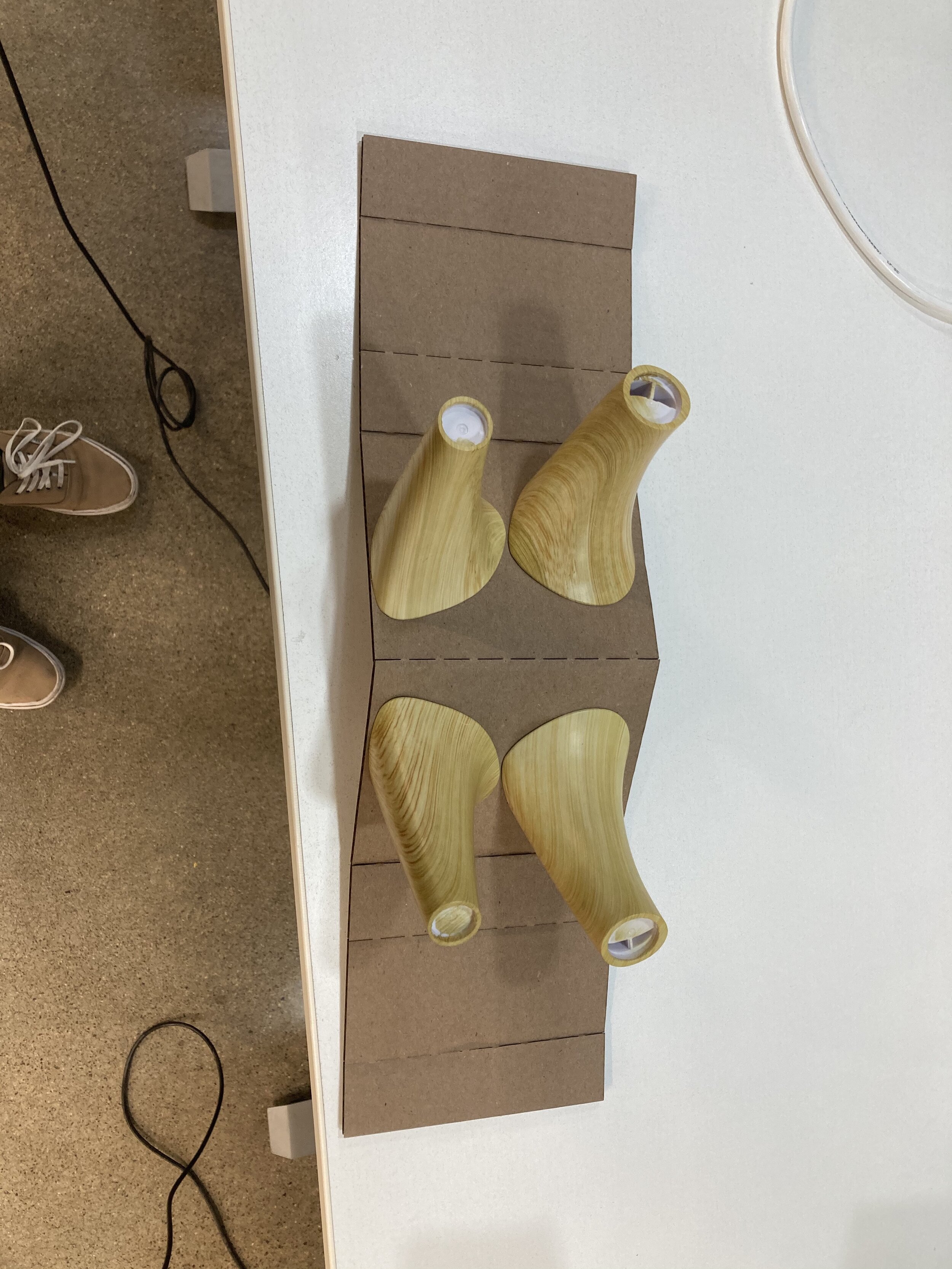
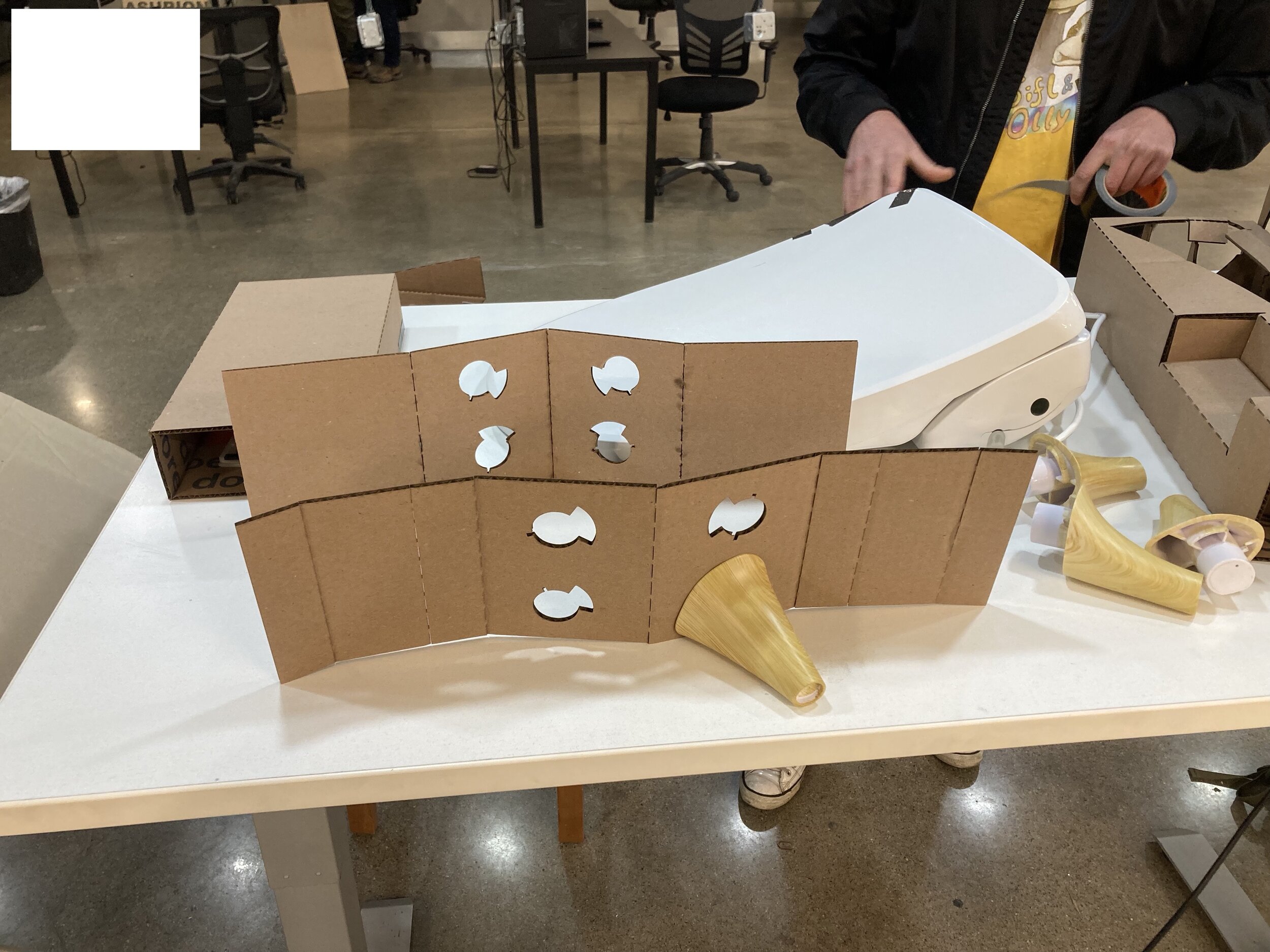
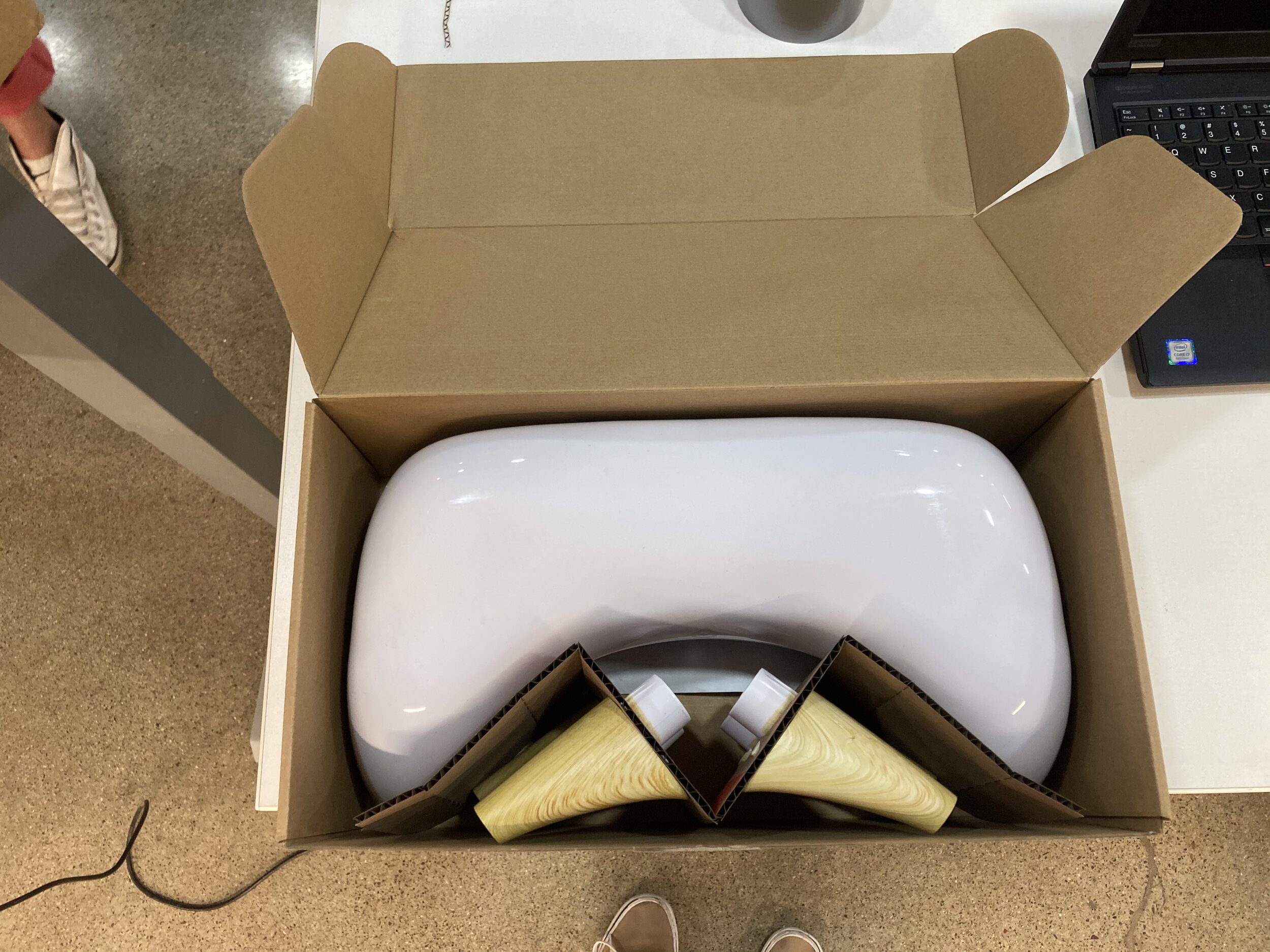
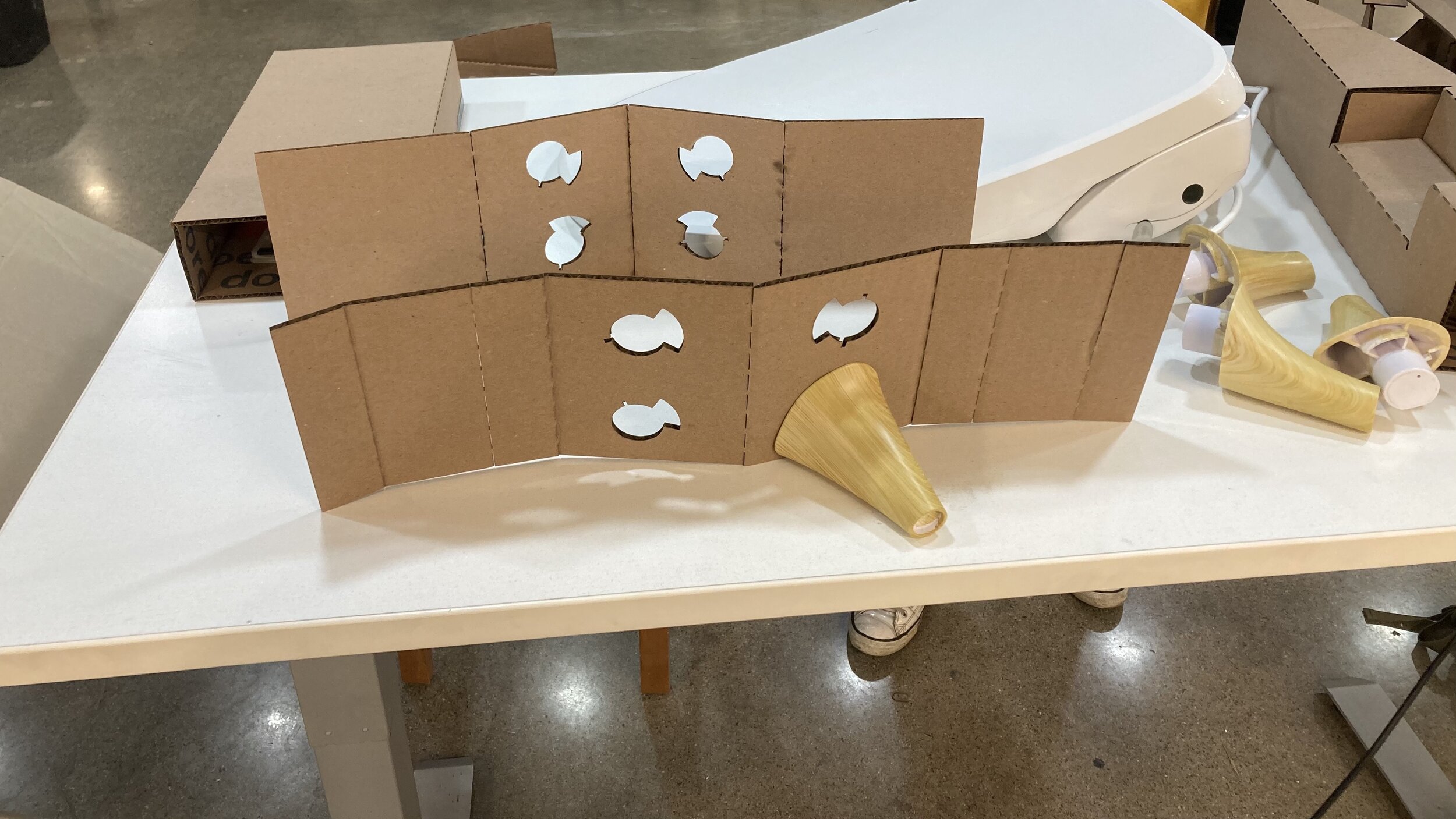