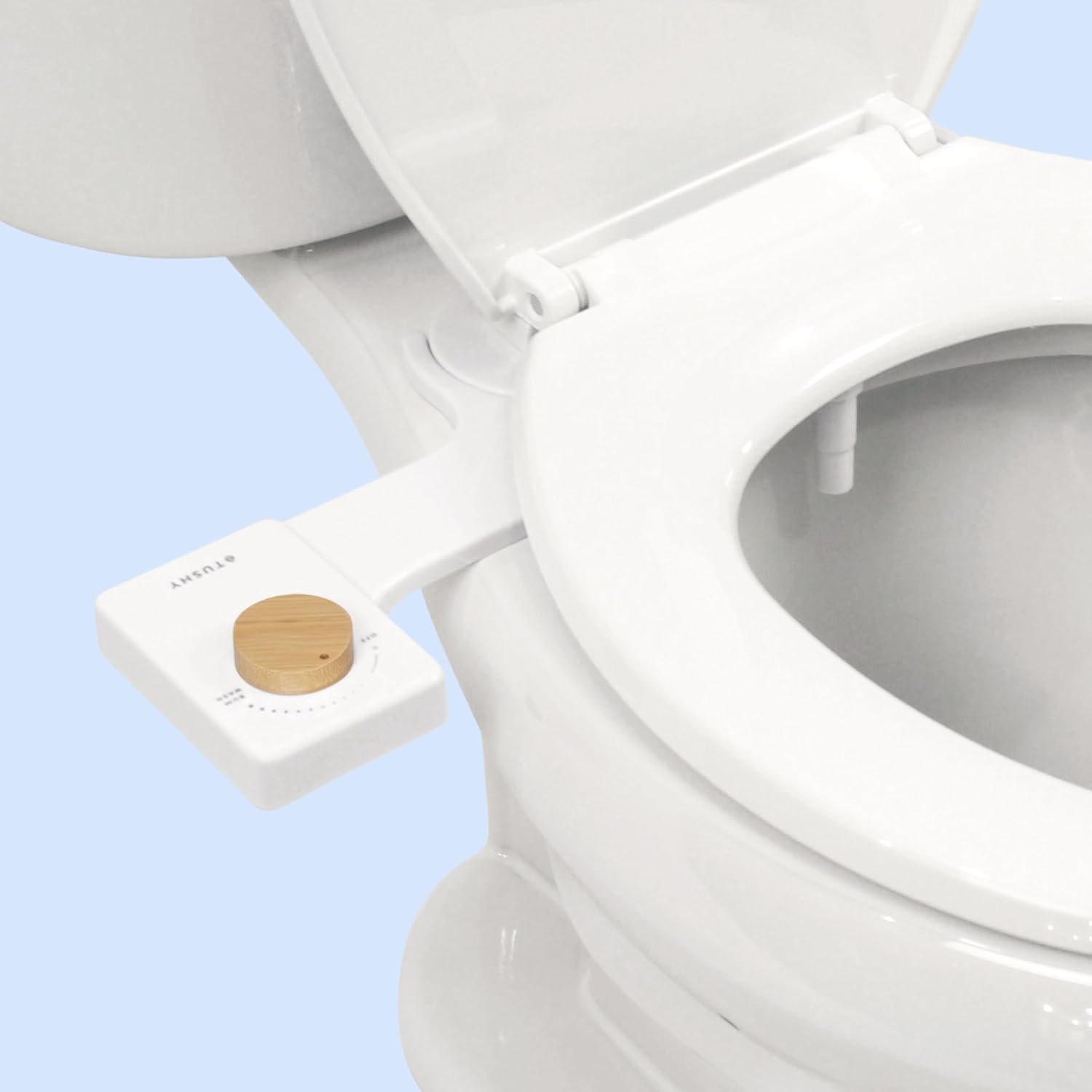
Hello Tushy
Position: Product Engineer
Role: Research, Design, DFM, Quoting, Prototyping & Validation
Project Timeline: Jul 2022 - Jul 2023
Tushy Fresh
Tushy is a premium bidet brand. As such, it’s products are at a higher price point than it’s competitors. After conducting market research, it was found 80% of bidet attachments were sold under the $50 price point. To compete with this market while maintaining the brand’s premium aesthetic, Tushy Fresh was born.
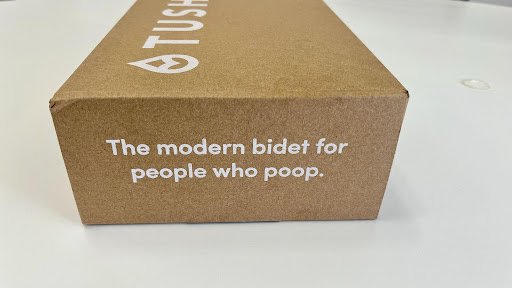
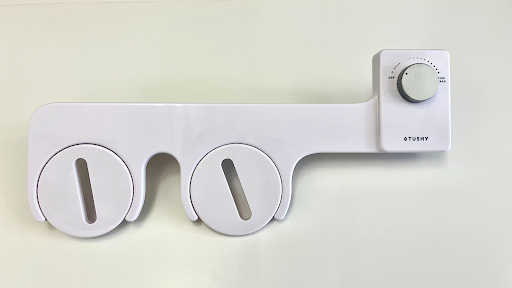
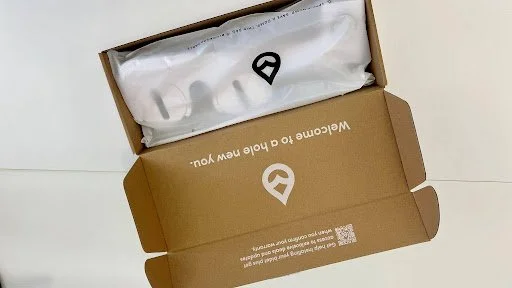
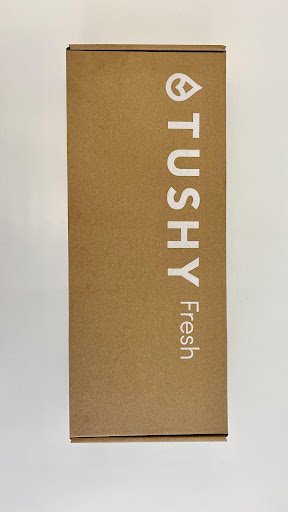
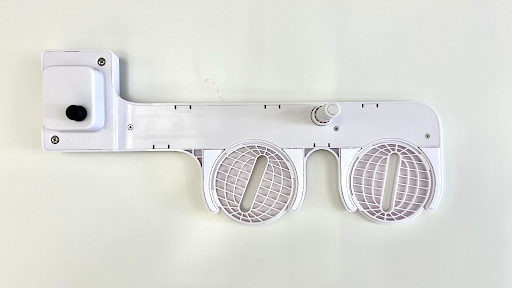
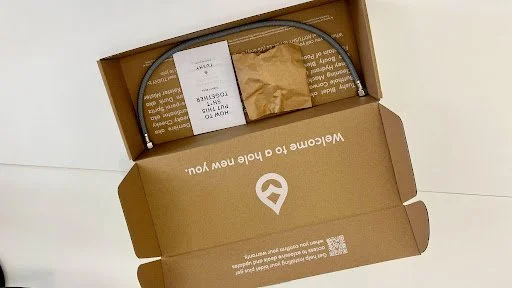
Overview
The Tushy Fresh is an entry level bidet attachment intended as a low cost option to the bidet naive and curious. This is a new product that is simple, intuitive, and minimizes cannibalization with other bidet products of the Tushy suite. It is a one-temperature cool water model of bidet with a slim console and single angle stream.
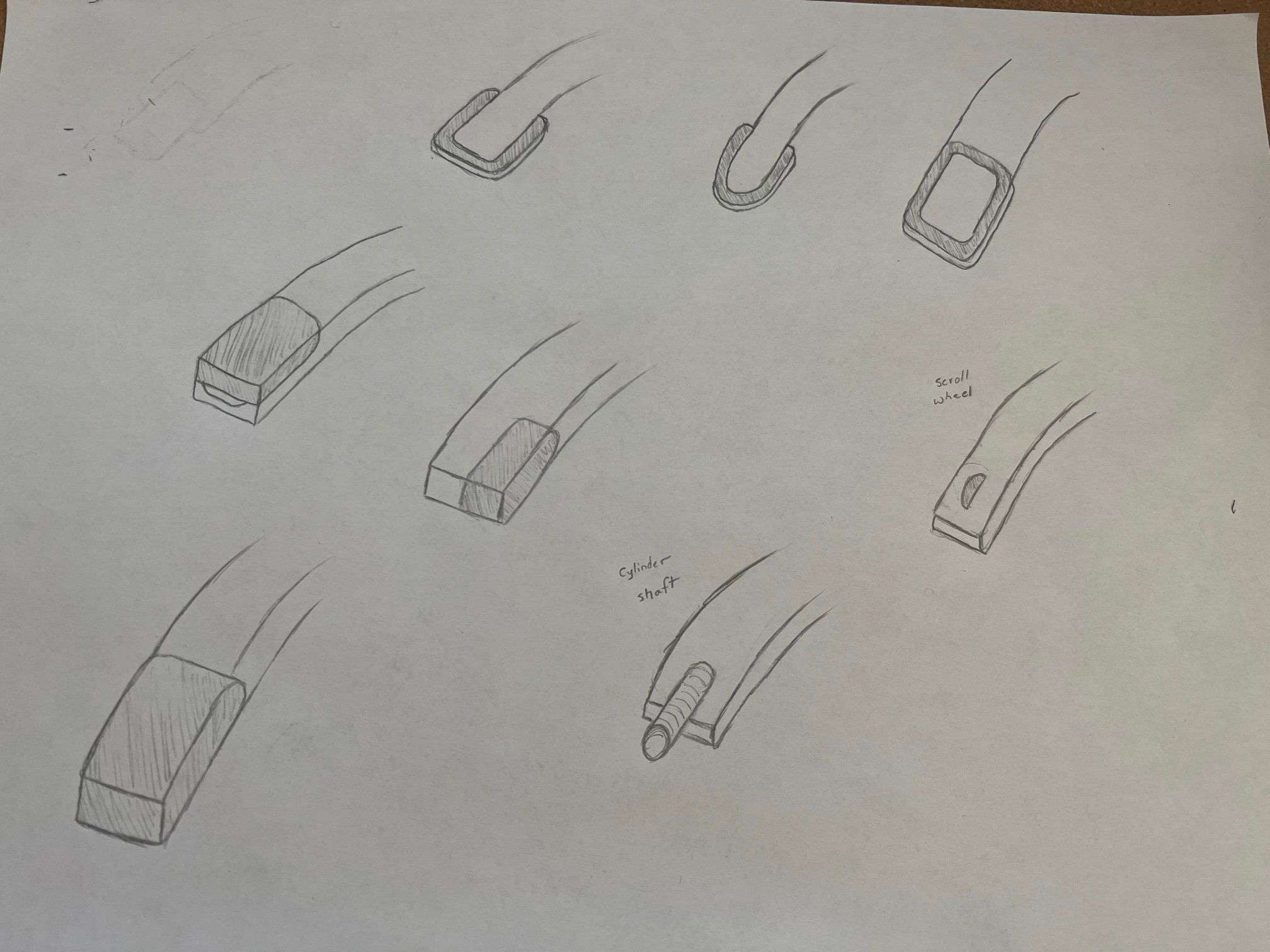
The Concept Phase
Ultrasonic vs Hardware Construction
The first decision to be made was whether I would employ ultrasonic welding for this product. Initially, ultrasonic welding was an extremely appealing implementation as it would allow for a slightly slimmer body design as well as fewer components. This was my preference until I got my hands on some water products that employ ultrasonic welding. It was here where I became uncomfortable with the durability and reliability of the process. The products with ultrasonic welding were offputtingly flimsy and were prone to leaking when bent. Additionally, our manufacturers did not have a great breadth of experience in this manufacturing process which depleted my confidence. As a brand with a reputation for robust and premium products, it was a clear decision to go with using hoses and hardware for the Tushy Fresh.
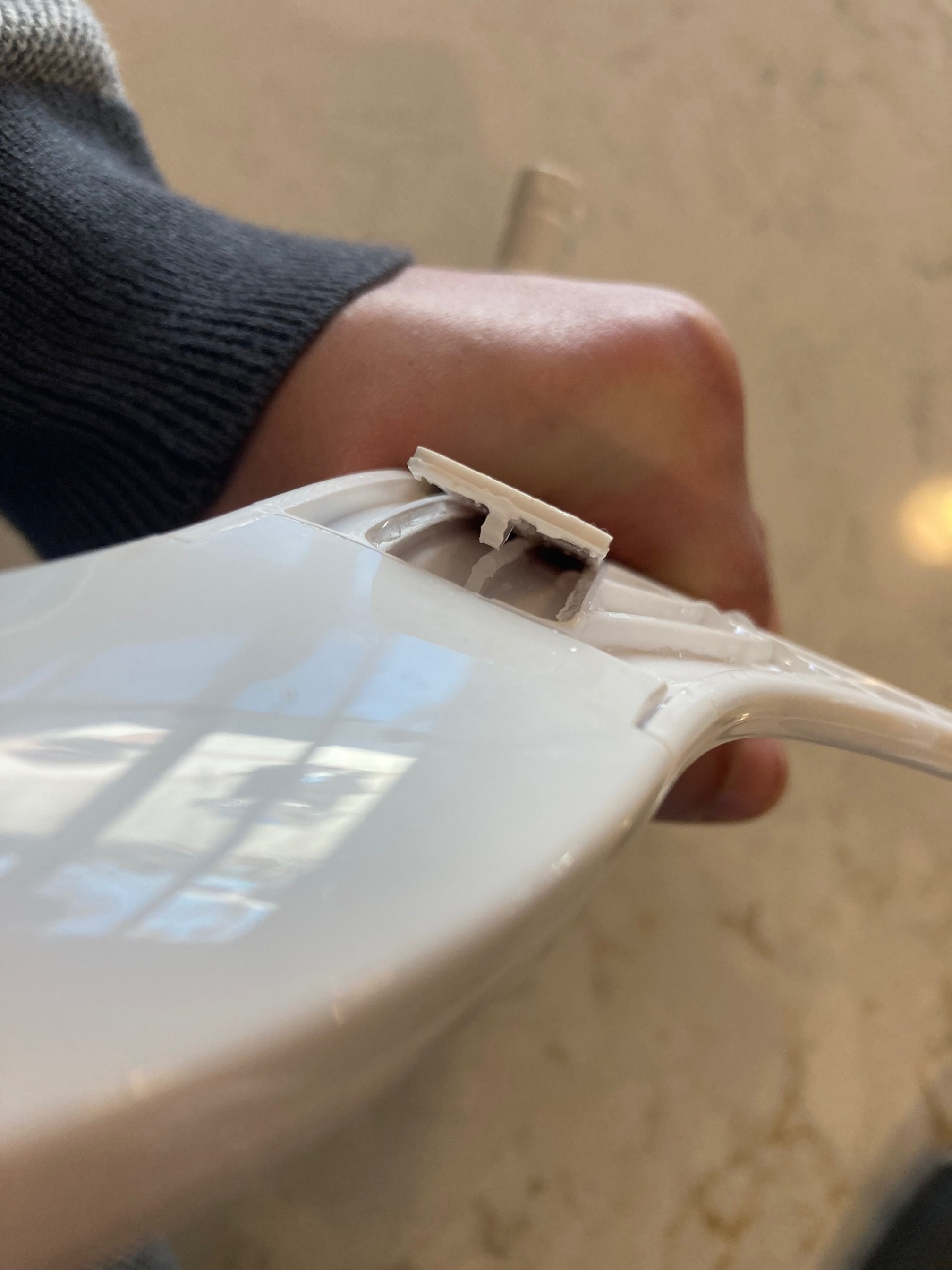
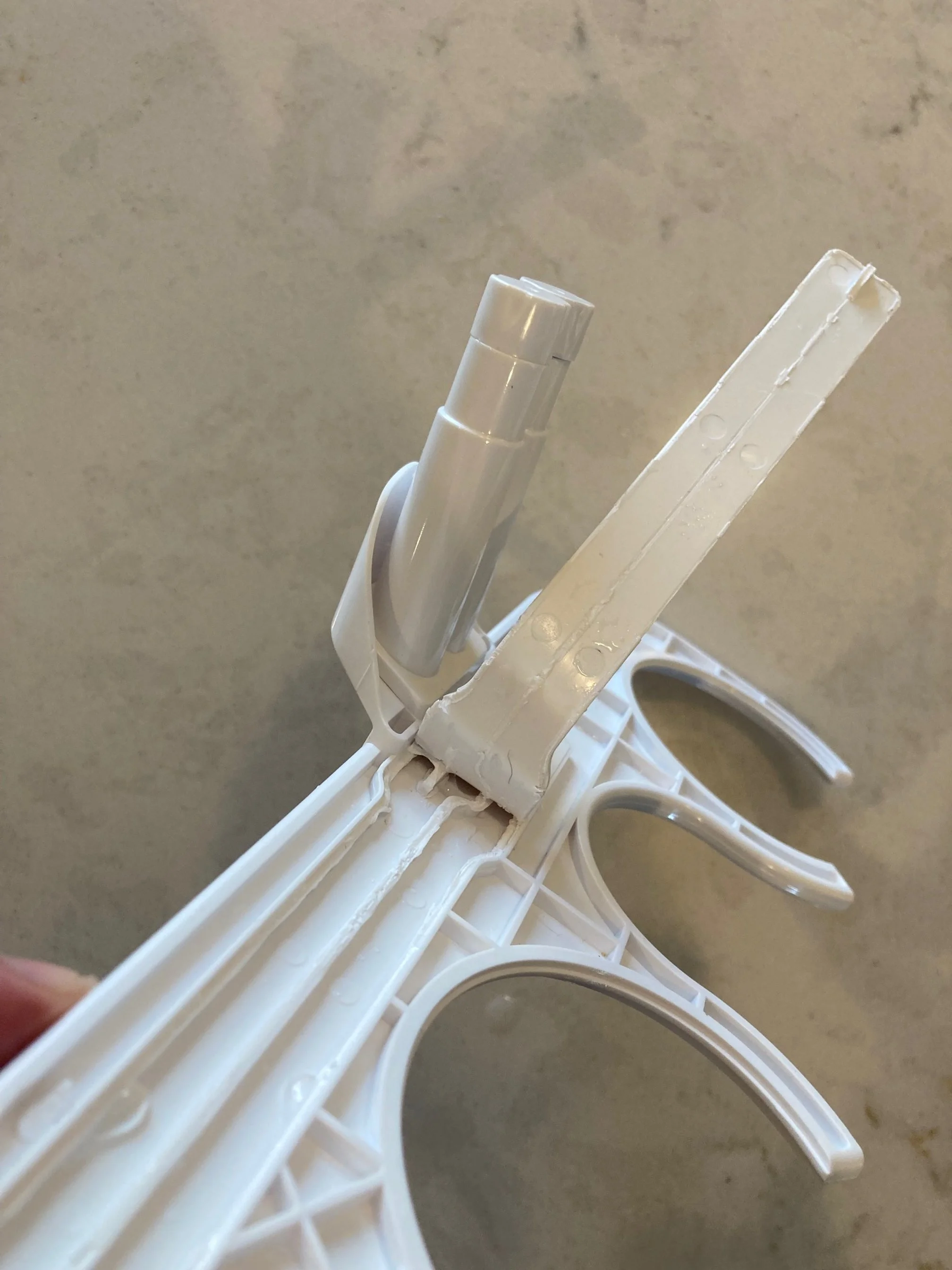
Console Design
Console design is often the differentiator at the point of purchase. It is essentially an appendage sticking out of your toilet. It is quite the challenge to make it look normal. An elegant console changes the mindset of “What is this weird medical device” to “I want to try that!”
There were two main considerations when designing the console: Aesthetic and Interaction.
The first consideration to tackle was the interaction. Many people are buying their first bidet or are encountering them for the first time. It is imperative that the console is intuitive so you don’t need a posted instruction manual to figure it out. Bidets are still widely taboo in North America. Eliminating pain points such as confusion are necessary for the widespread adoption of bidets. Additionally, the bidet needs to be easy to actuate.
I took inspiration from airplane throttles and began mocking up a paddle/lever actuator that is spring loaded. These low fidelity prototypes were great to get a sense of the interaction in mind.
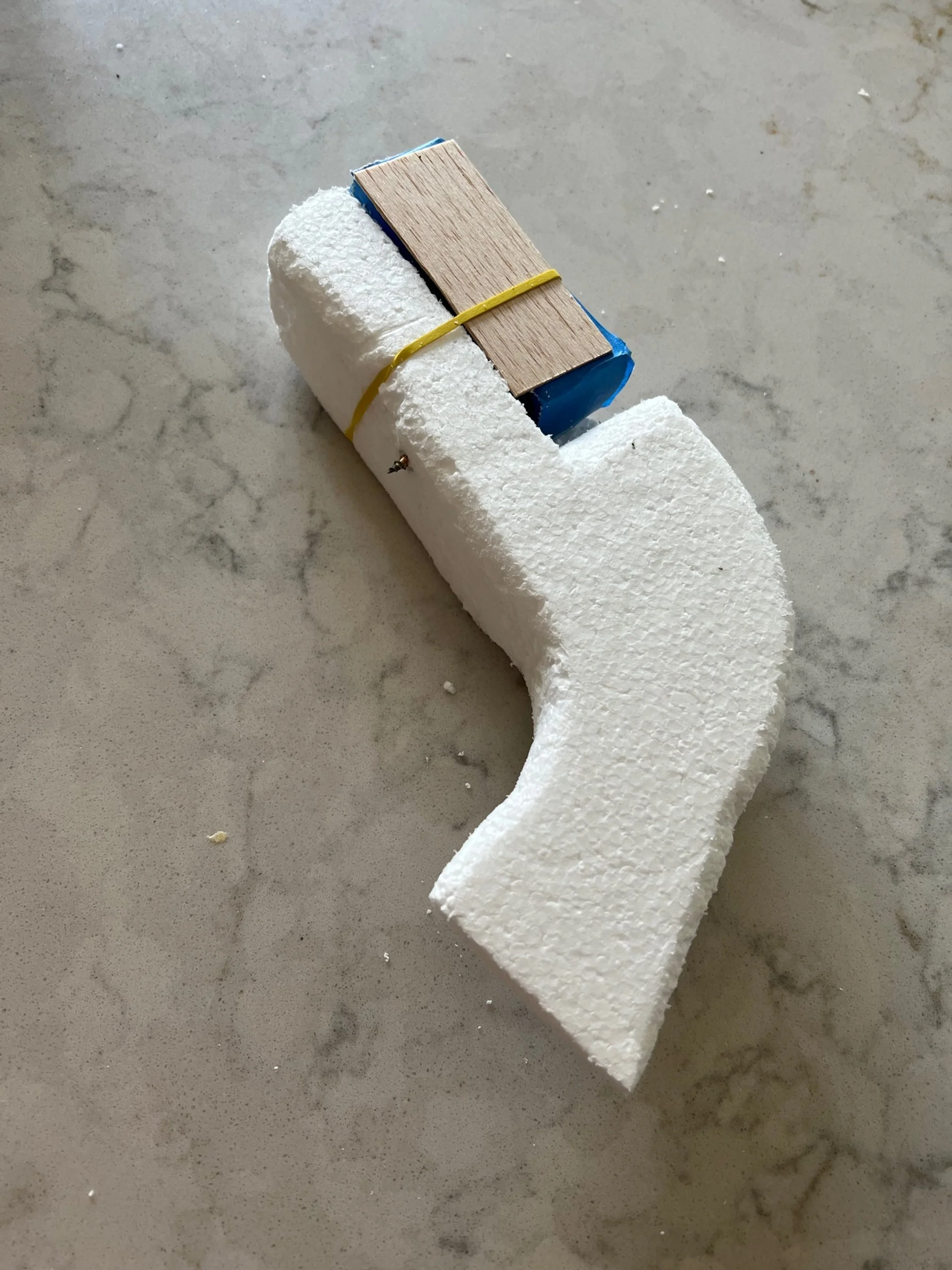
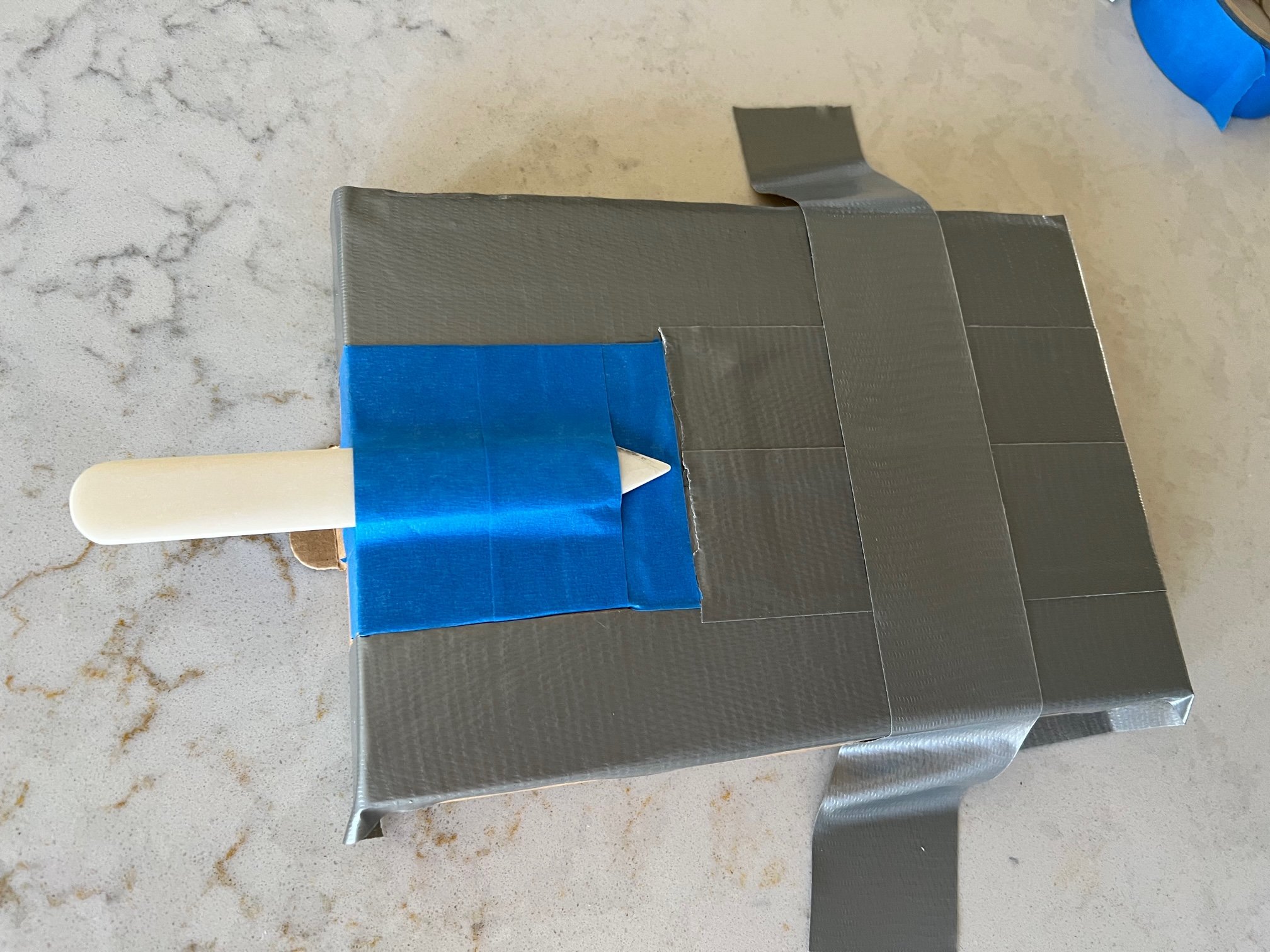

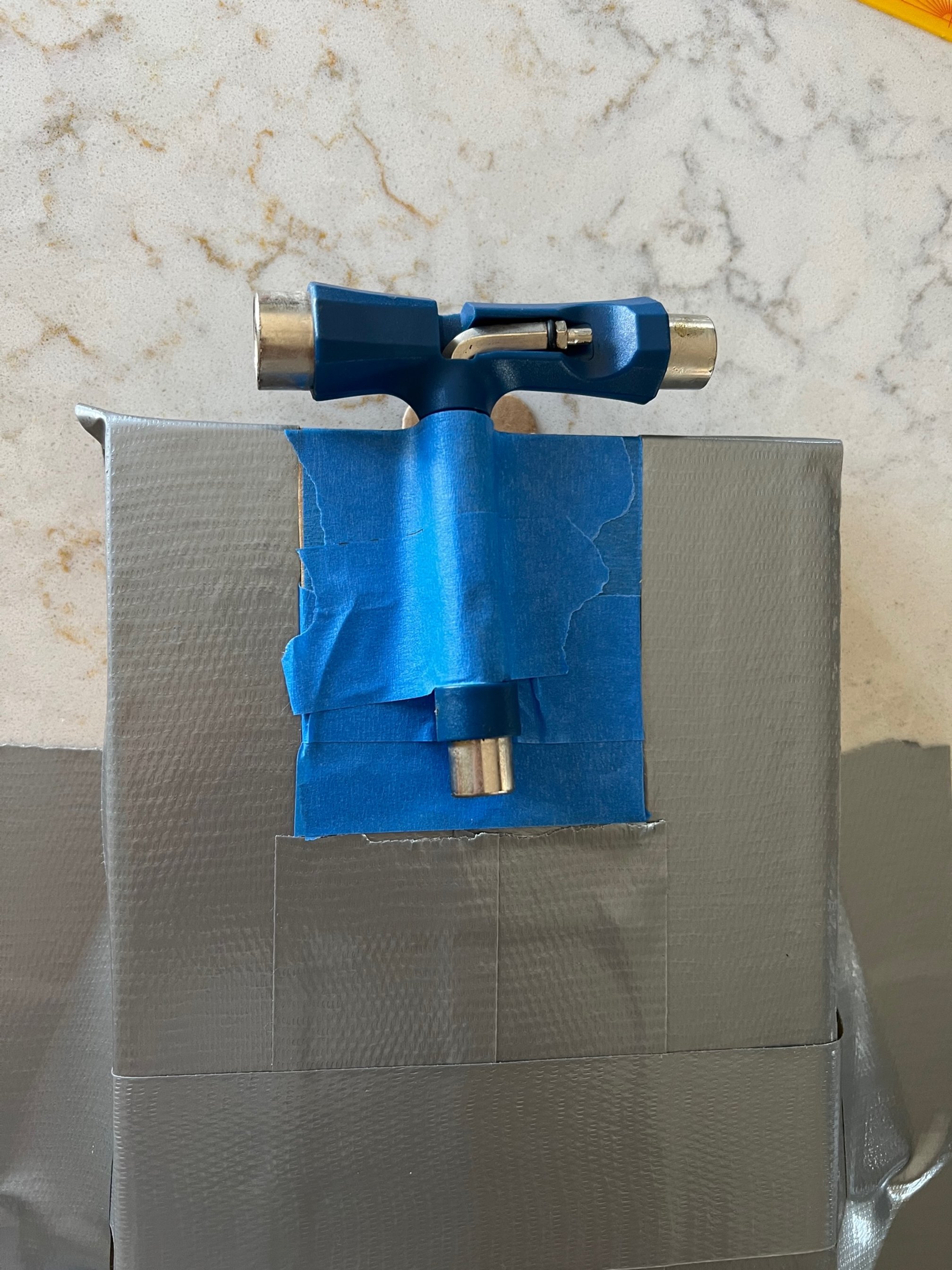
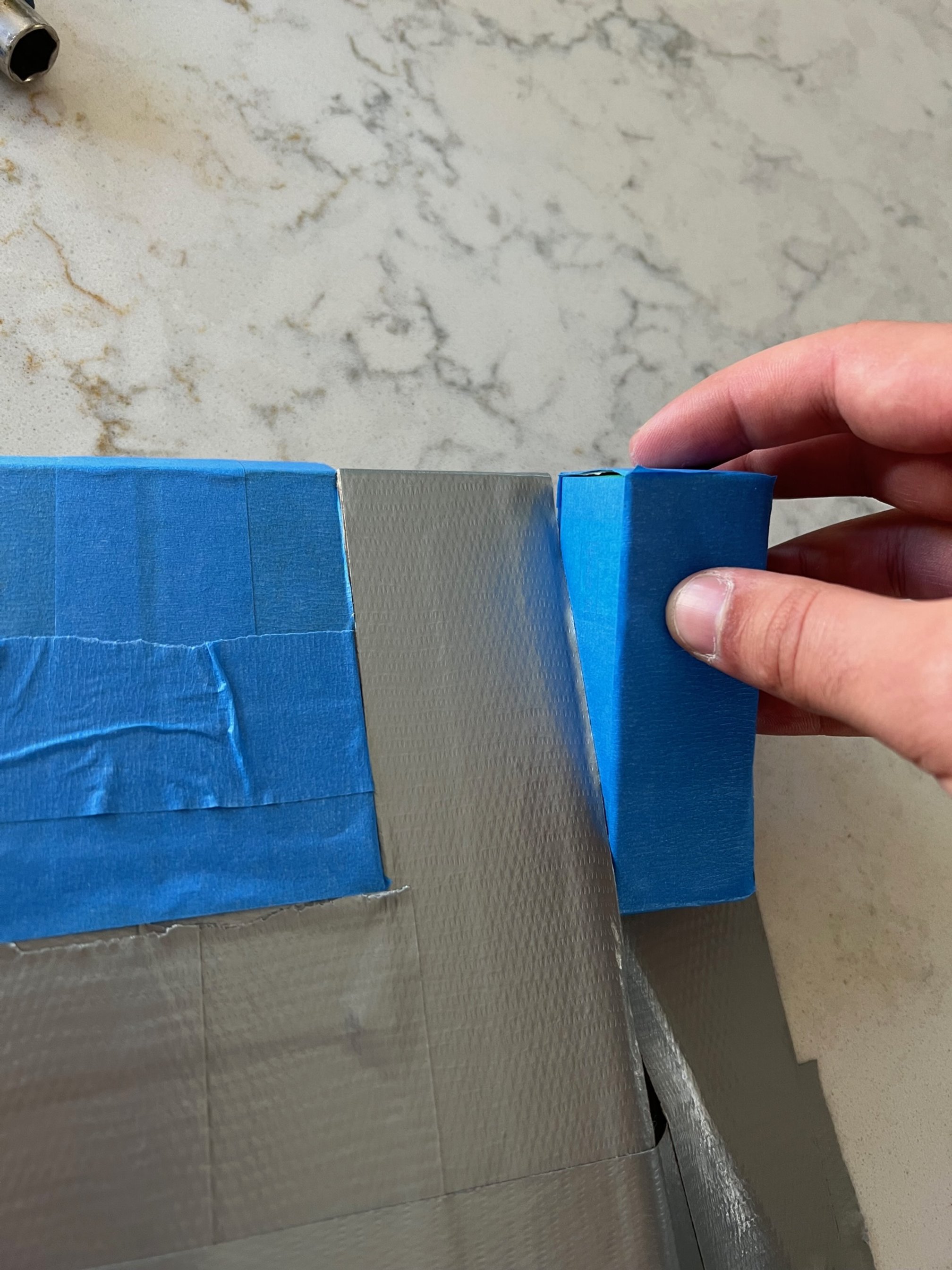

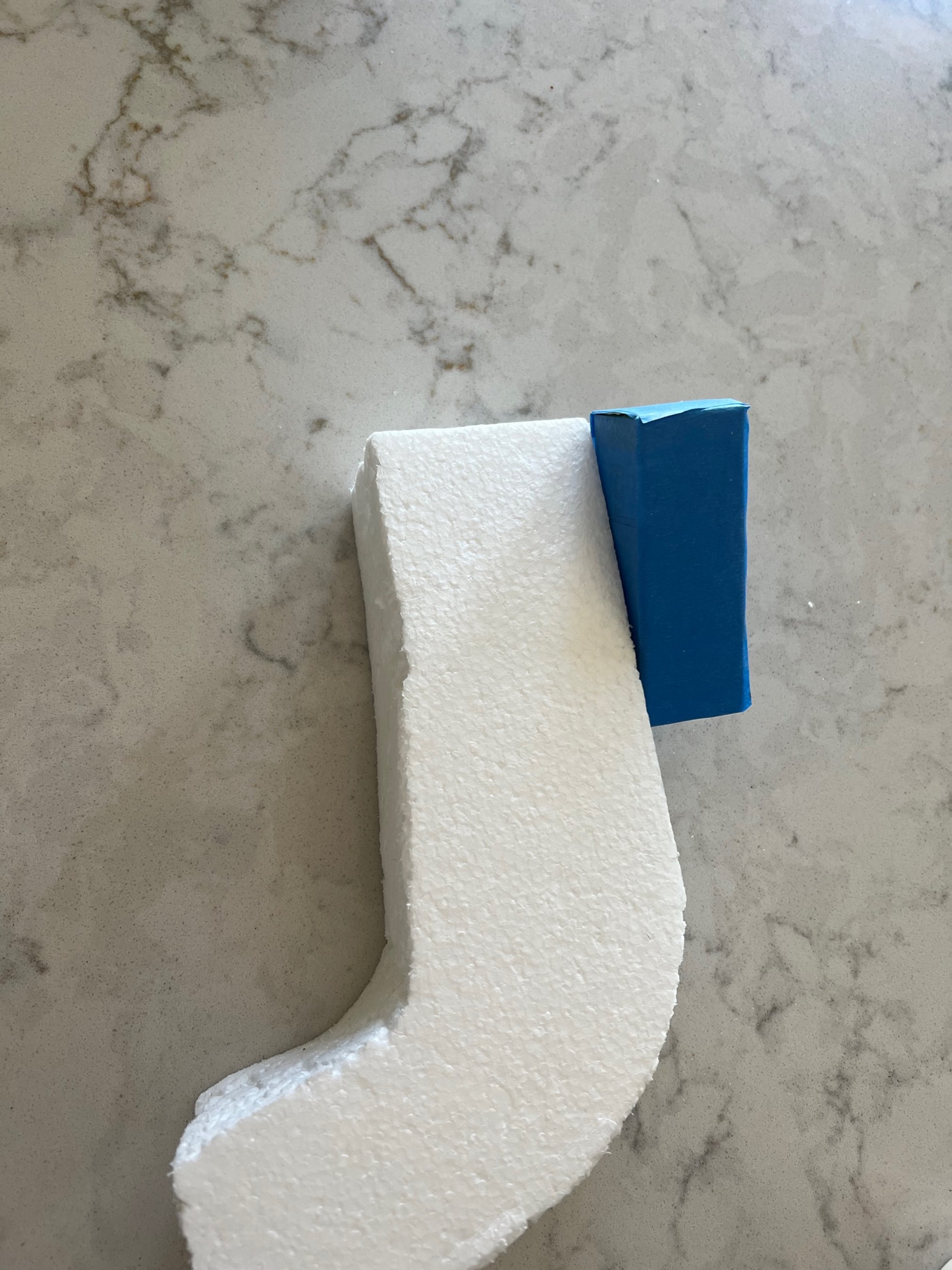
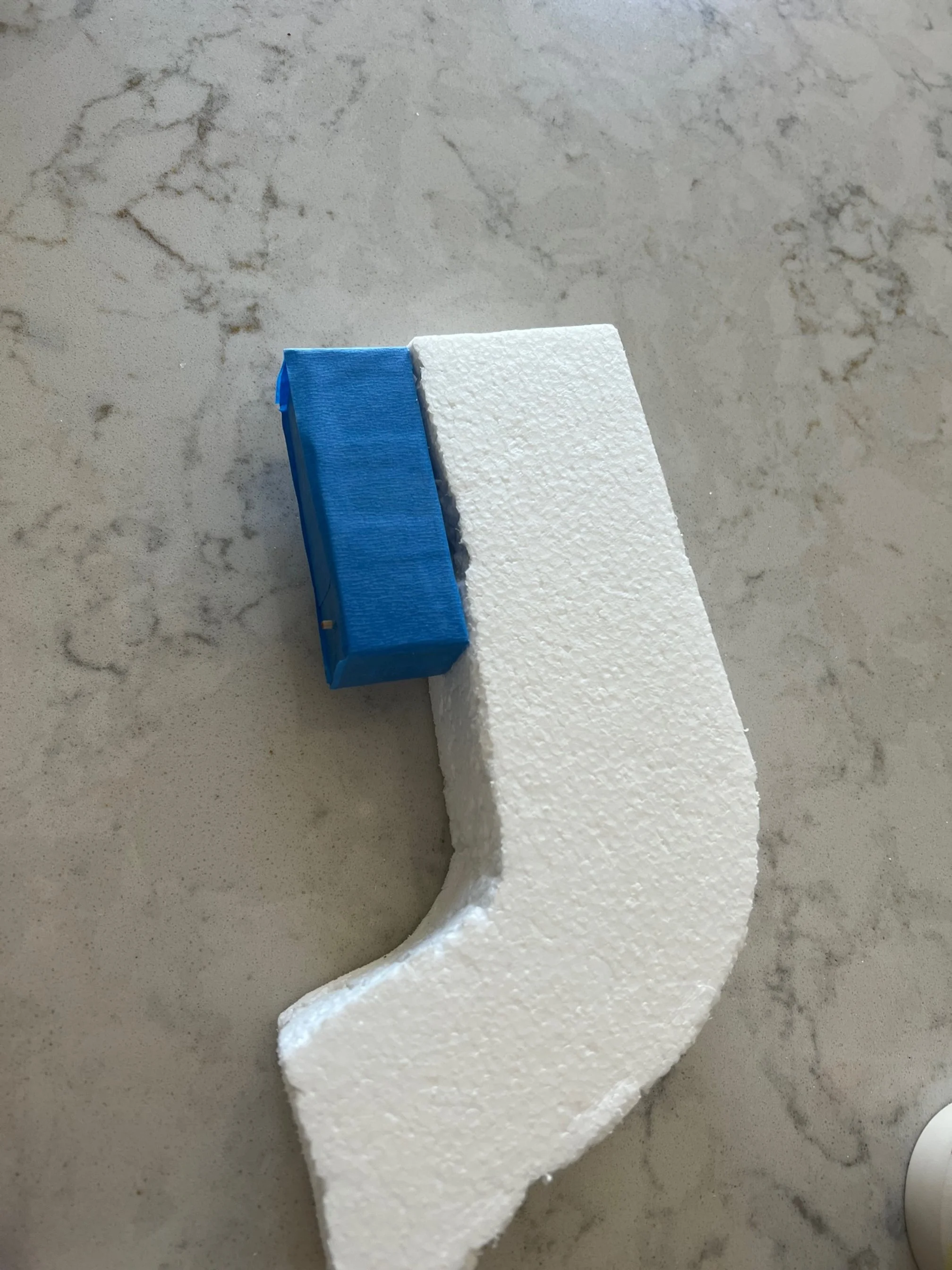
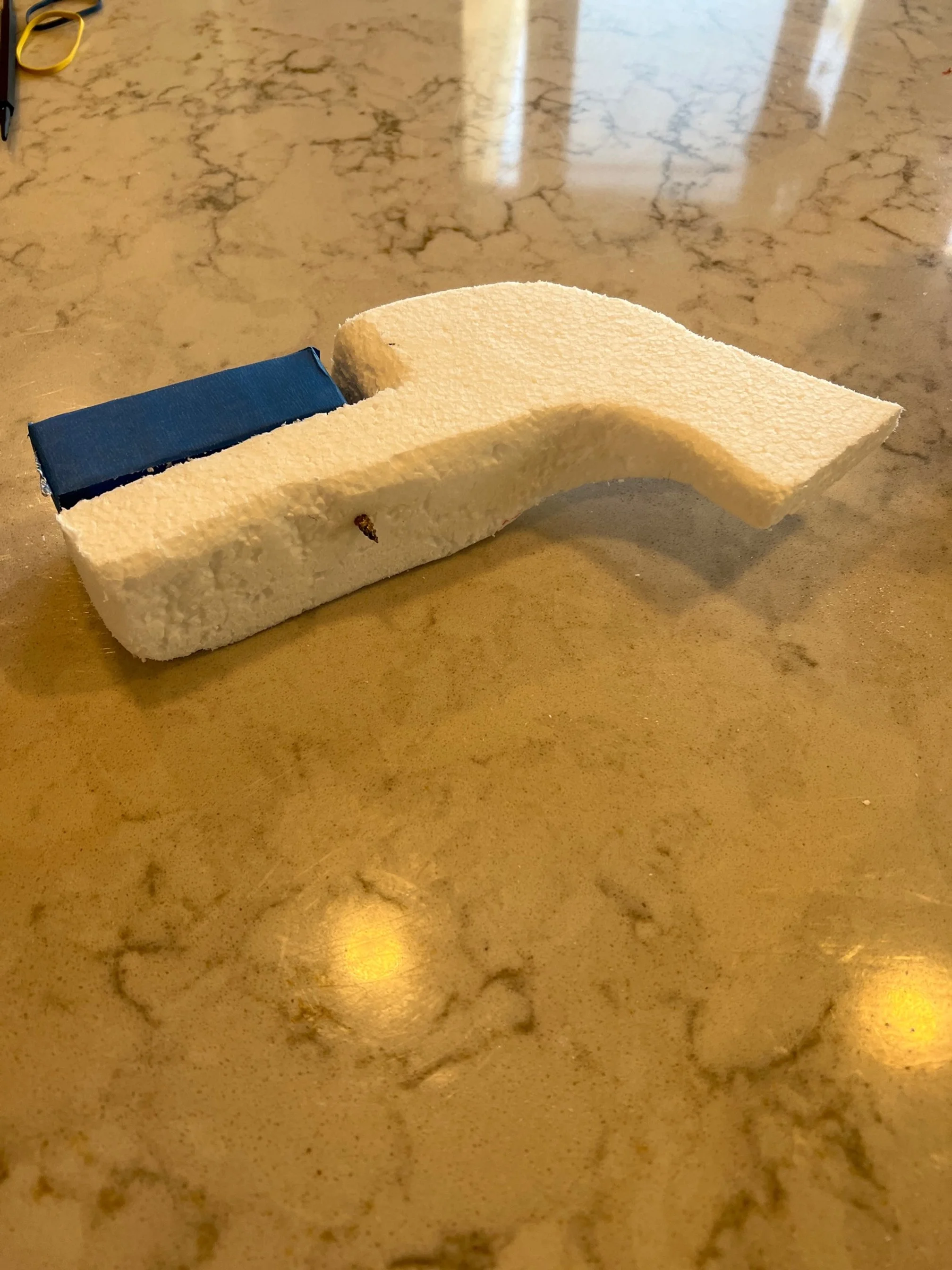
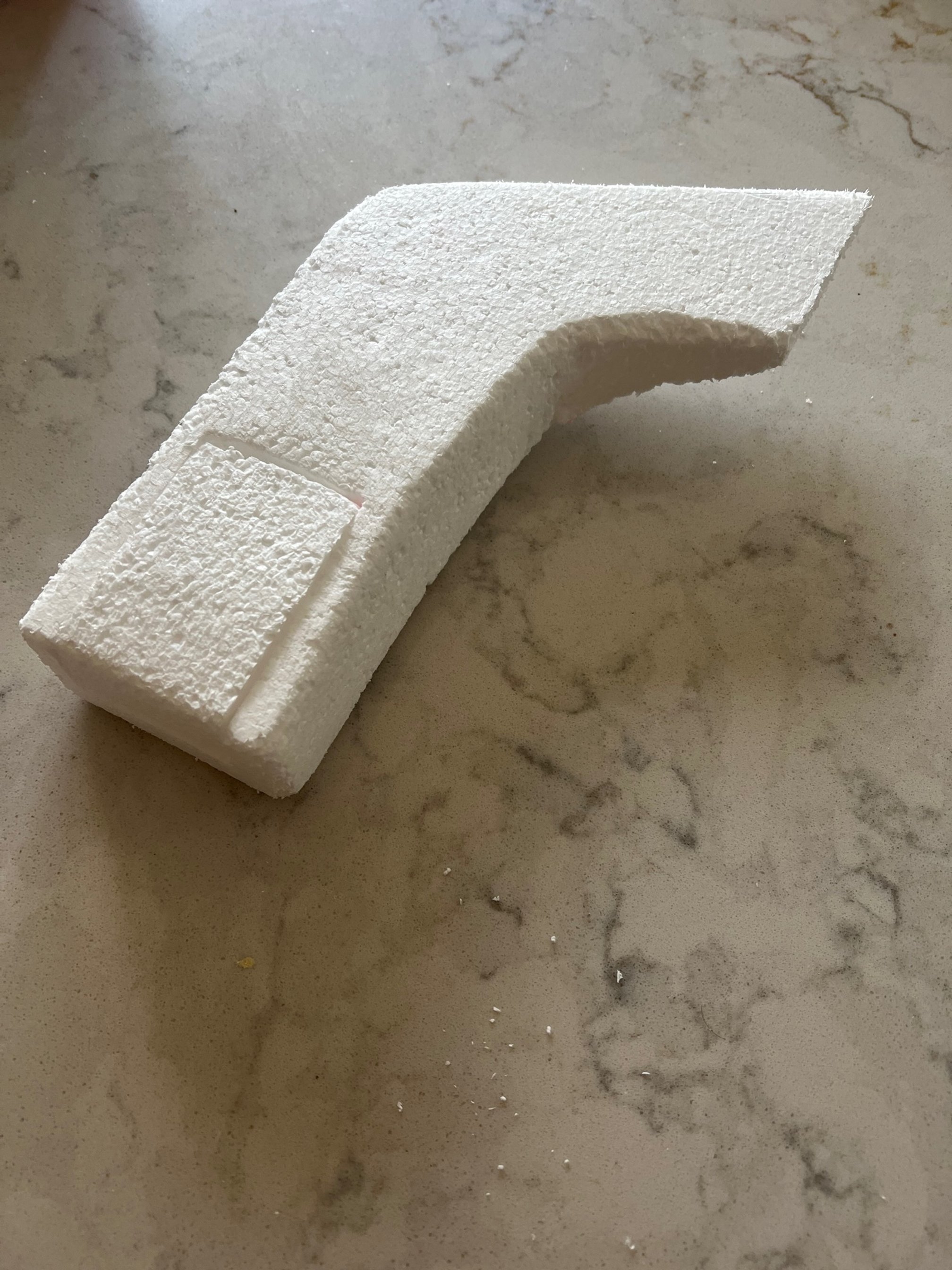
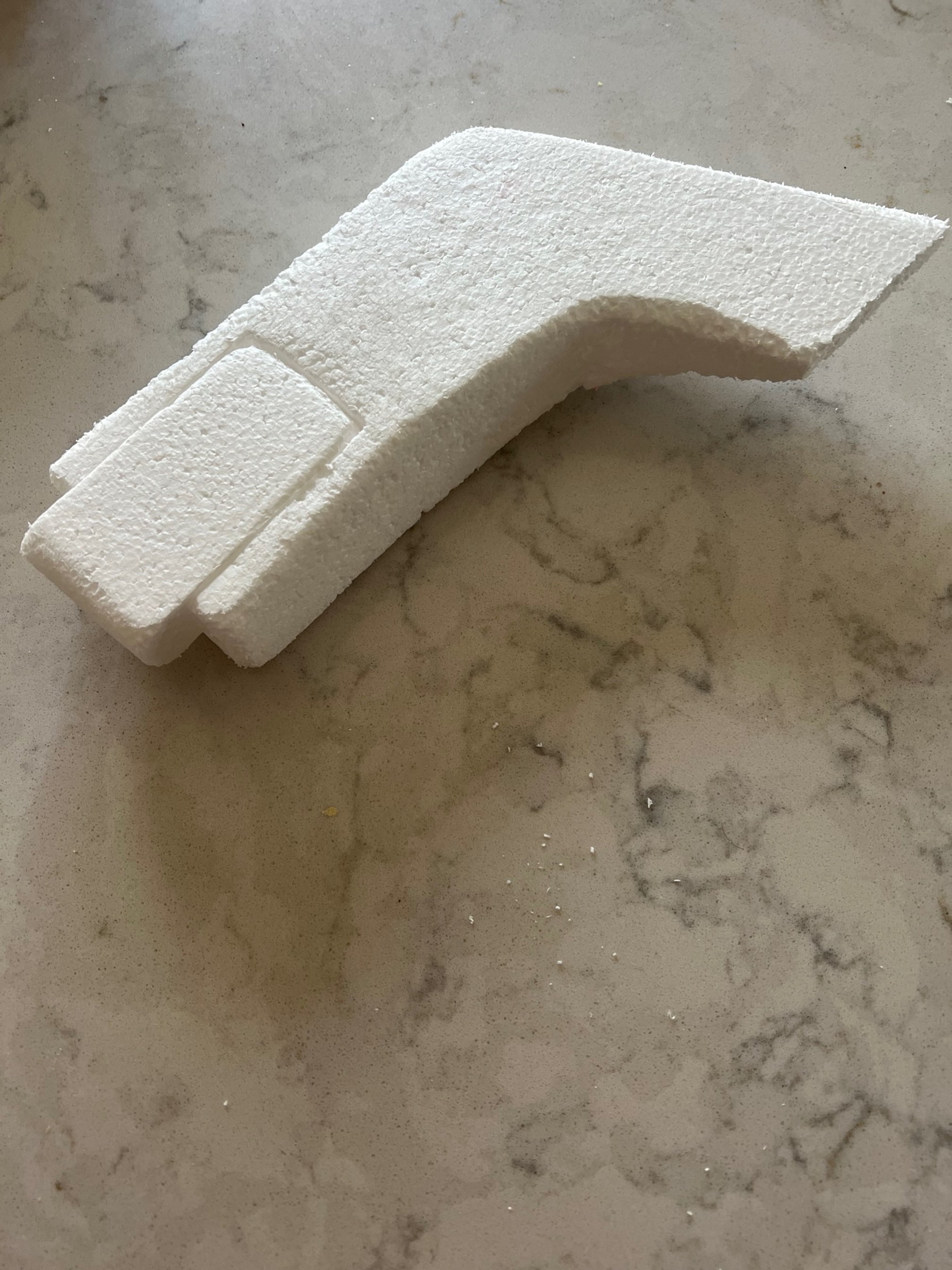
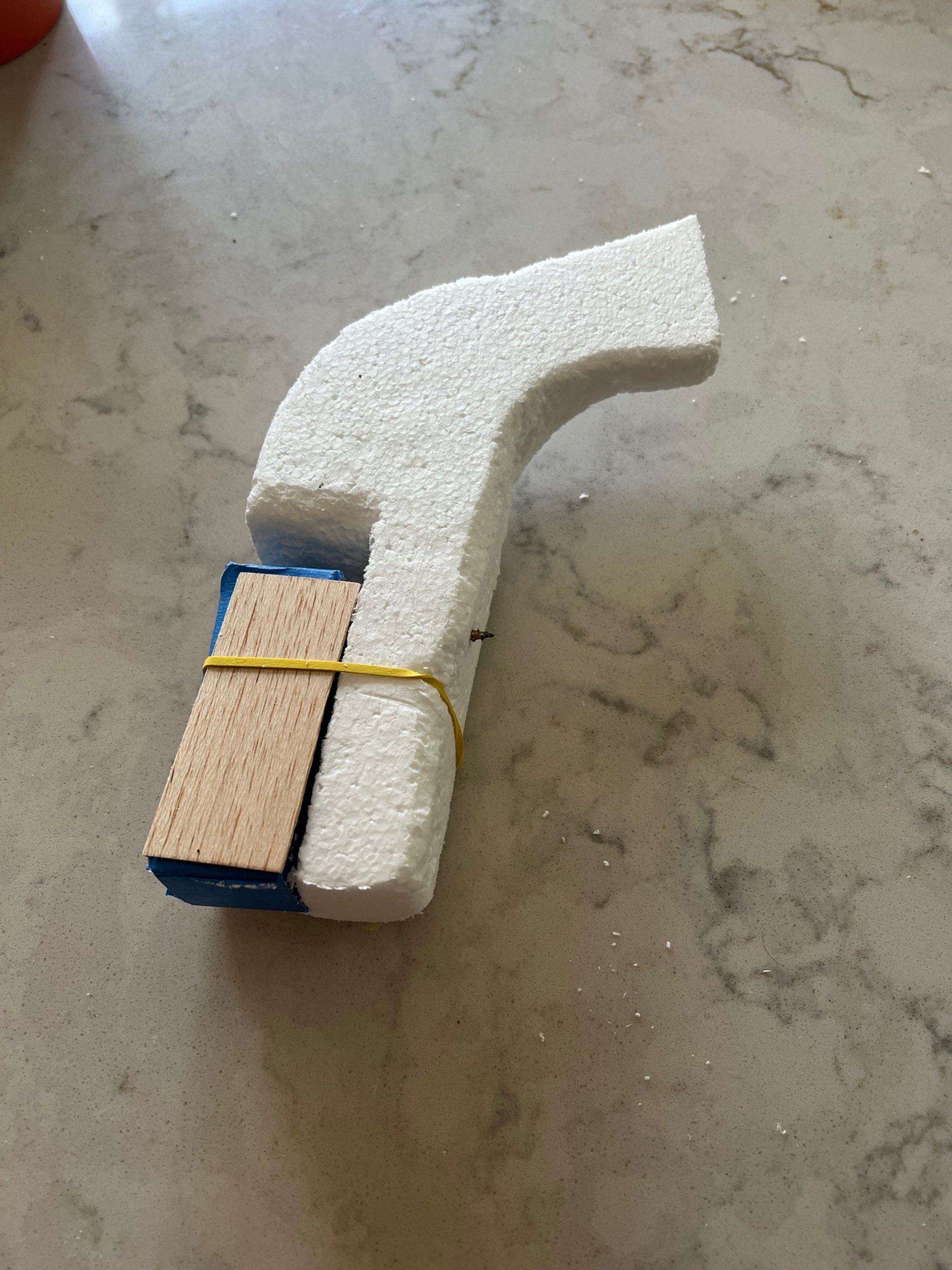
The Paddle
After playing around with my physical mockups, the results were satisfactory enough to move on with the exploration. I created some rough concept designs in SolidWorks to understand how the paddle actuator might be implemented. They were then rendered in KeyShot to provide life to the designs.
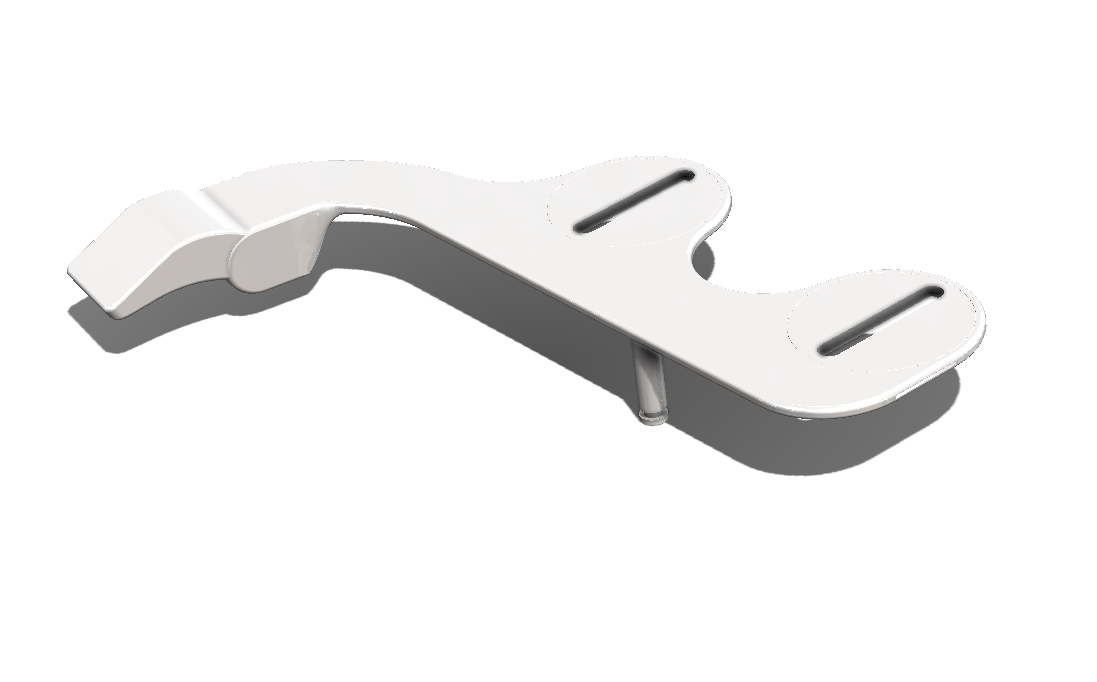
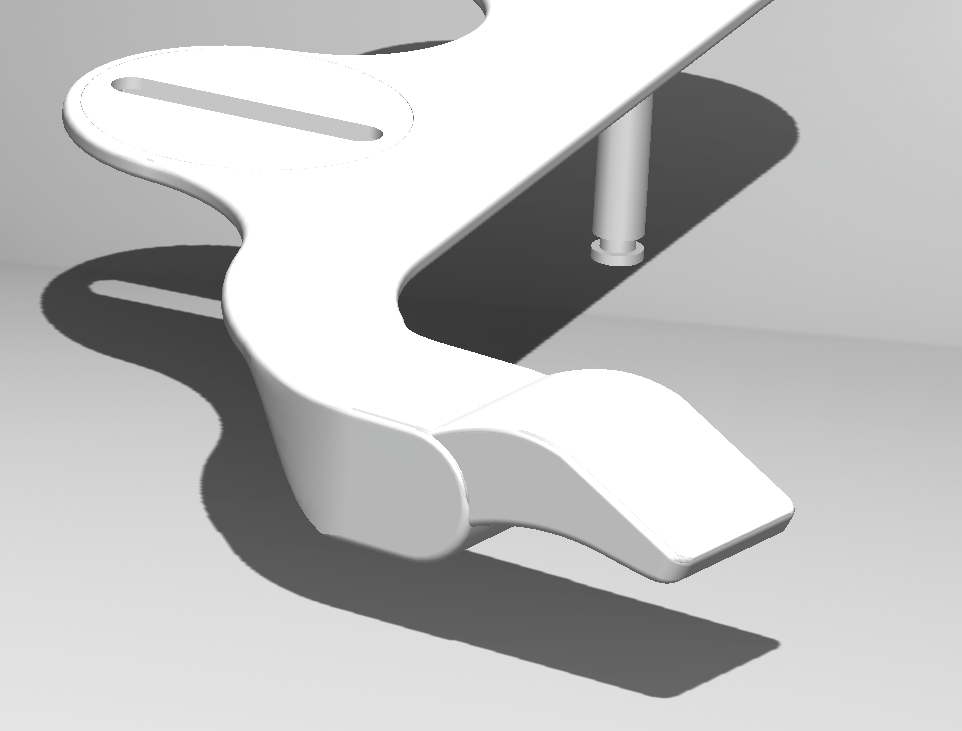
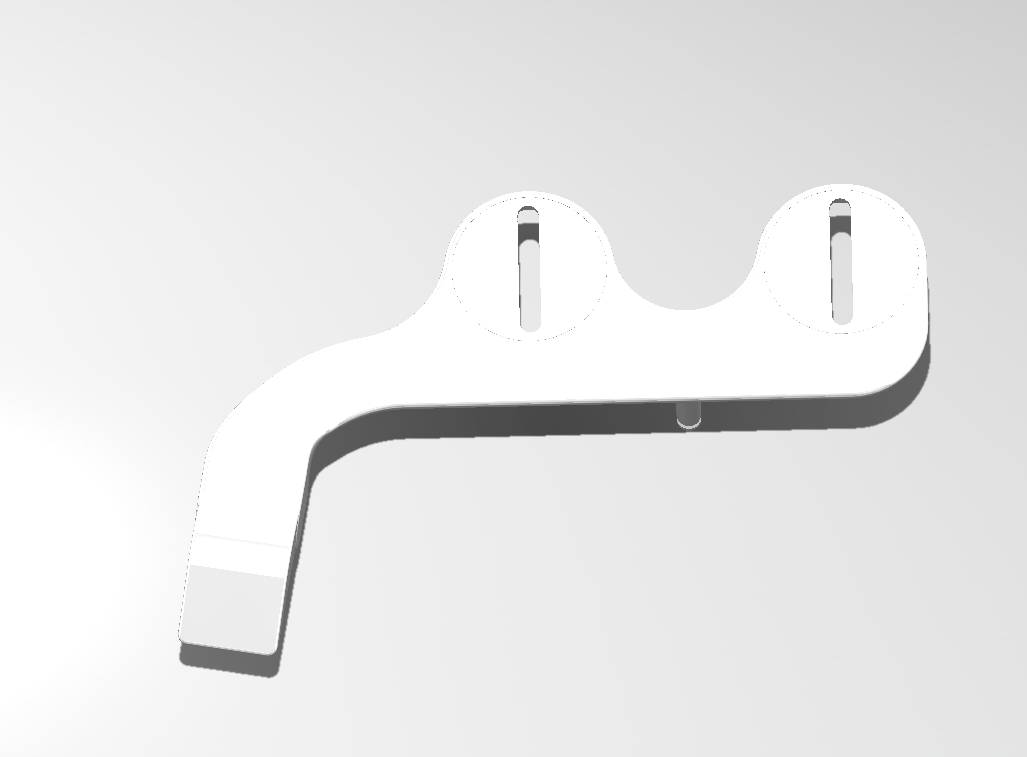

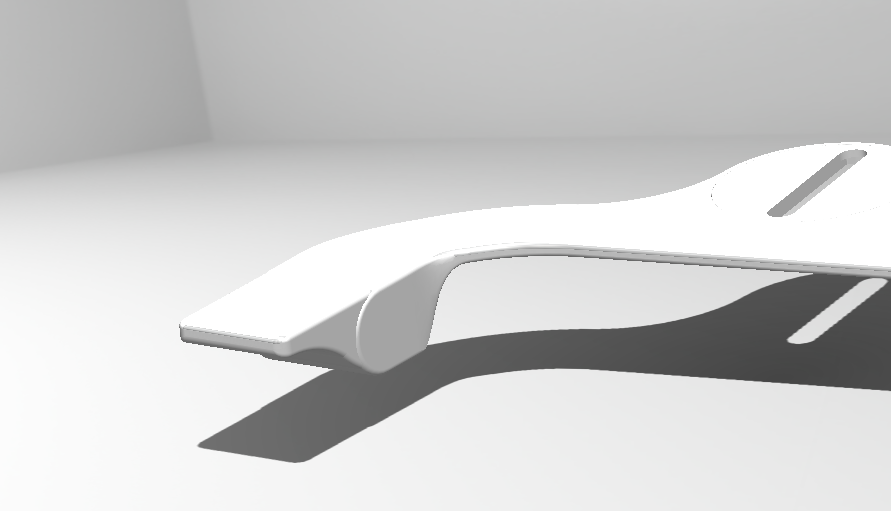
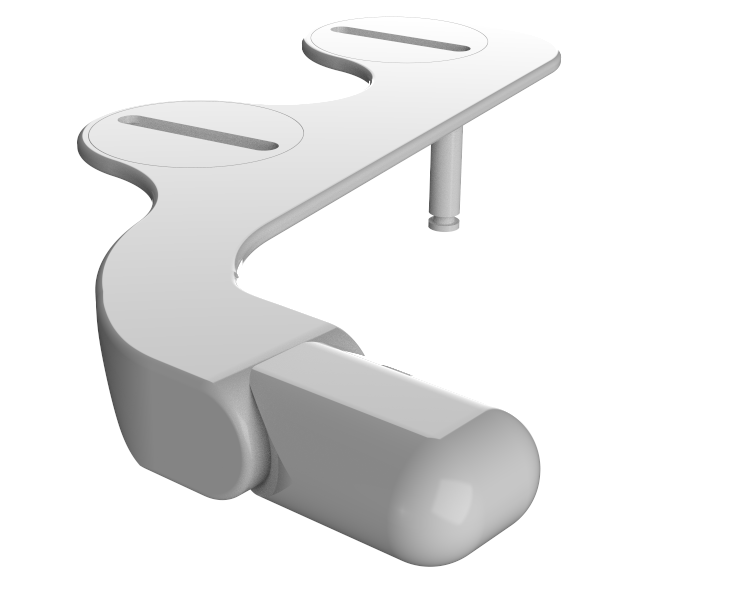

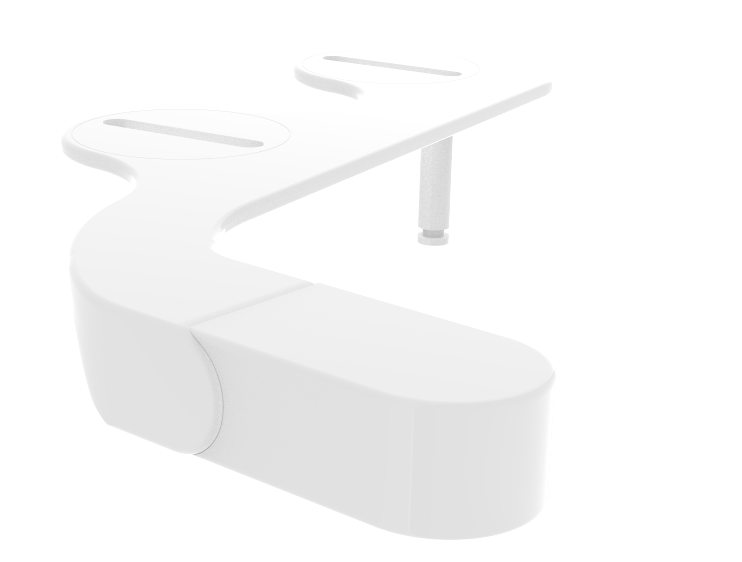
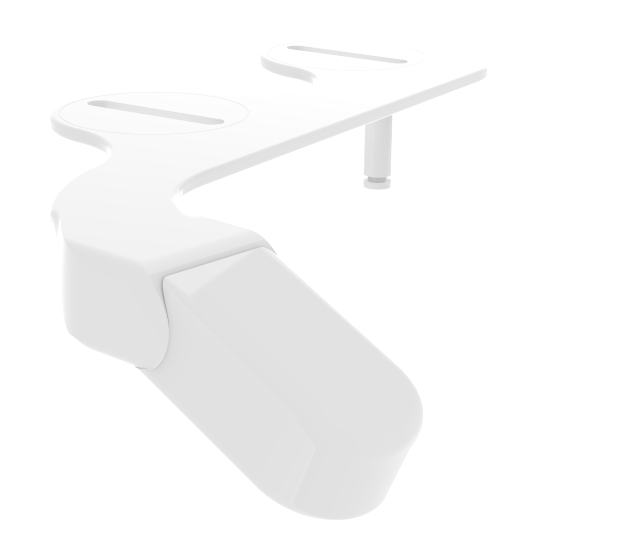
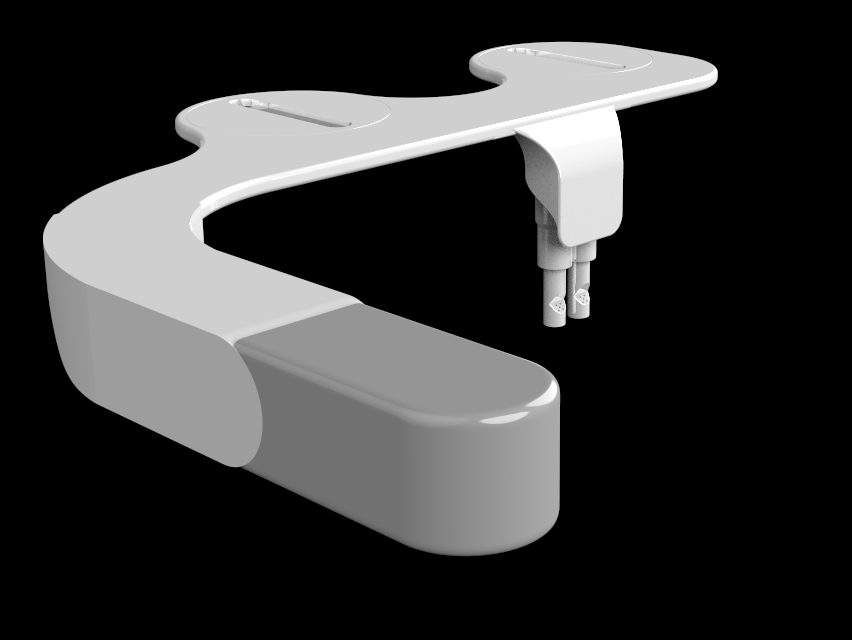

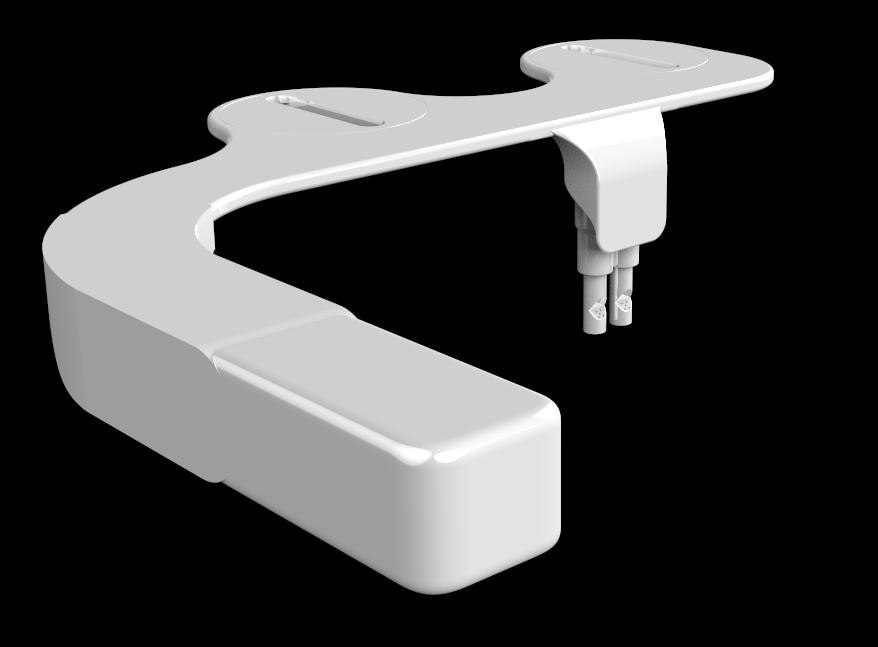
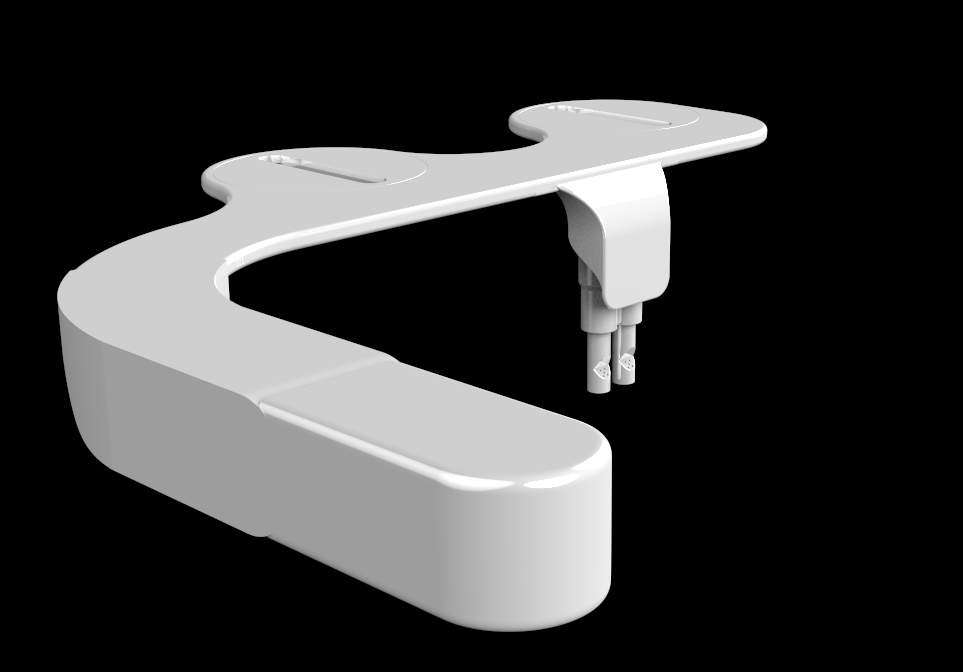
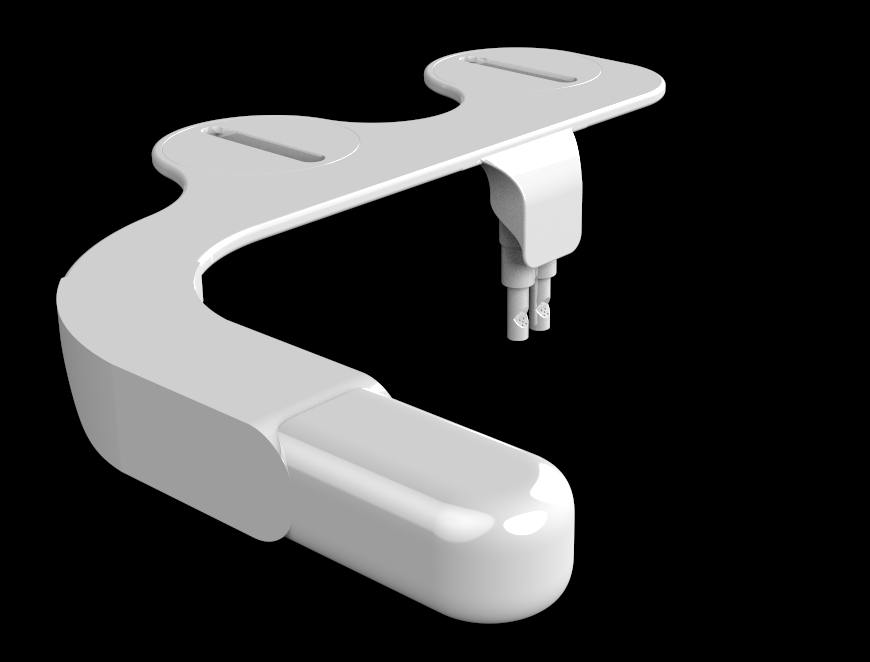
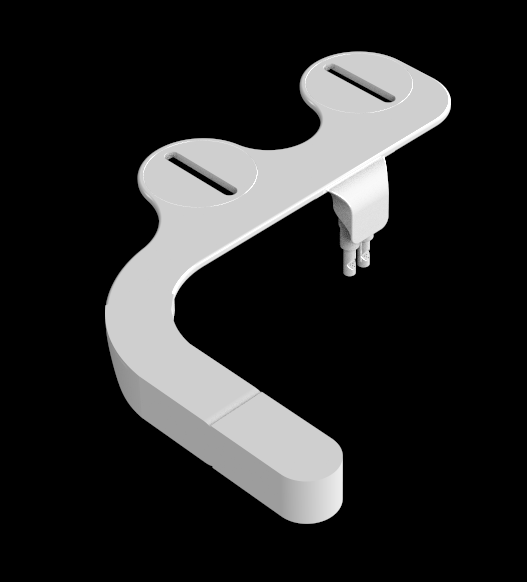
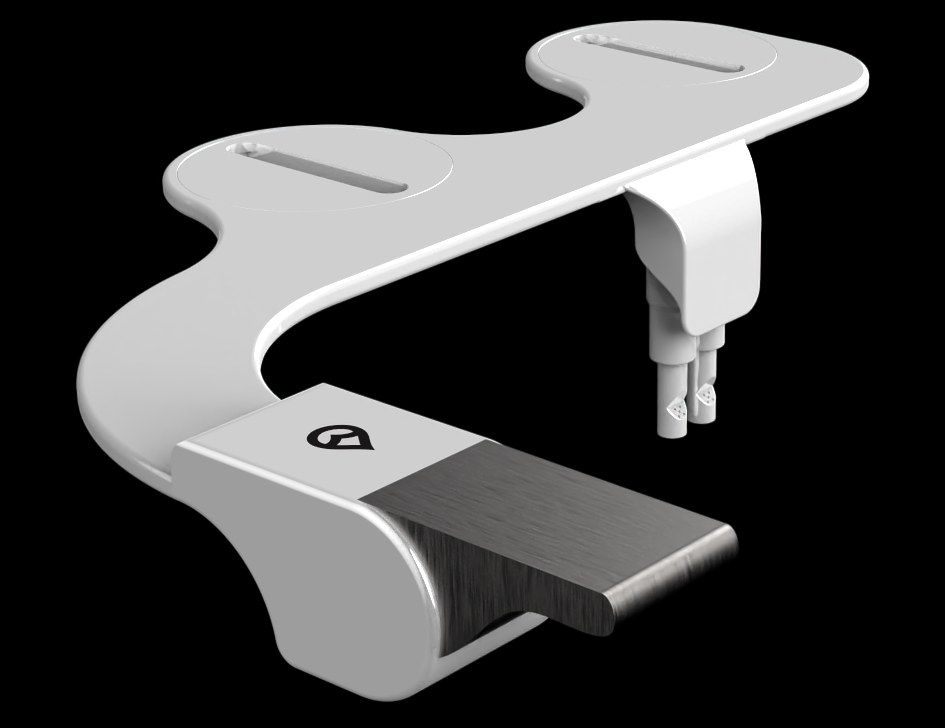
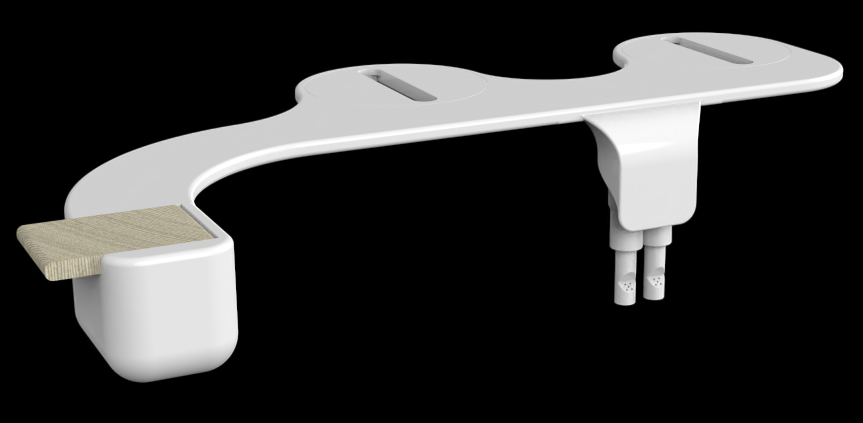

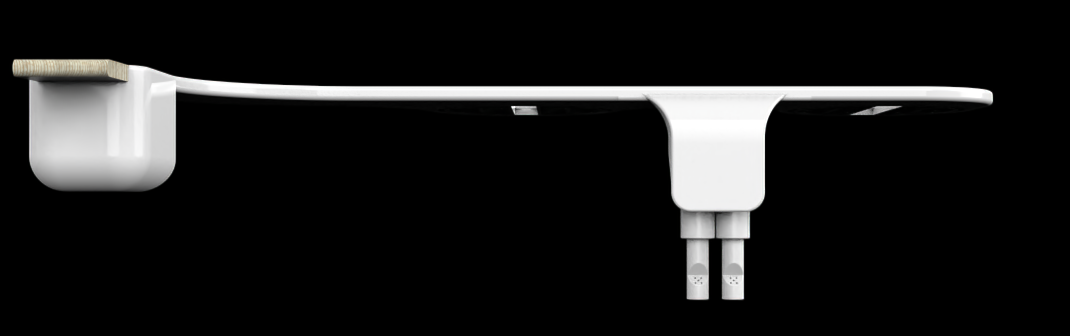
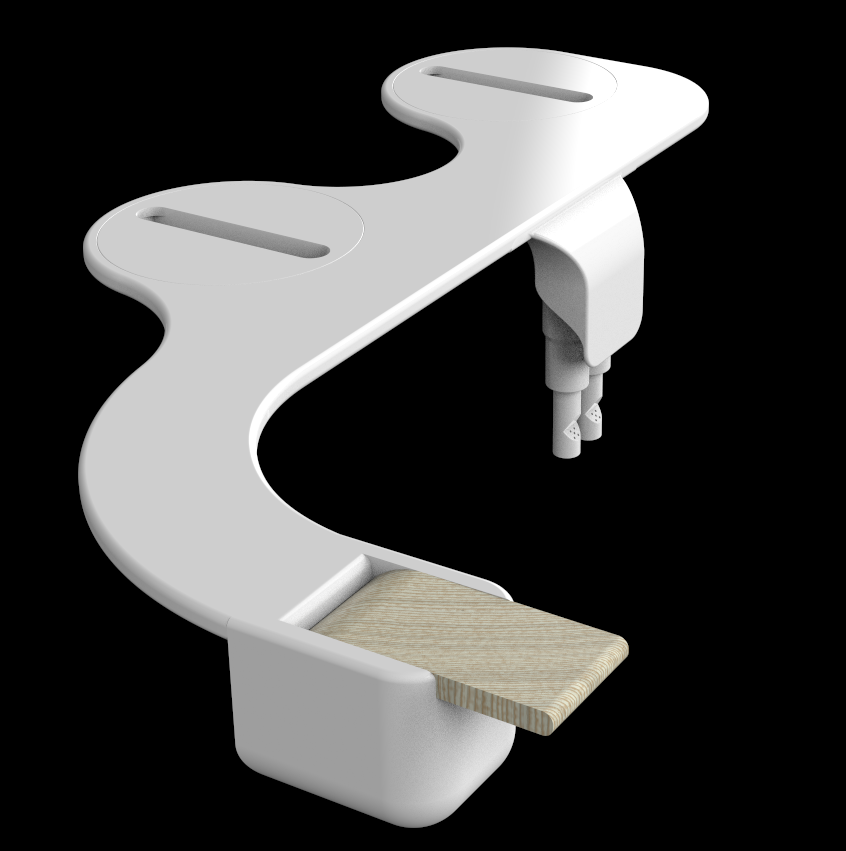
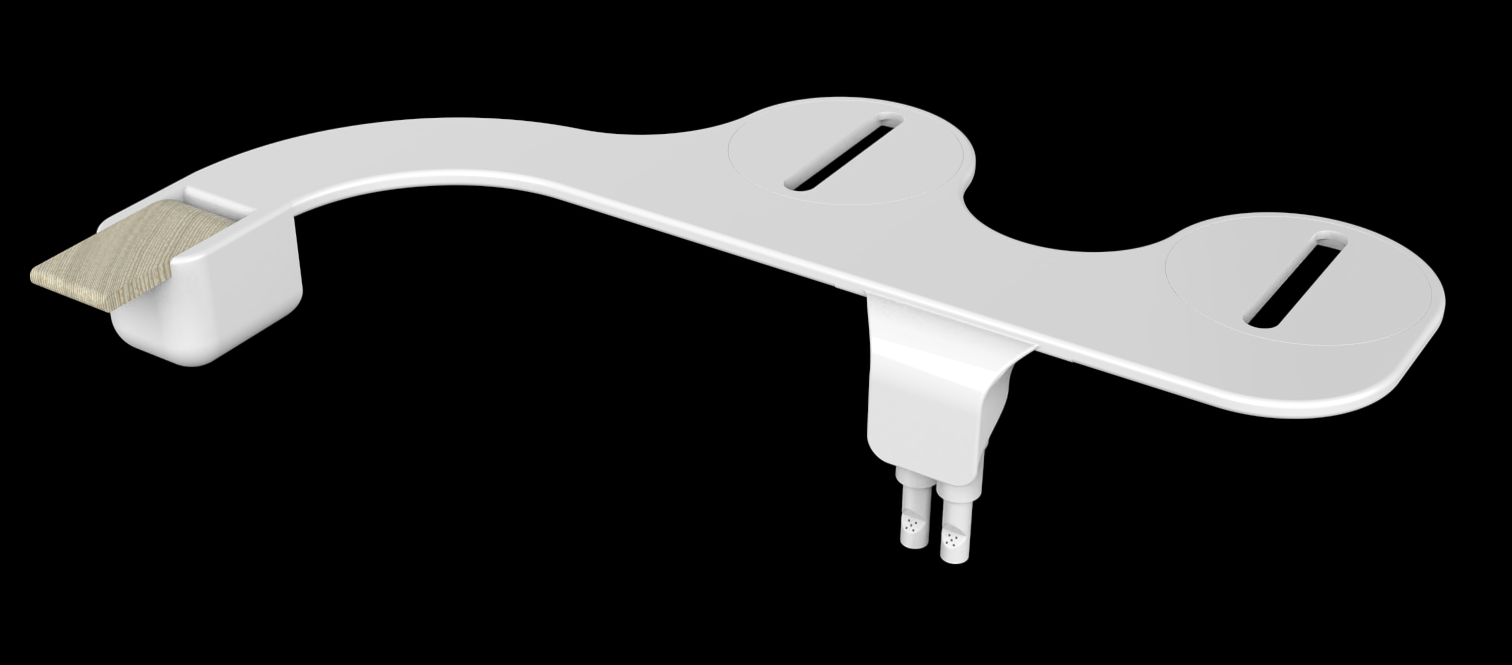


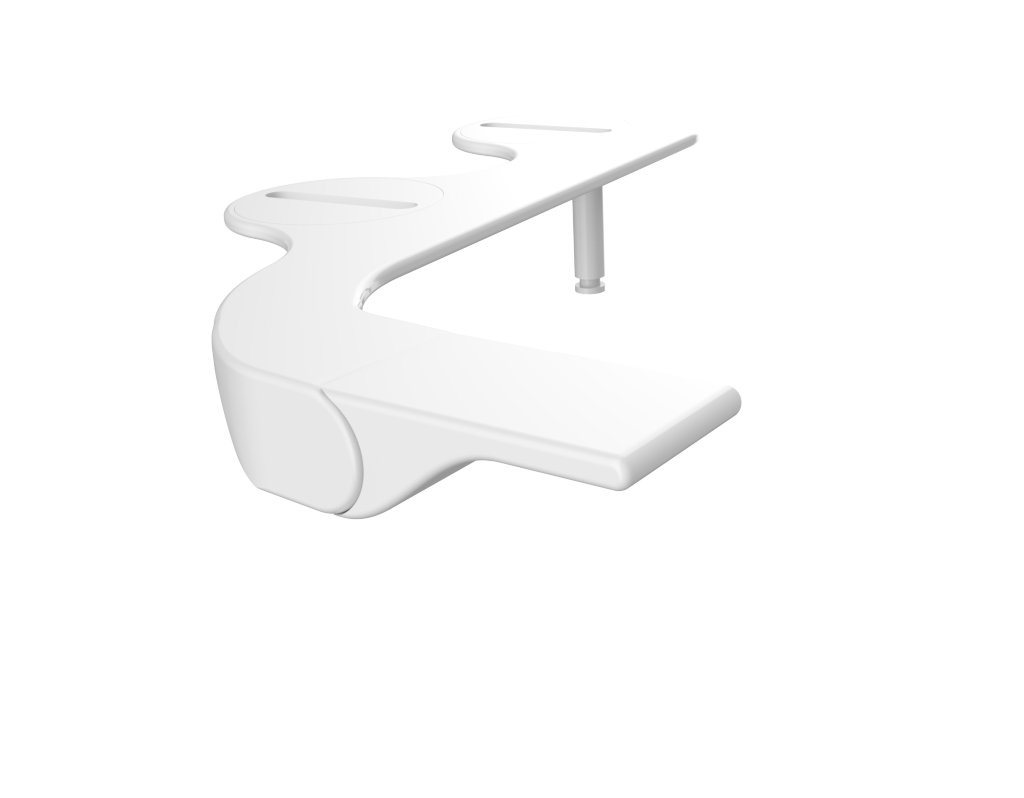
Knobs
As an alternative, some mockups were designed with a more standard knob configuration. Knobs are often used as means of actuation for bidet attachments. Their main benefit is familiarity, appeal to intuition, and the simplicity of the mechanism.
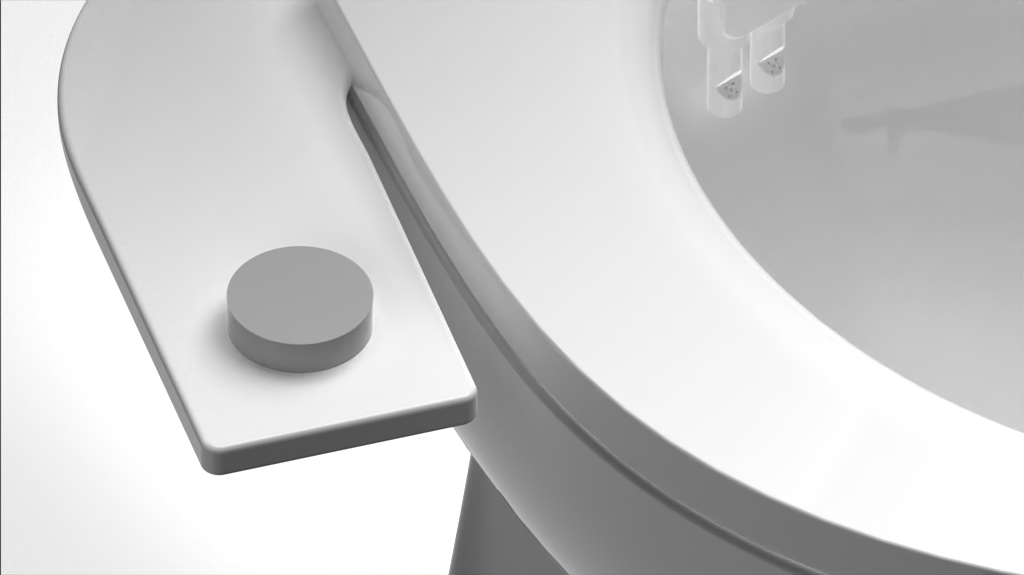
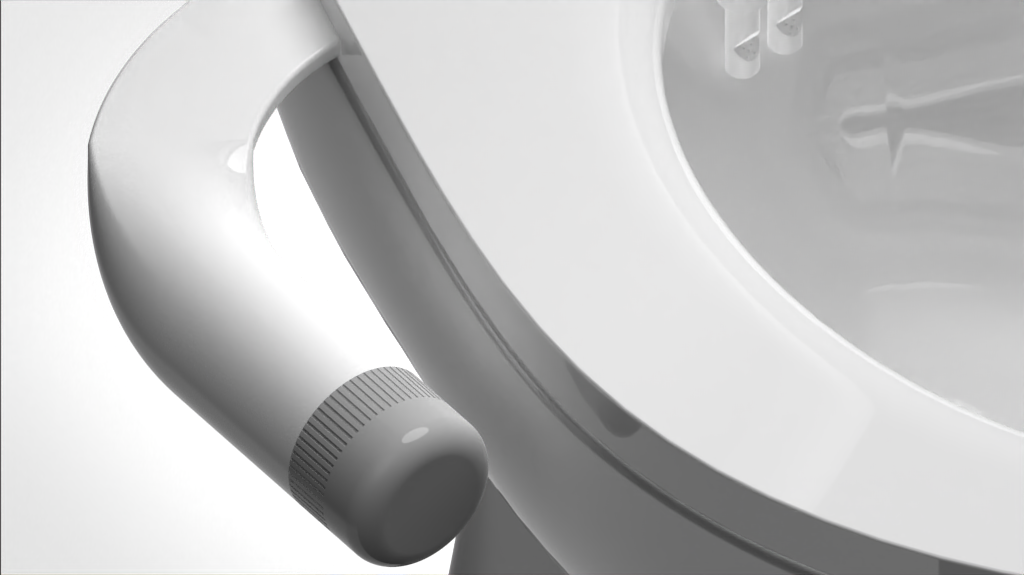

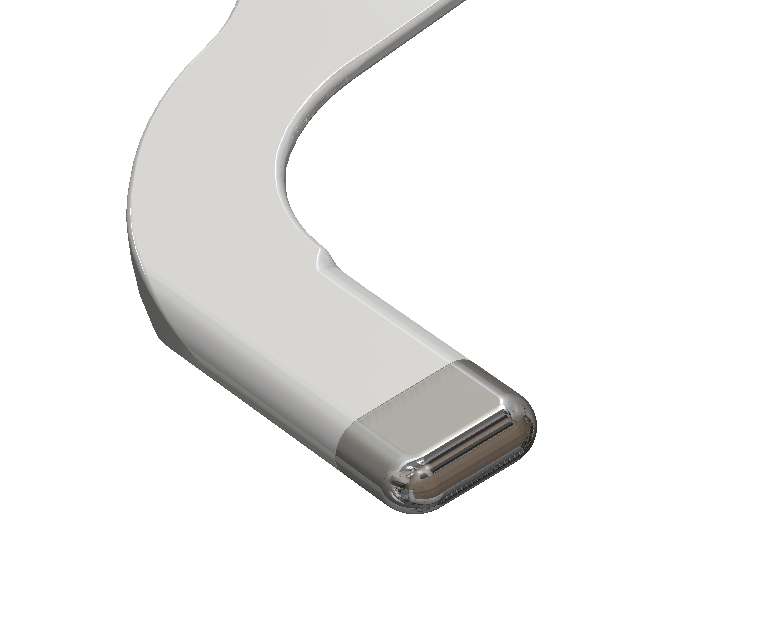
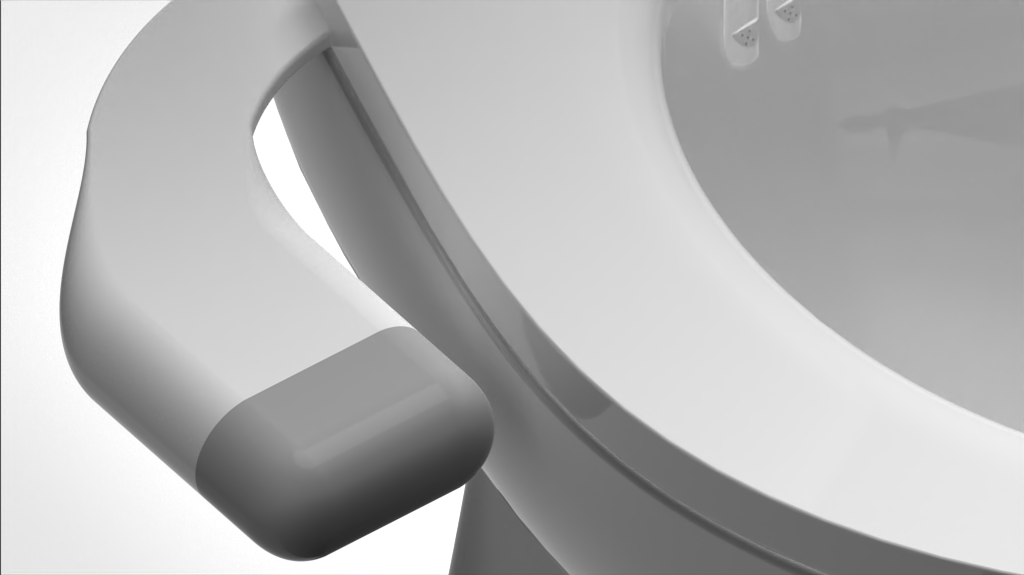
User Research and the Decision
After discussing our favorite designs between the two options with the internal team, we took consumers to aid in a final decision. We conducted multiple 200+ sample size studies to compare some our designs with competitor designs. By removing all decals, we were able to get an unbiased reaction to each design. Ultimately, the tried and true knob design was preferred.
As a product designer, you may fall in love with a concept and convince yourself that you know best. However, the end goal is to sell products which is why considering the end user holds a lot of weight.
With our selected actuator in mind, the next step was to hone in on the aesthetics of the console.
Slimming the Console
With the knob configuration, it was clear which direction to move in. To be a top player in the competitive market the design had to stand out, or actually in fact, stand in. Simplicity and elegance was the goal. There was also an incentive to make the Tushy Fresh be cohesive with the rest of the Tushy product suite. With this in mind, the design intent had taken on a “little brother” persona to the TUSHY 3.0.
In an effort to differentiate but not cannibalize the existing products, it was determined that calculated defeaturing was necessary.
The tilt switch functionality was to be removed from the feature set. This decision had a huge impact on the outcome of the project and it worked out wonderfully.
By removing the tilt switch, we were able to save space within the console such that only the valve was housed inside. Getting rid of the tilt switch assembly allowed the opportunity to play around with perspective. Thus, the “tub” was born.
The top of the console was a traditional rectangle that acted as an overhang. As the consumer is always looking down on the bidet after installation, the entire console appears slim. Because of this perspective, the length of the console could also be decreased so as to look proportional.
Ultimately, the design arrived at a slim and elegant geometry.
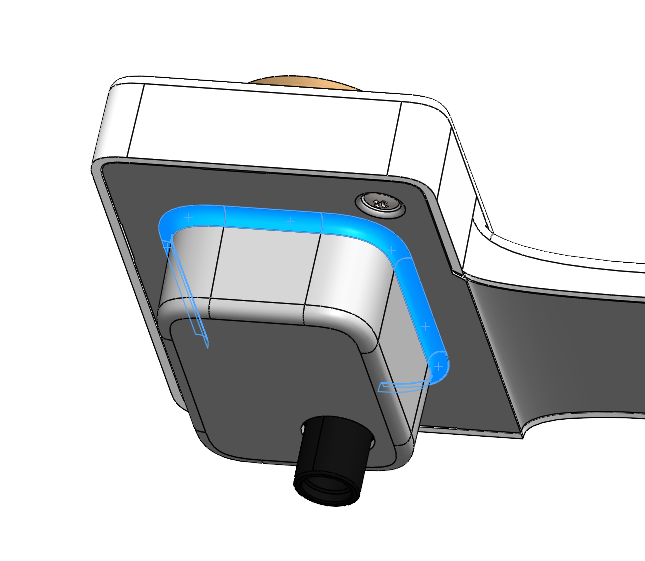



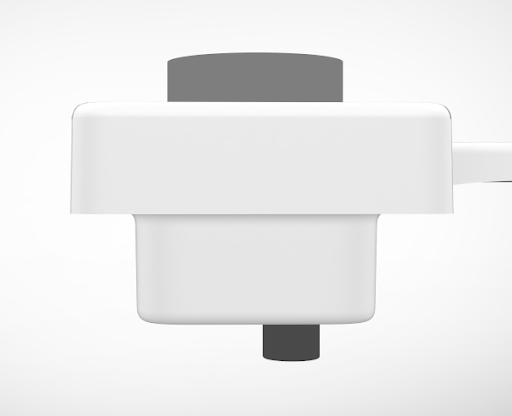
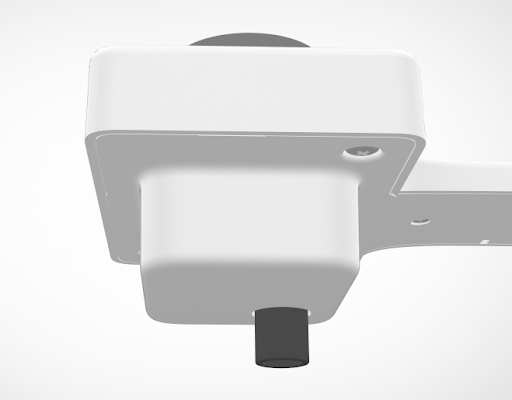
COGS Reduction
To compete at a lower price point, the COGS had to be further reduced. A reduction in material and the tilt switch subassembly was already a great start. To further drop the cost, I looked at a variety of avenues.
Flange Consolidation
Flanges are the circular mounting discs that allow the bidet to be attached to the toilet via the toilet seat bolts. With the legacy design, this was a 3-piece construction. I was able to consolidate these 3 pieces into 1 by reworking the tab assembly and increasing internal ribbing. Cost was saved on both material and assembly.
Diverter Redesign
Tushy bidet attachments have a patented nozzle rinse feature. To achieve this there are 2 tubes the enter the “diverter” which directs whether the water comes out of the nozzle or washes around the nozzle. With the tilt switch feature, the inlets for the diverter had to be coaxial such that the nozzle can angle back and forth. By removing the tilt switch, I was able to redesign the diverter so the two inlets were parallel to one another, saving costs by reducing tube length.
Removal of Stiffener
Up to this point, stainless steel stiffeners were used spanning from the body to the console of the bidet. By reducing the console length, the cantilever effect was mitigated. After comparatively performing deflection tests with a force gauge, it was deemed that a stiffener was no longer necessary with the Tushy Fresh construction.
Knob Material
Knob material on past bidets was metal or bamboo with a fitted plastic insert such that they could be attached to the valve shaft. As a lower alternative price point, I elected for an all plastic construction which consolidated the knob from 2 pieces to 1. This also saved on manufacturing cost. A variety of finishing processes were explored to best match the look and feel of a metal knob so as to not compromise the robust and premium feel of the product. A wire EDM finishing process was selected to achieve this. A bamboo knob is available at a raised price point.
3D Printed Prototypes
After locking in the design of the form, the DFM stage was enacted. After holding design reviews to ensure everything was manufacturable, it was time to validate the dimensions. To do so, a 3D printed prototype was made via ProtoLabs.
After inserting all of the components, everything fit well with the exception of the valve. What wasn’t considered in the initial design was the torque that the tubes would impart on the valve, causing it to sit askew and make the housing difficult to enclose. To address this, the tub was slightly expanded, the outlets on the valve were slightly turned in tool-safe manner, and ribs were adjusted to better guide the internal tubes. I tested the new fit by printing an adjusted section of the console bottom.
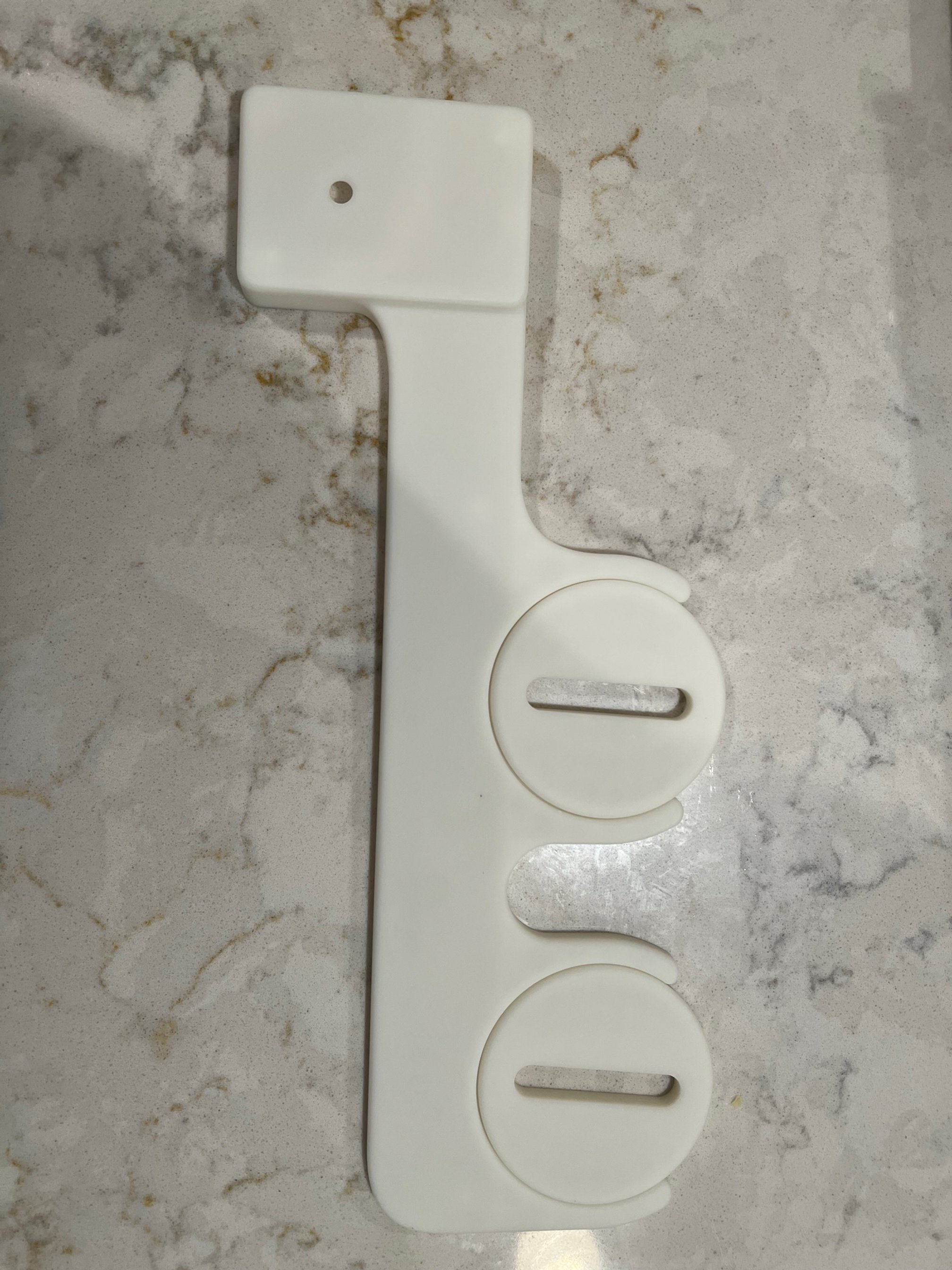
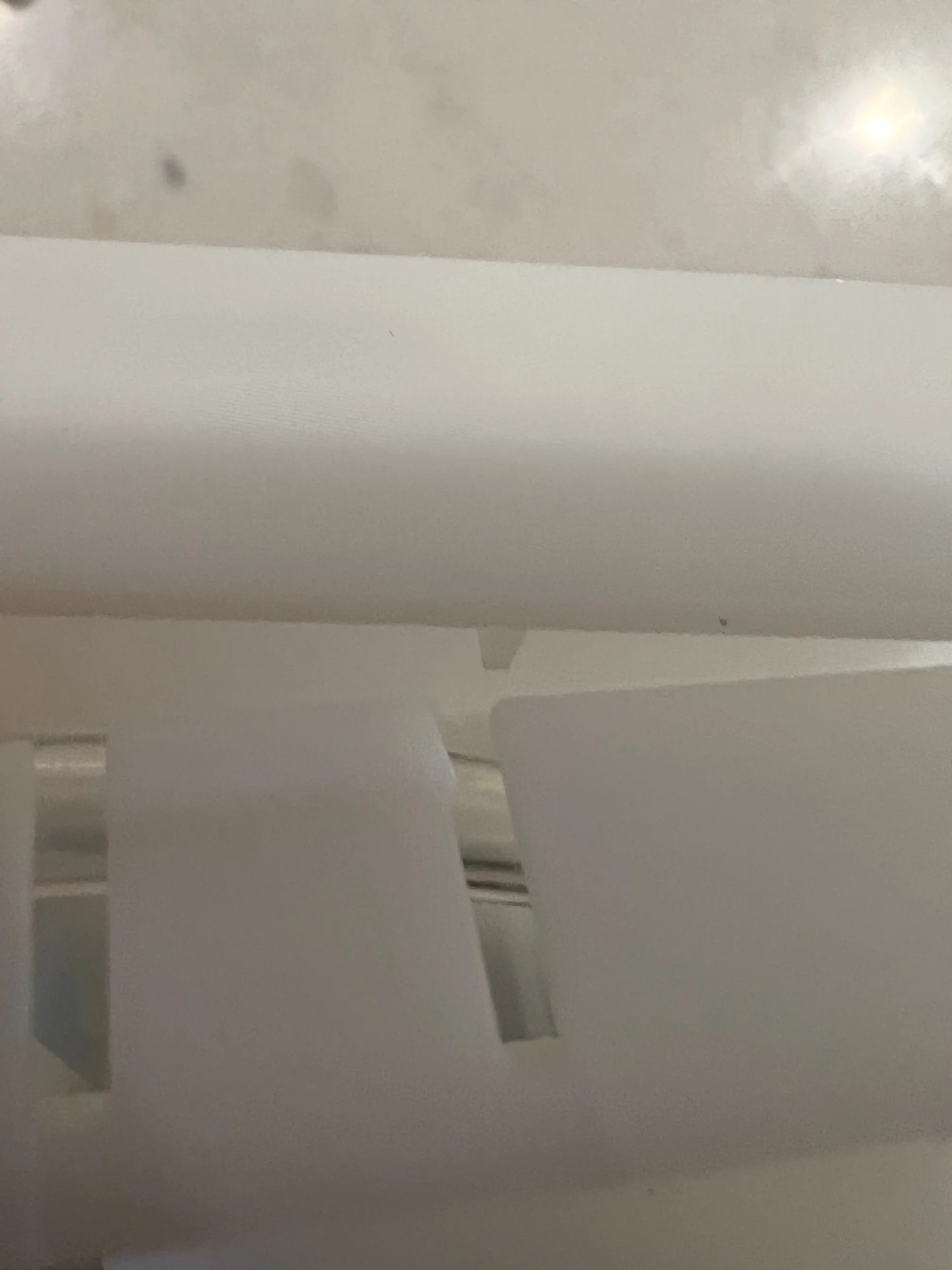
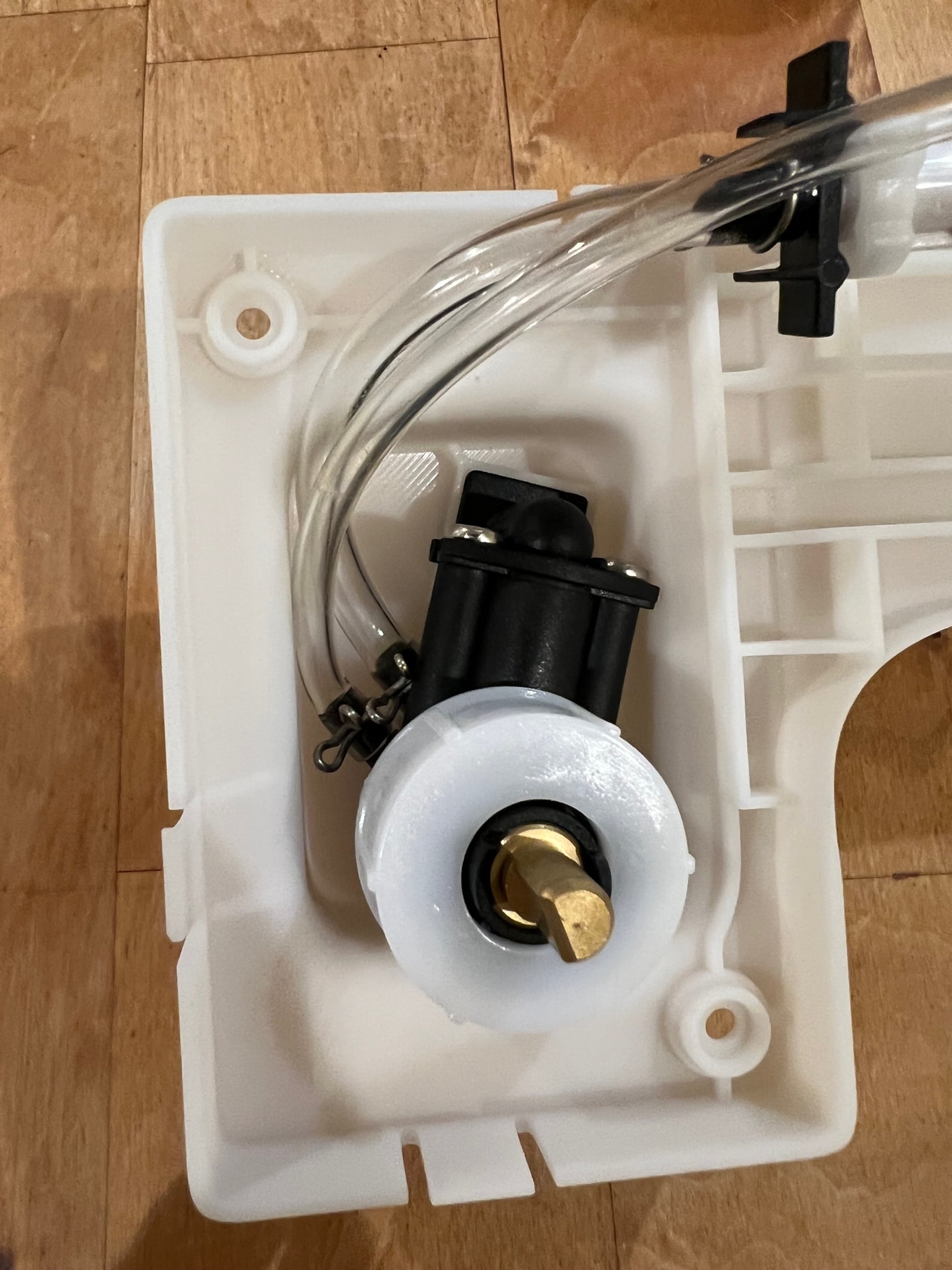
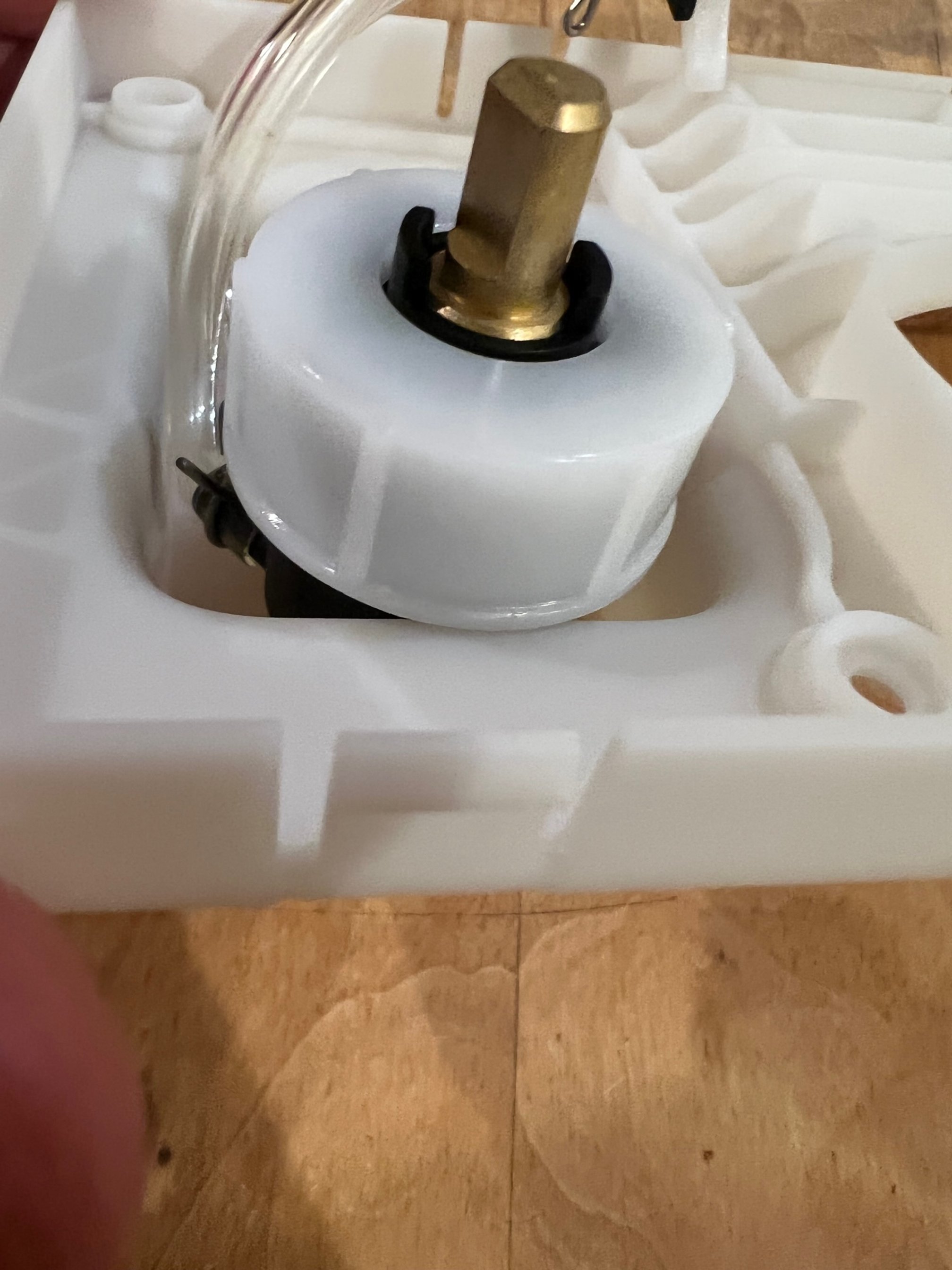


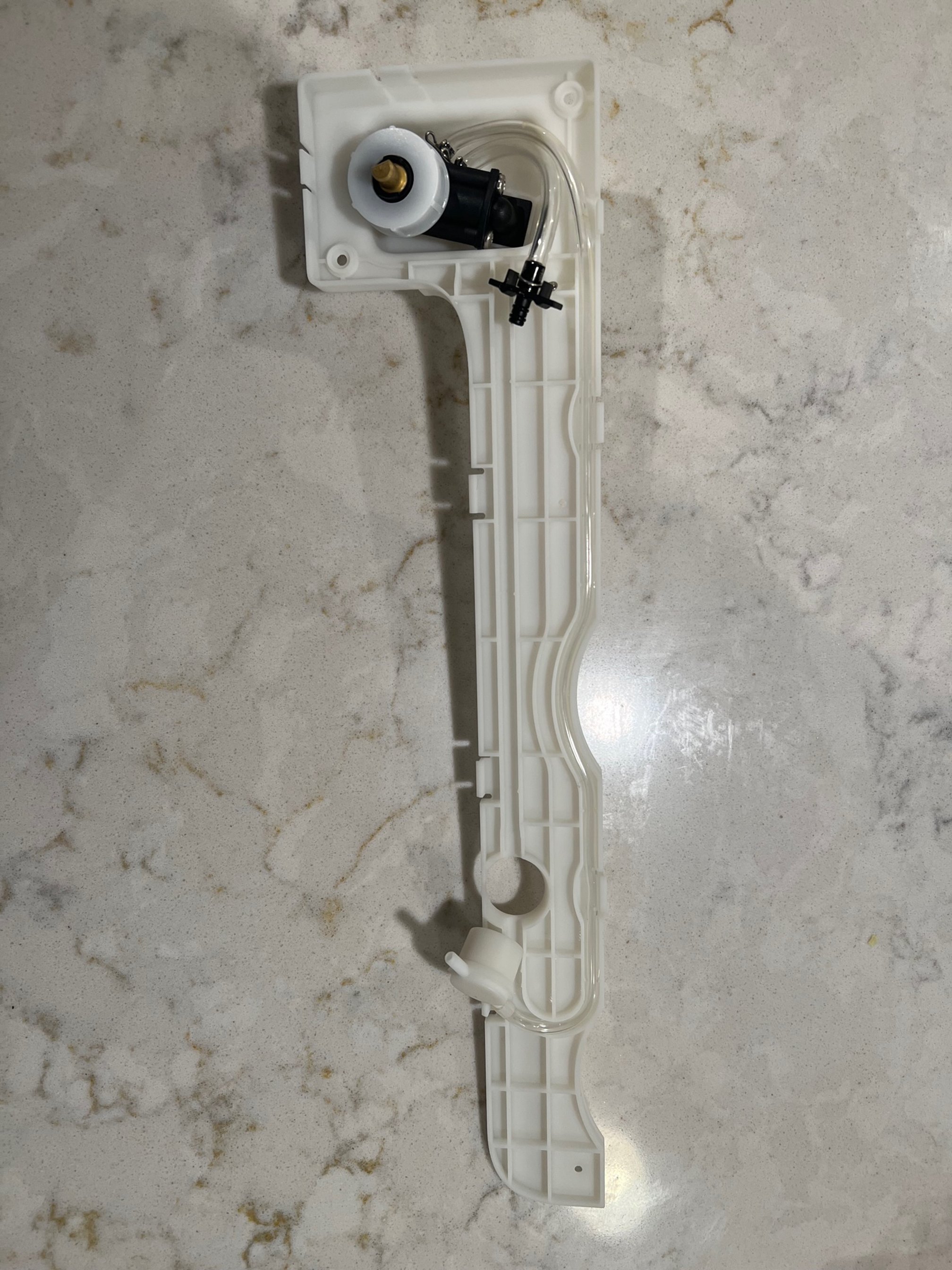
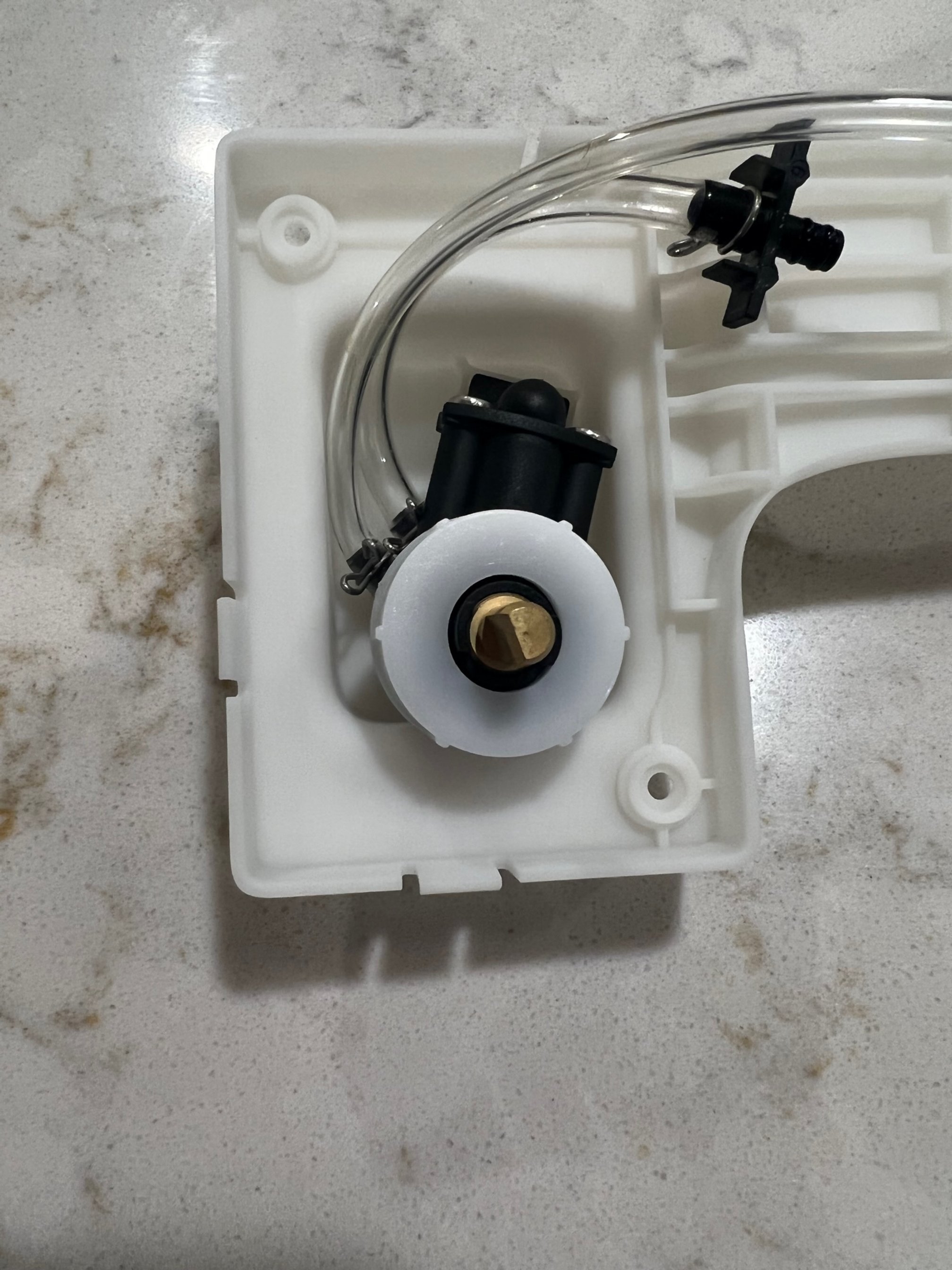
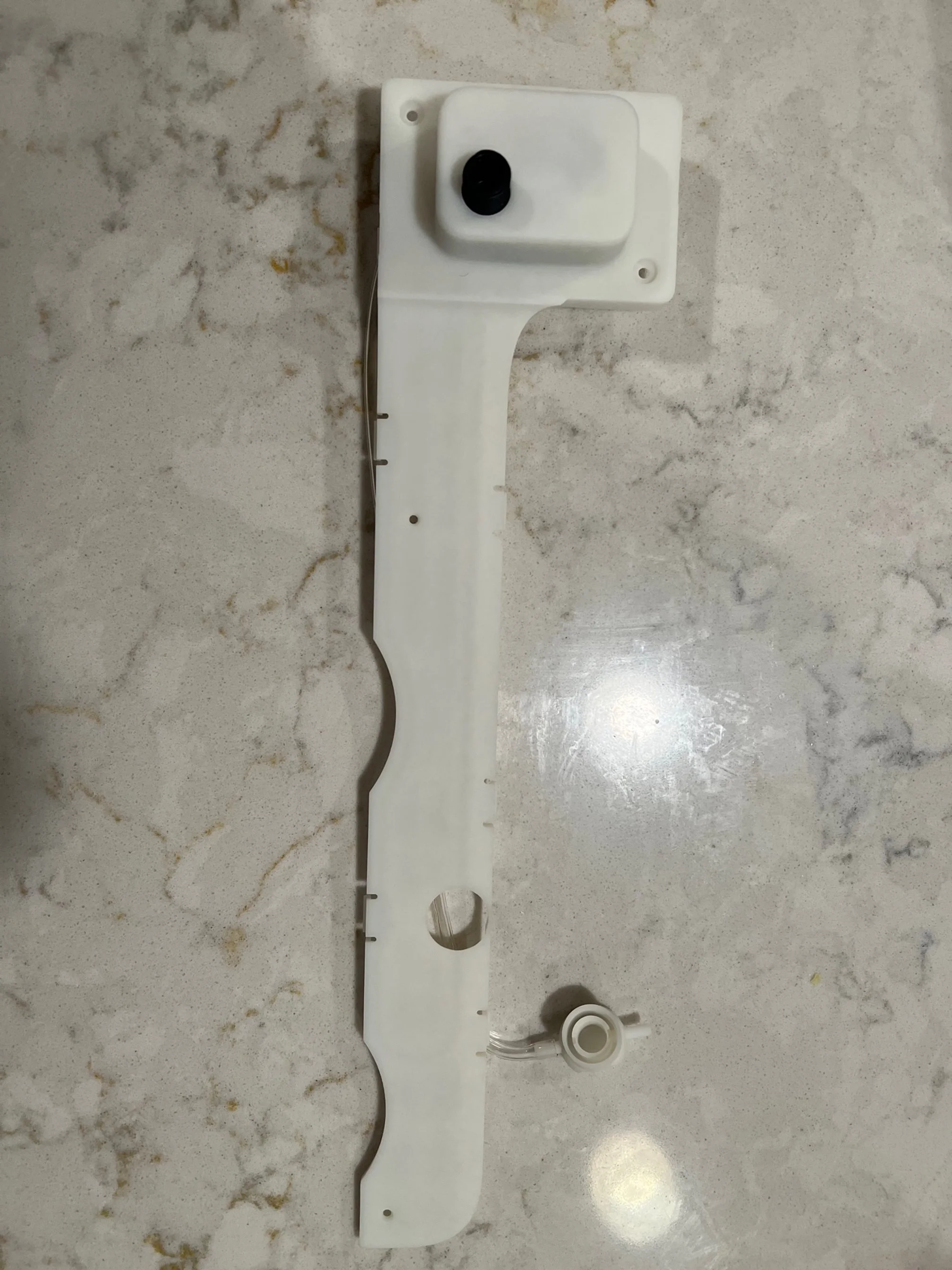
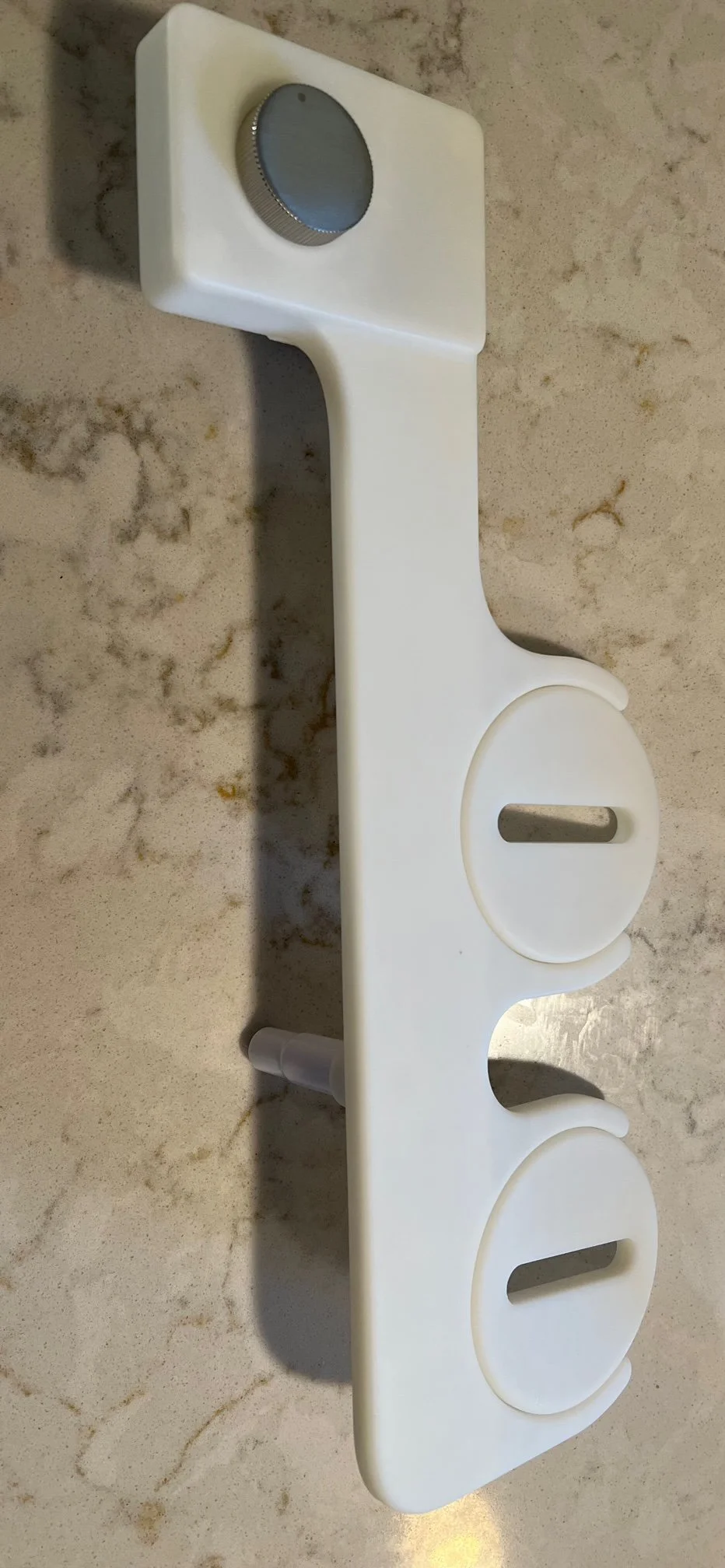
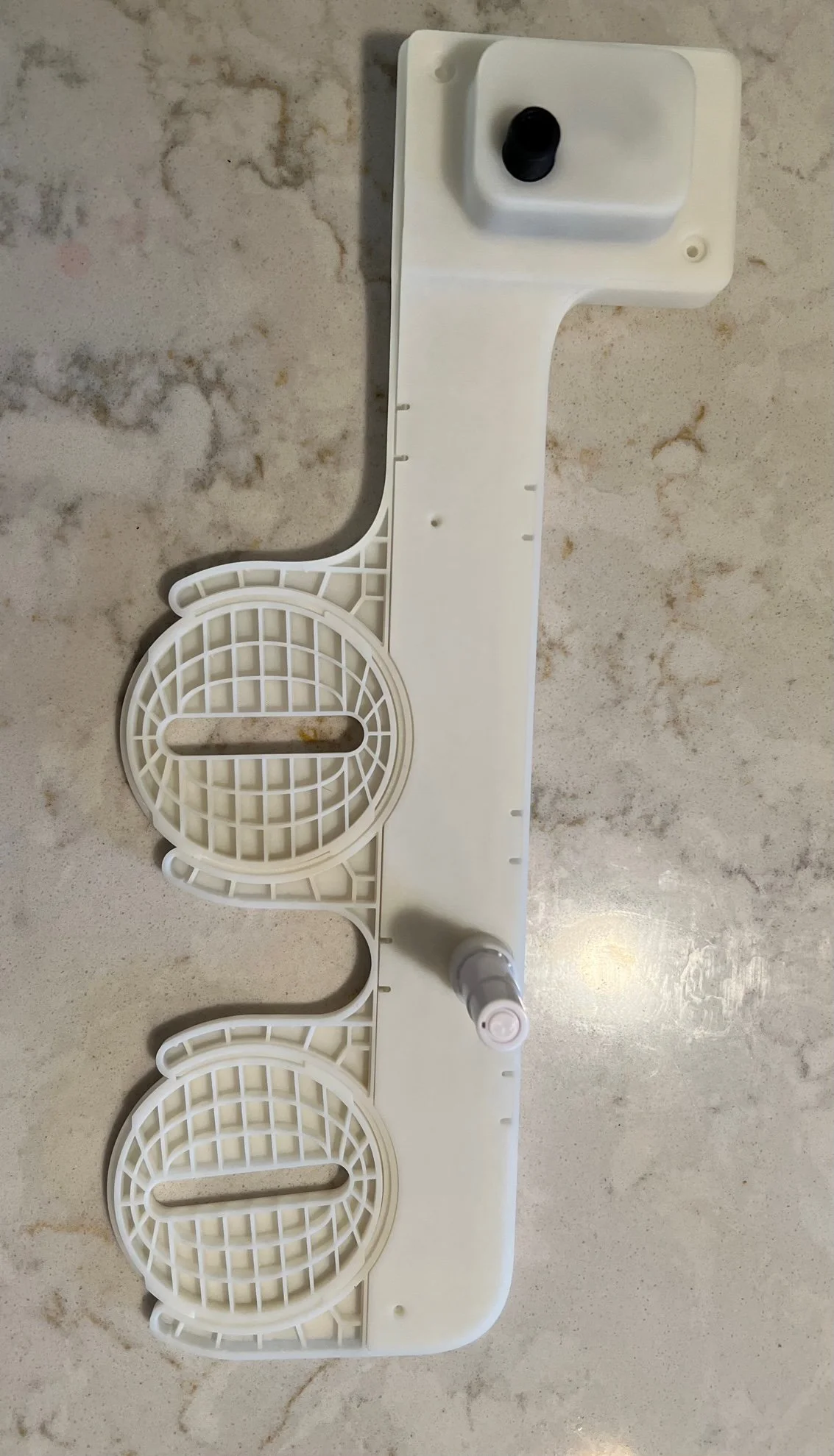
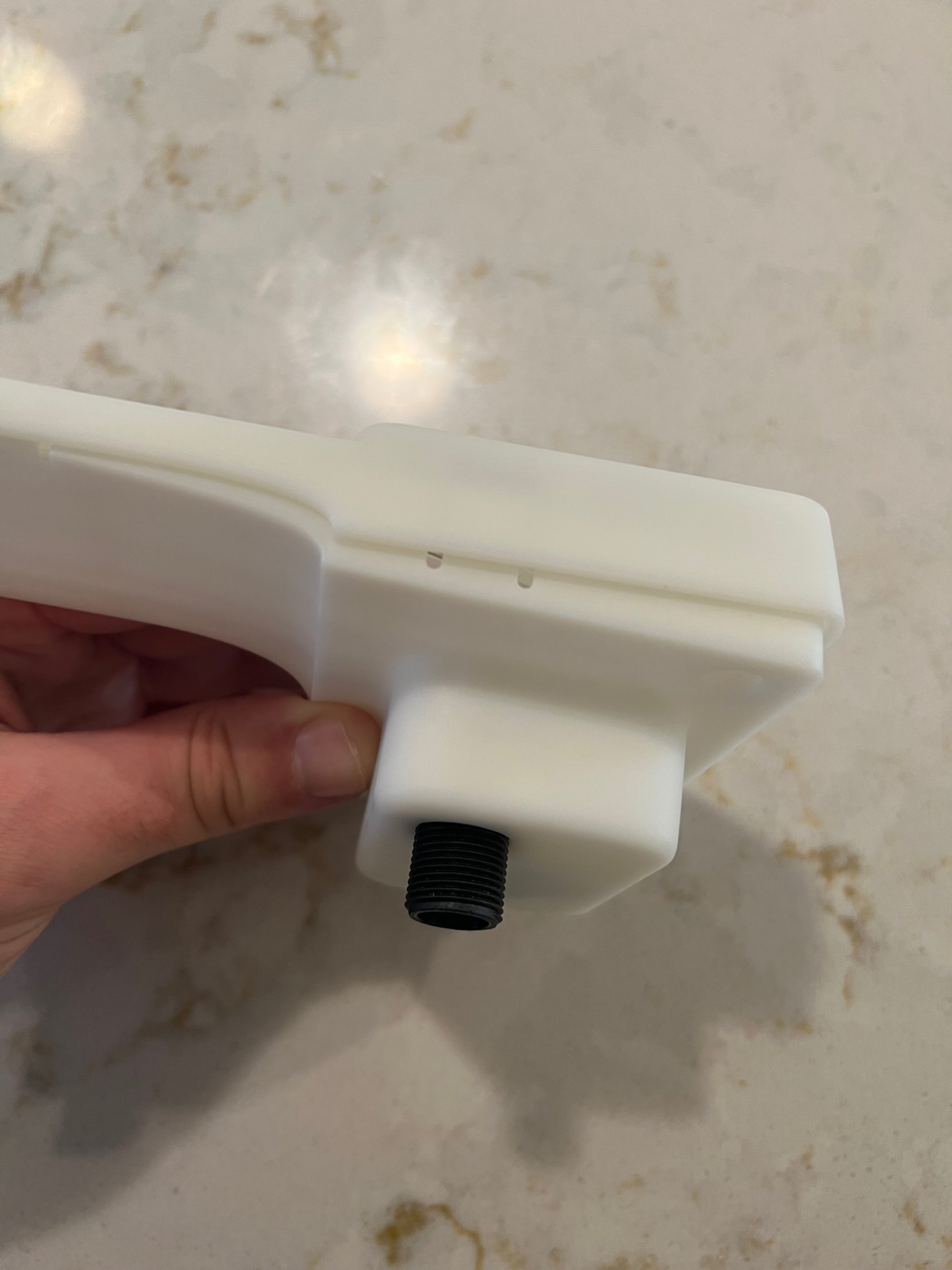
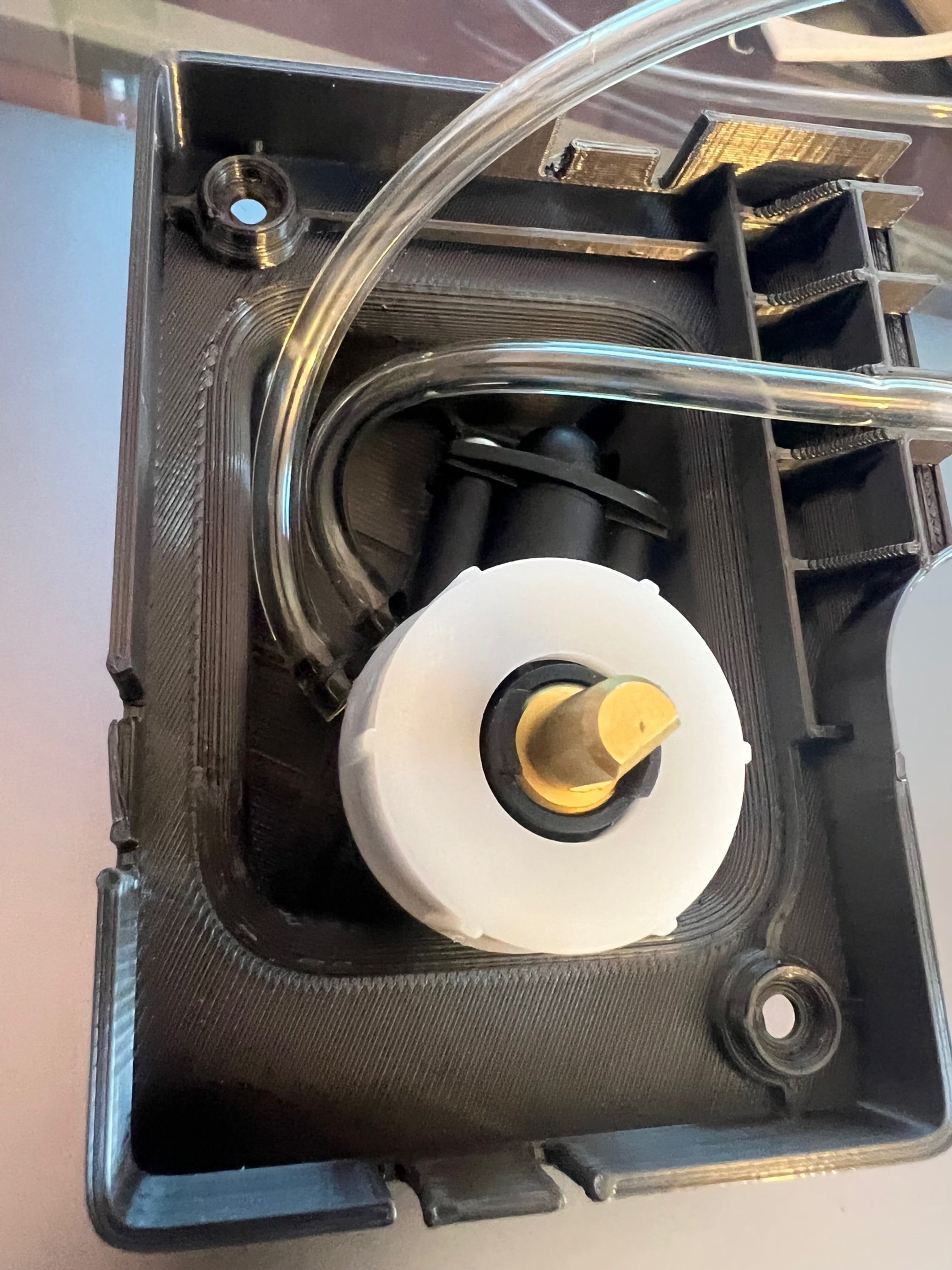
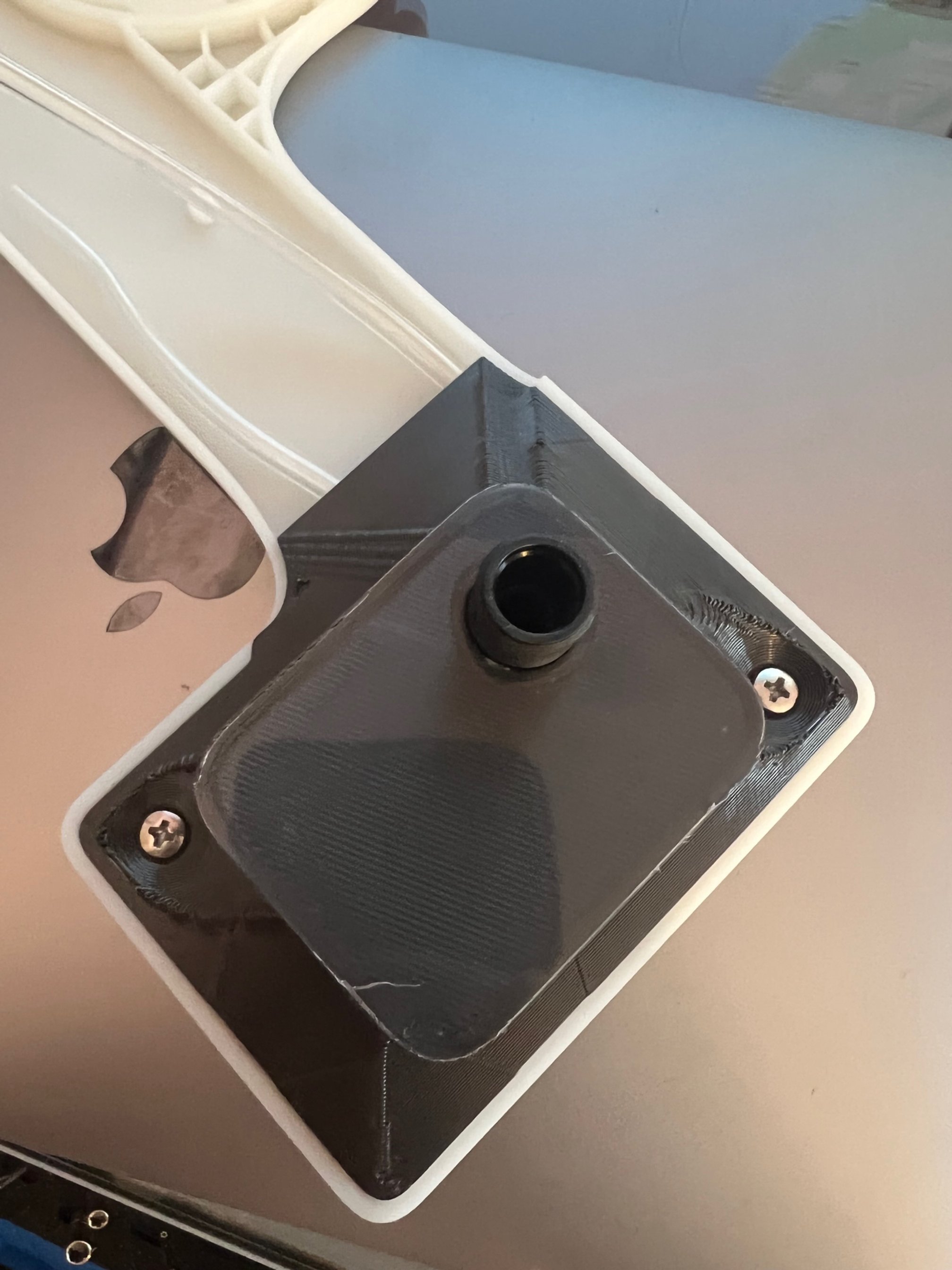
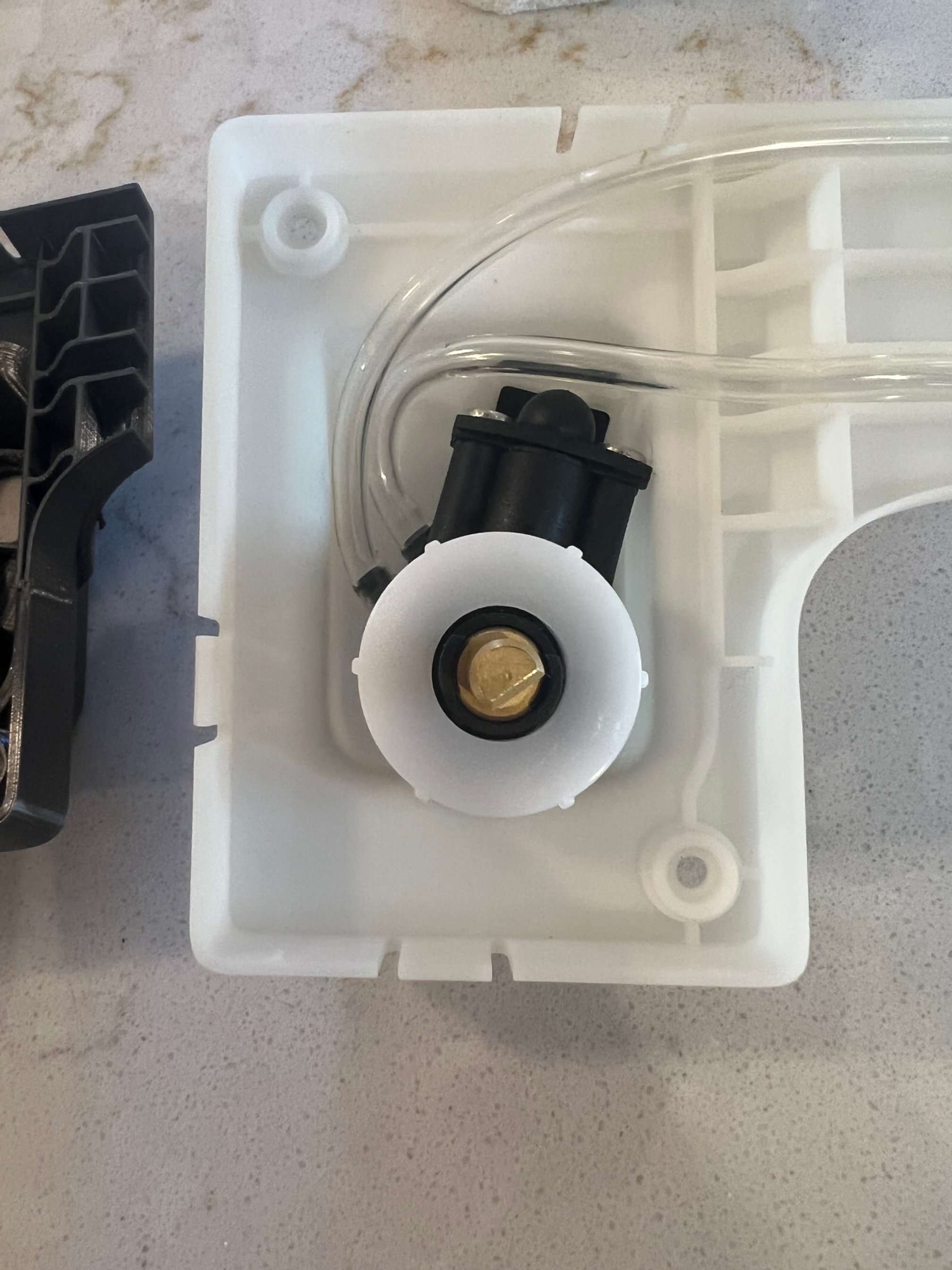
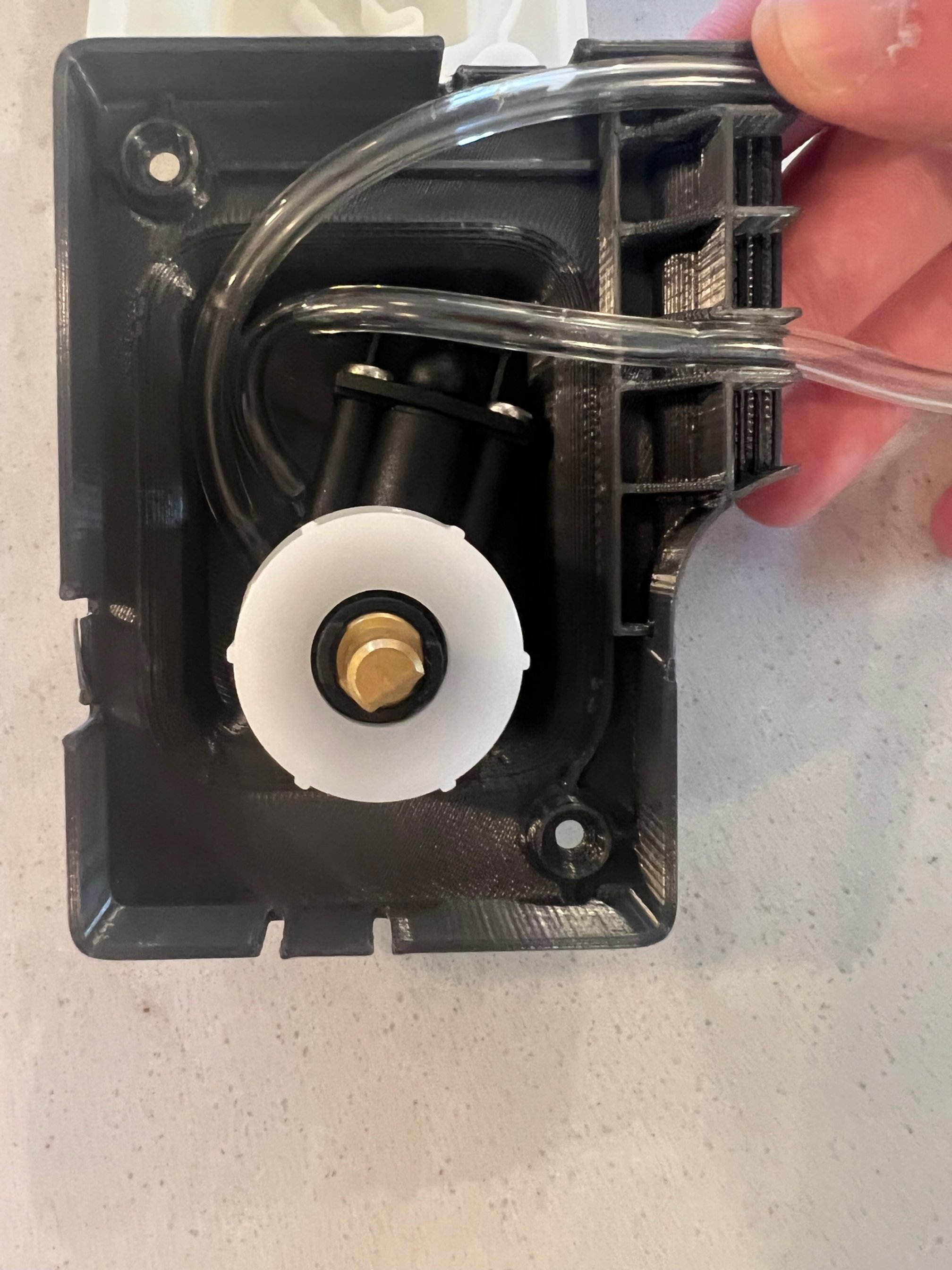
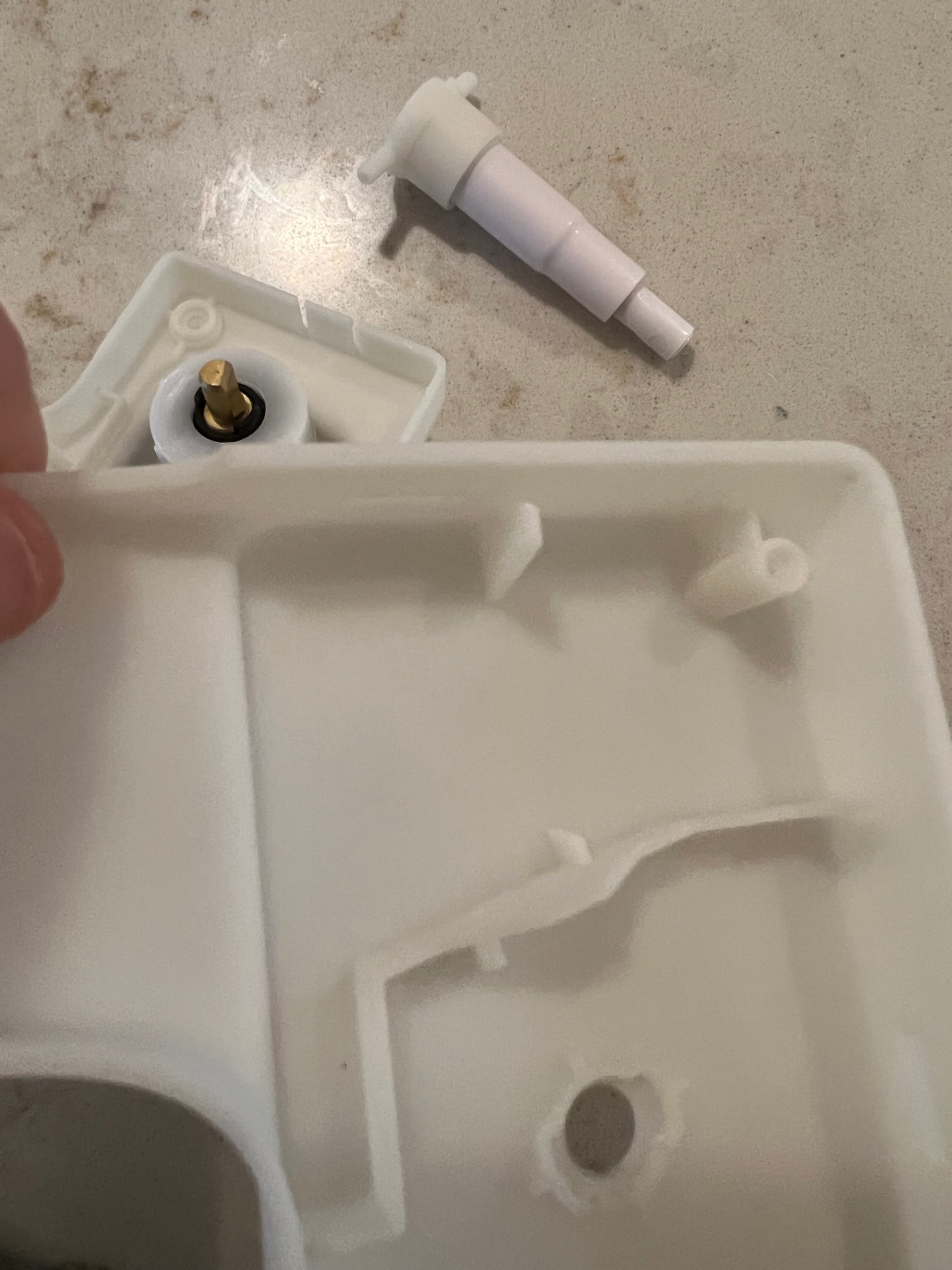
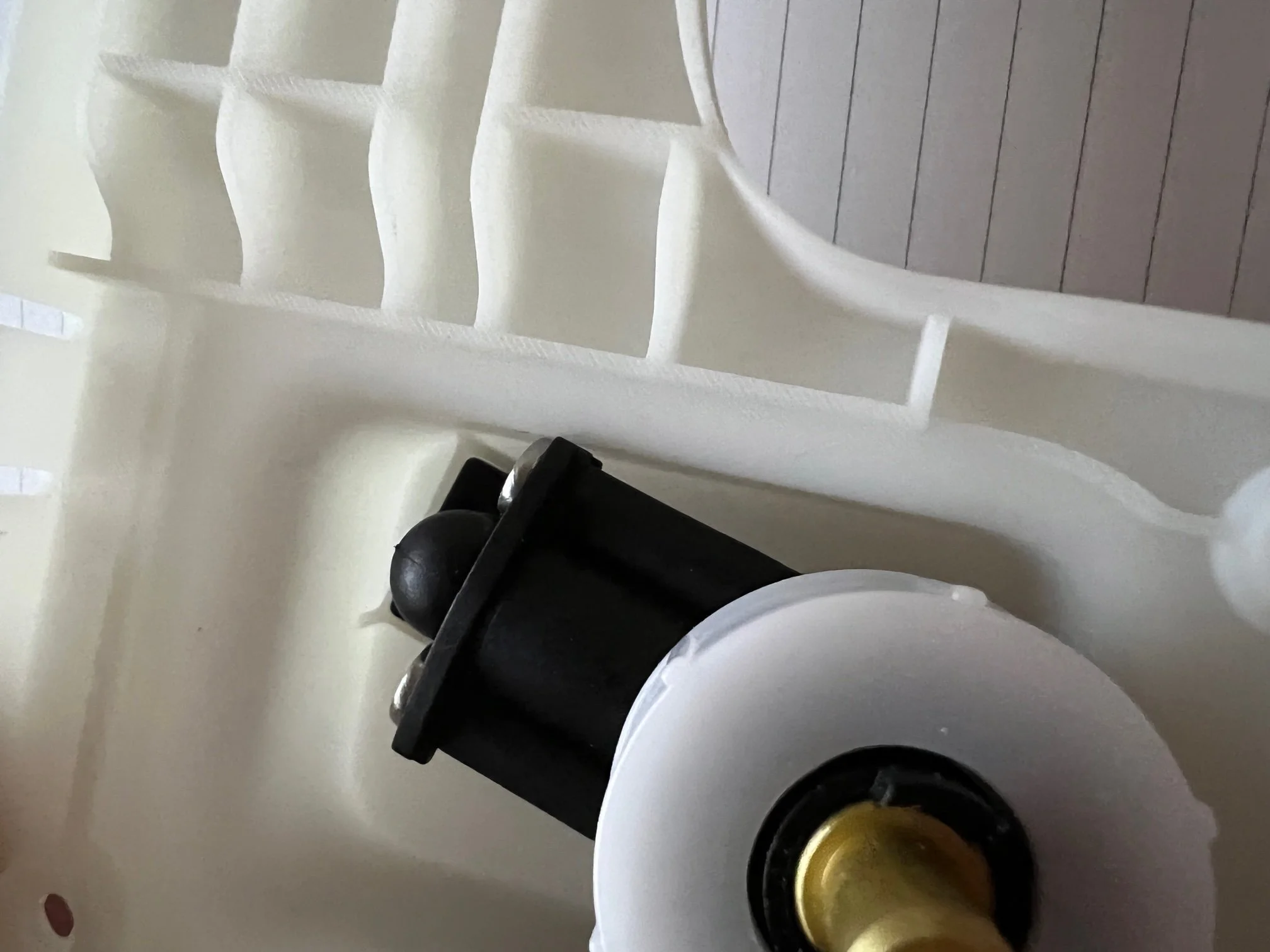
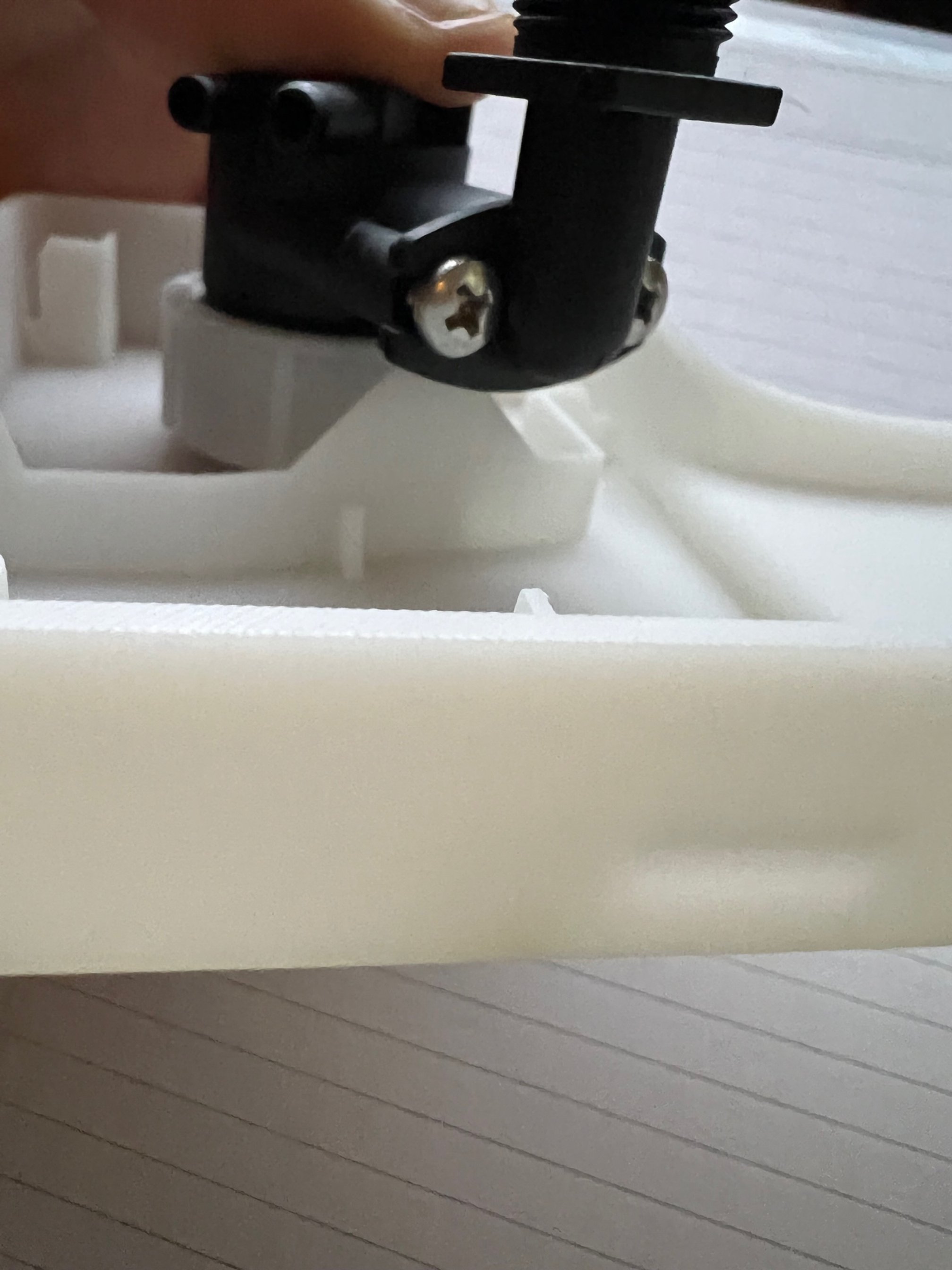
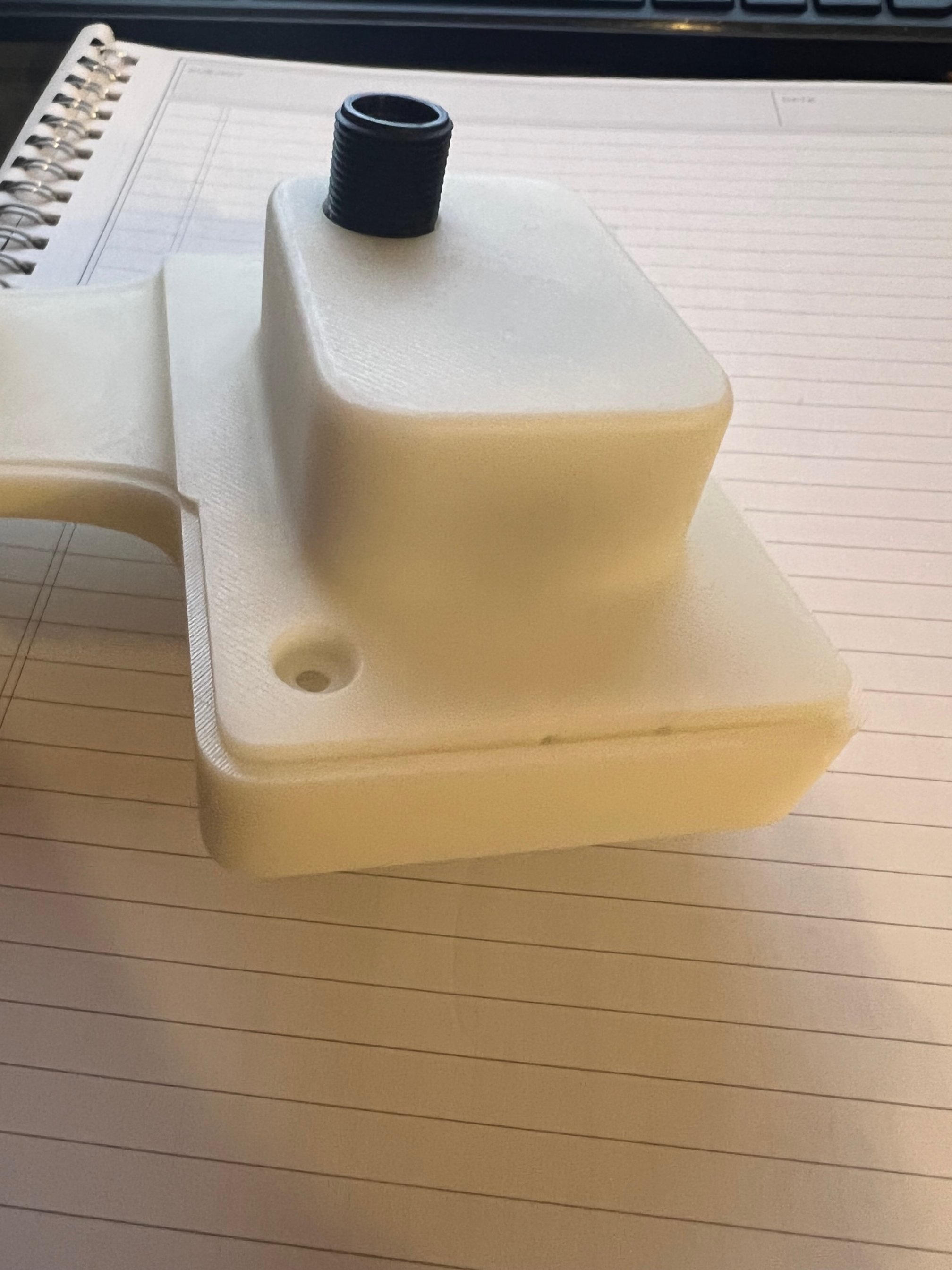
“Looks Like, Works Like” CNC Prototype
Before a final commitment to tooling, our manufacturer created a CNC’d prototype with automotive paint and silkscreen decals.
This stage was a last sanity check and great proposal piece for stakeholders. It turned out very well and tooling costs were approved.
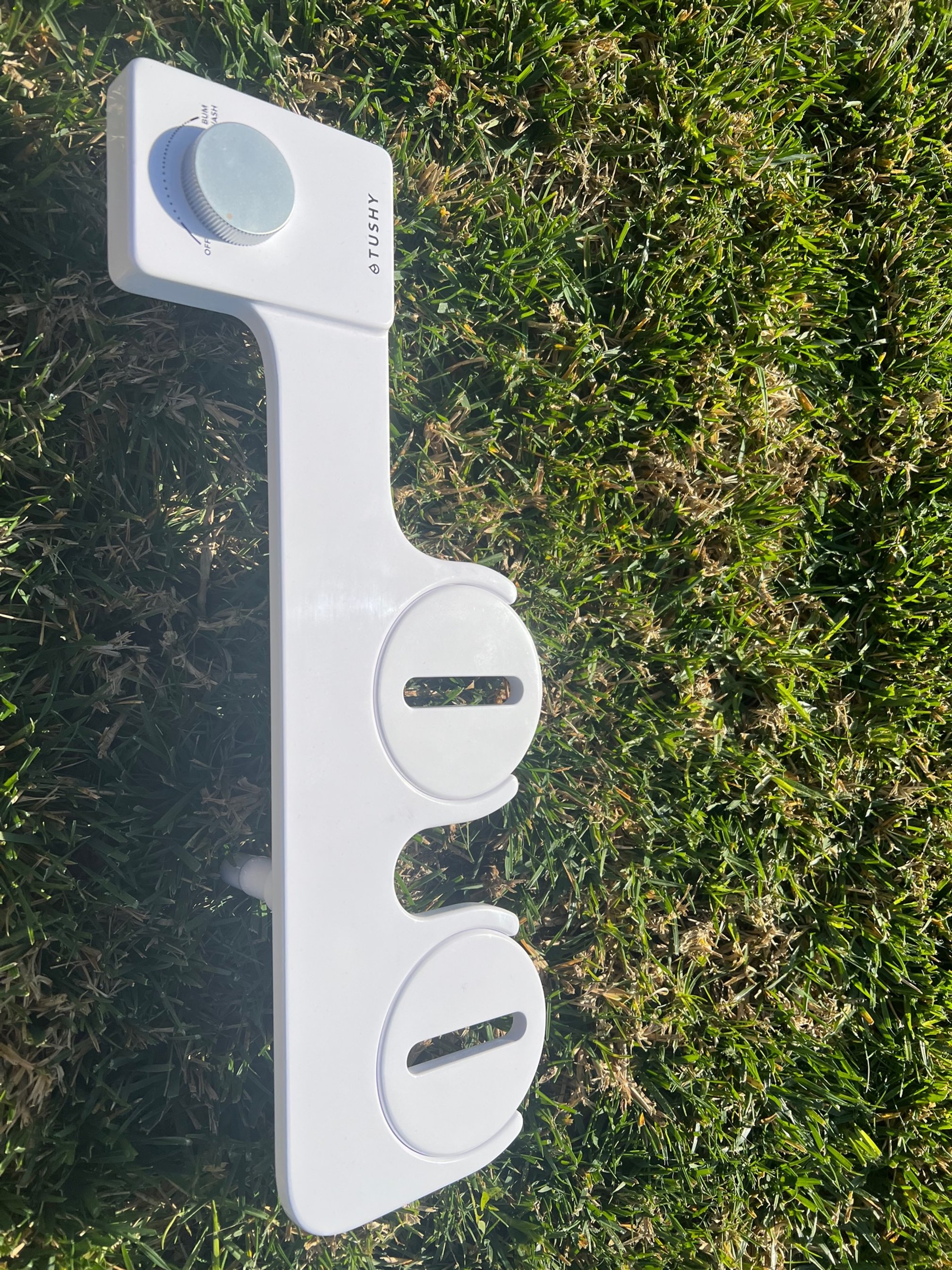
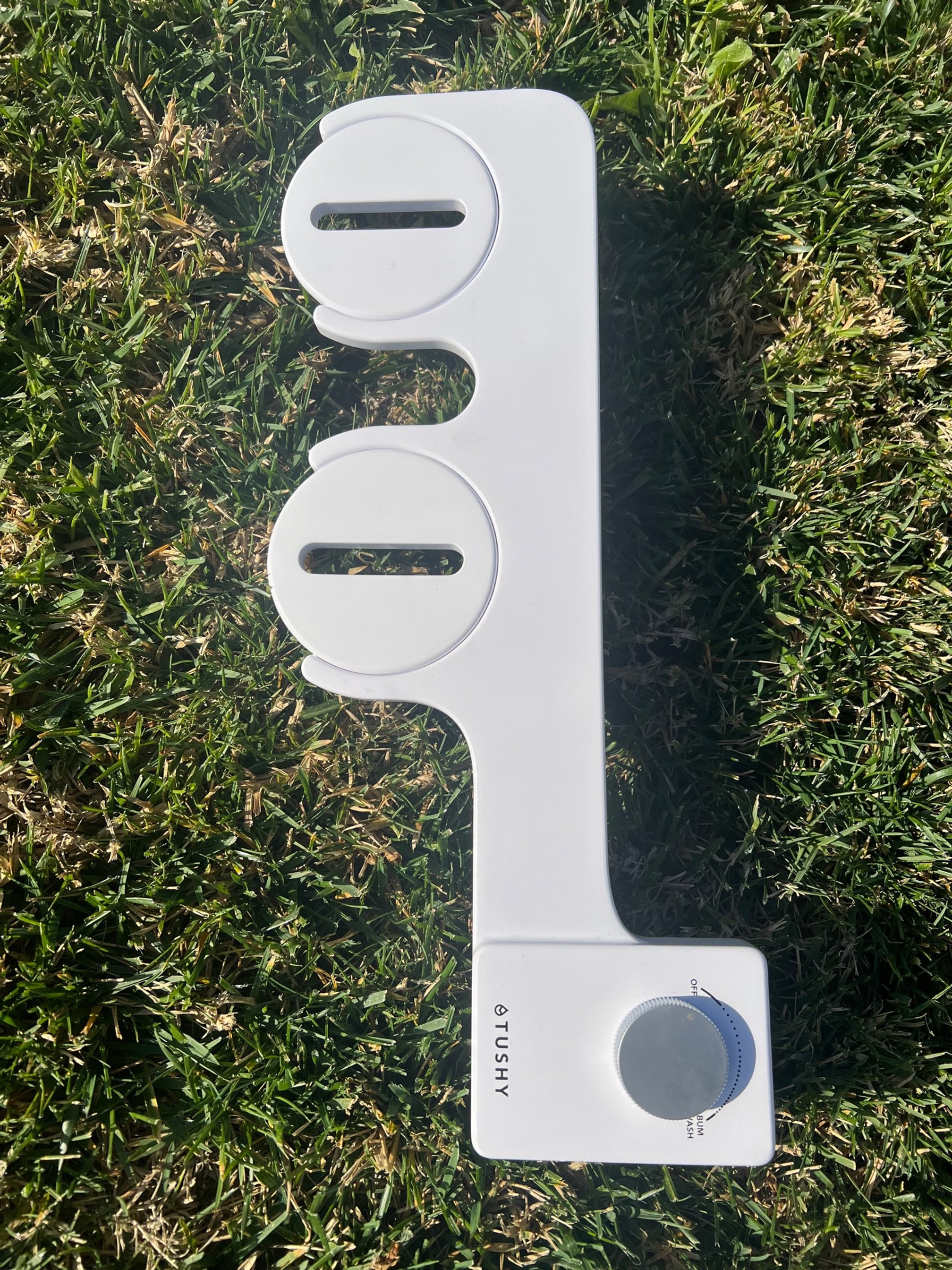
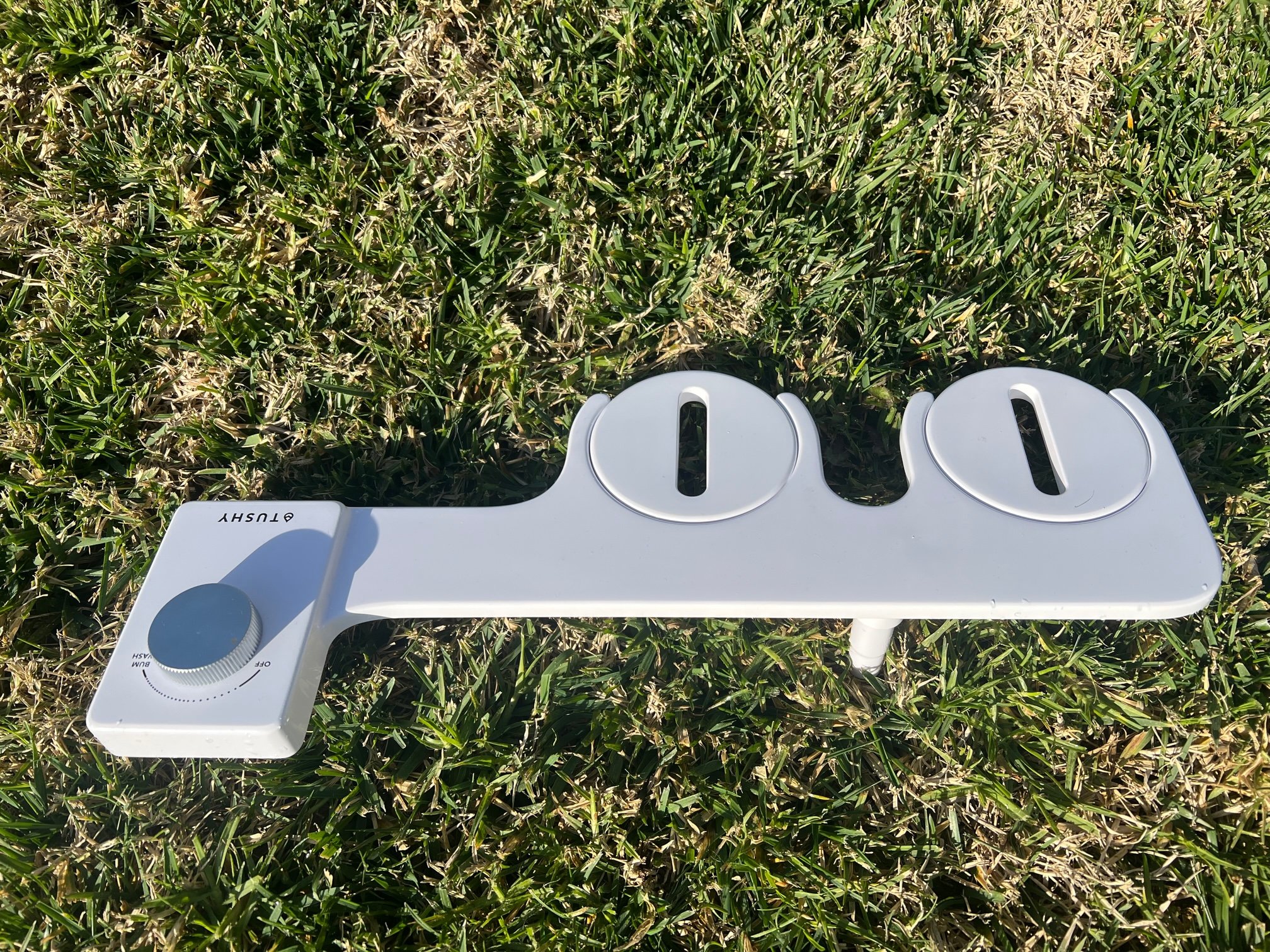
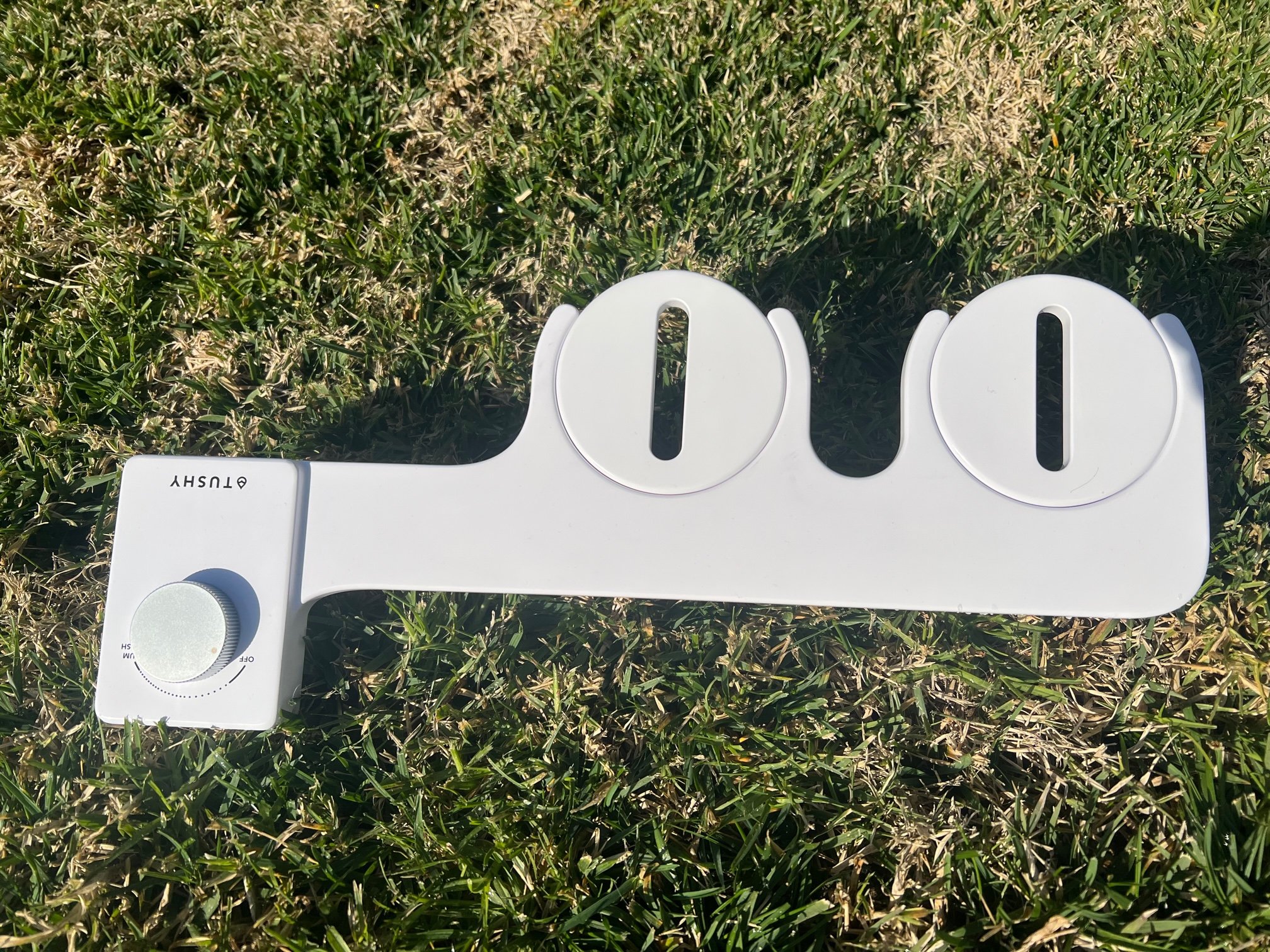
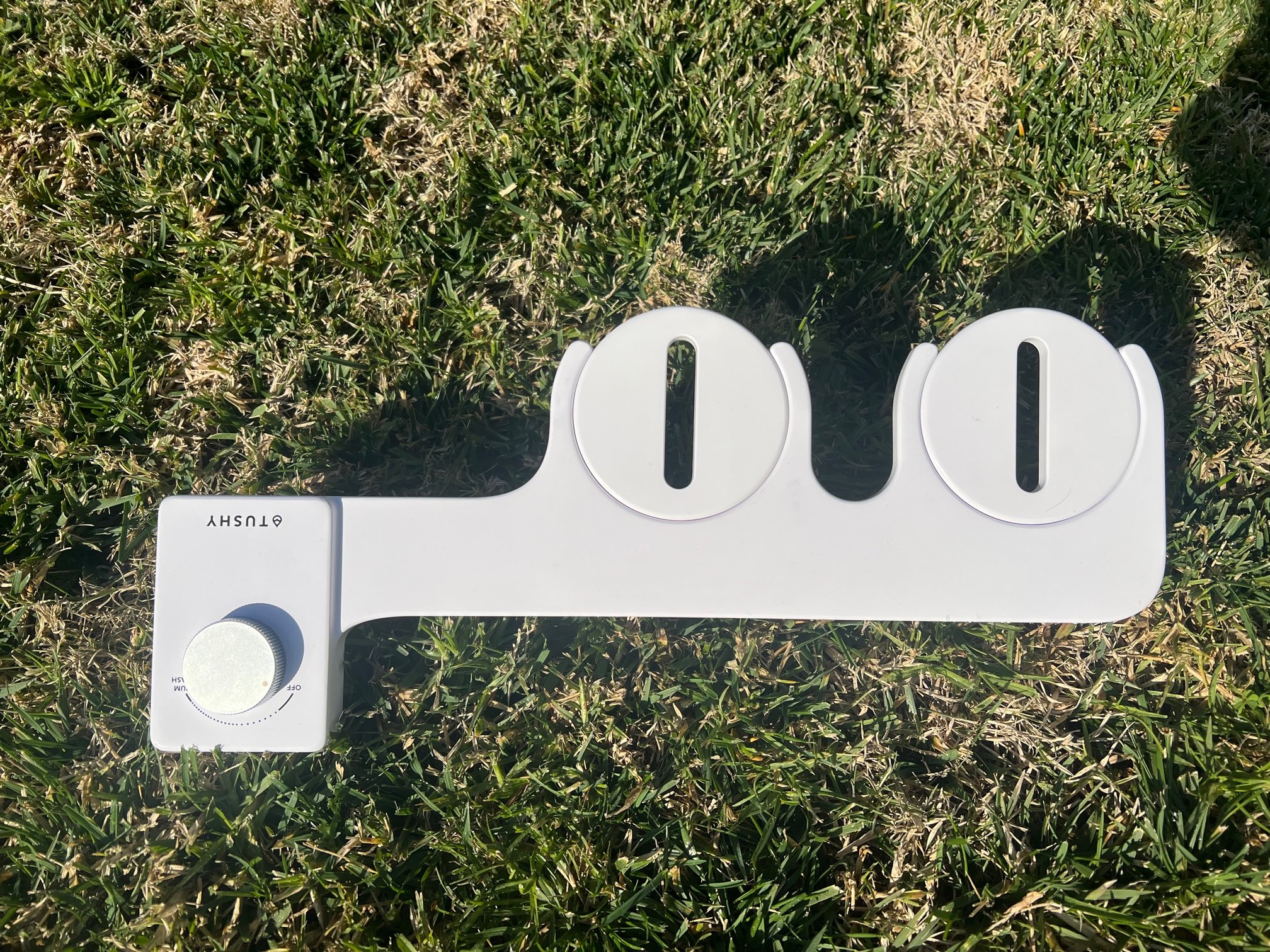
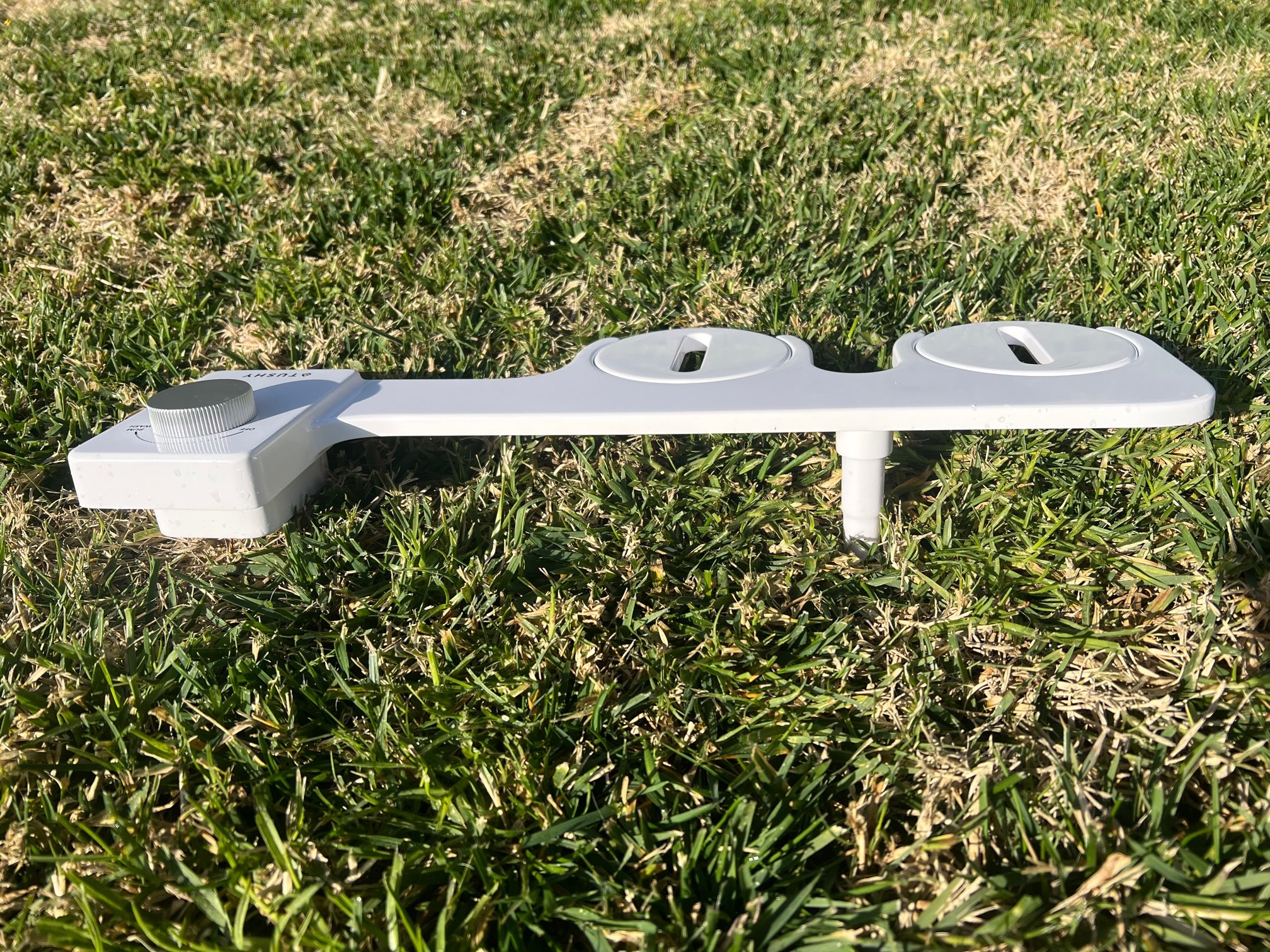
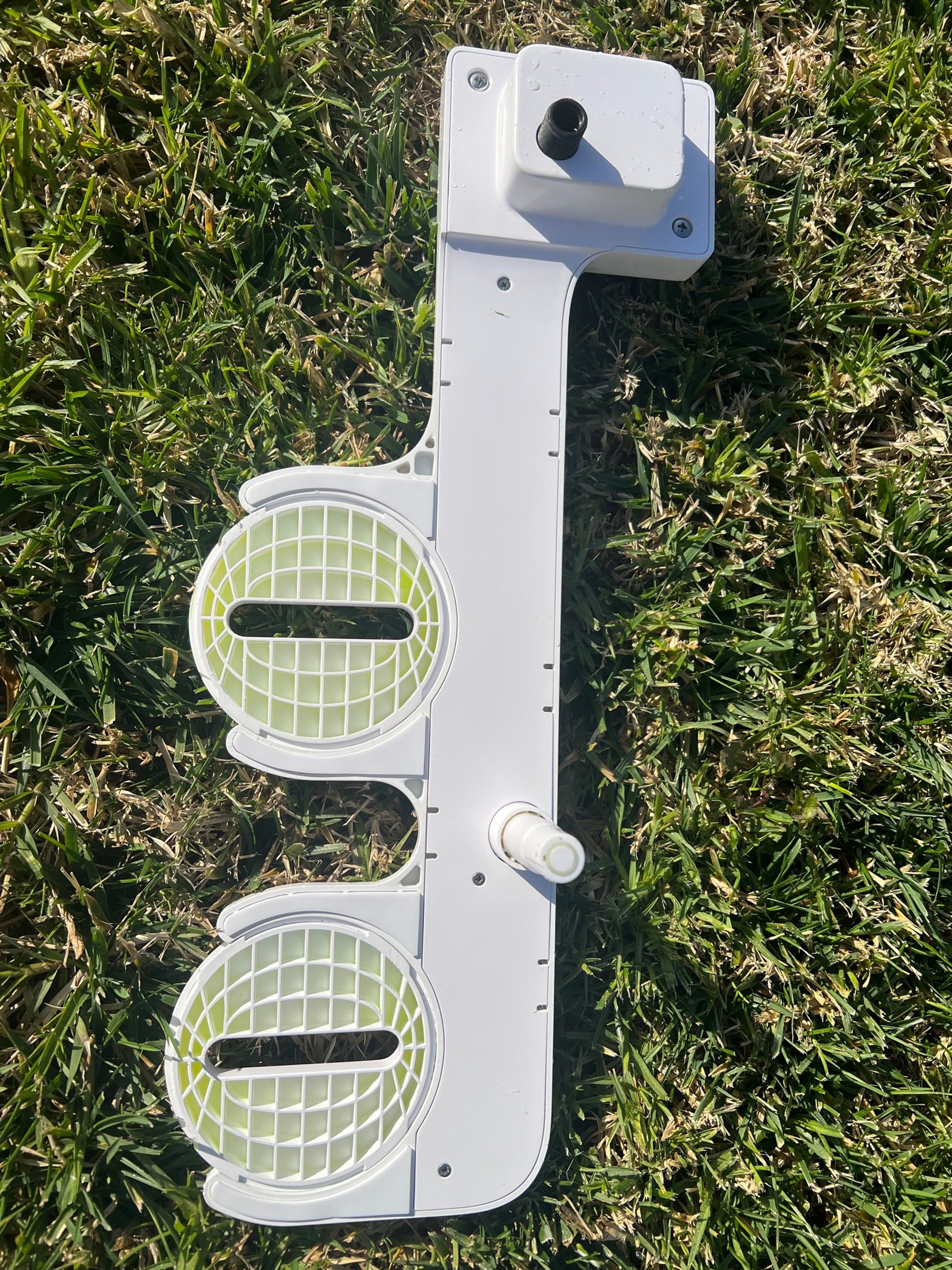
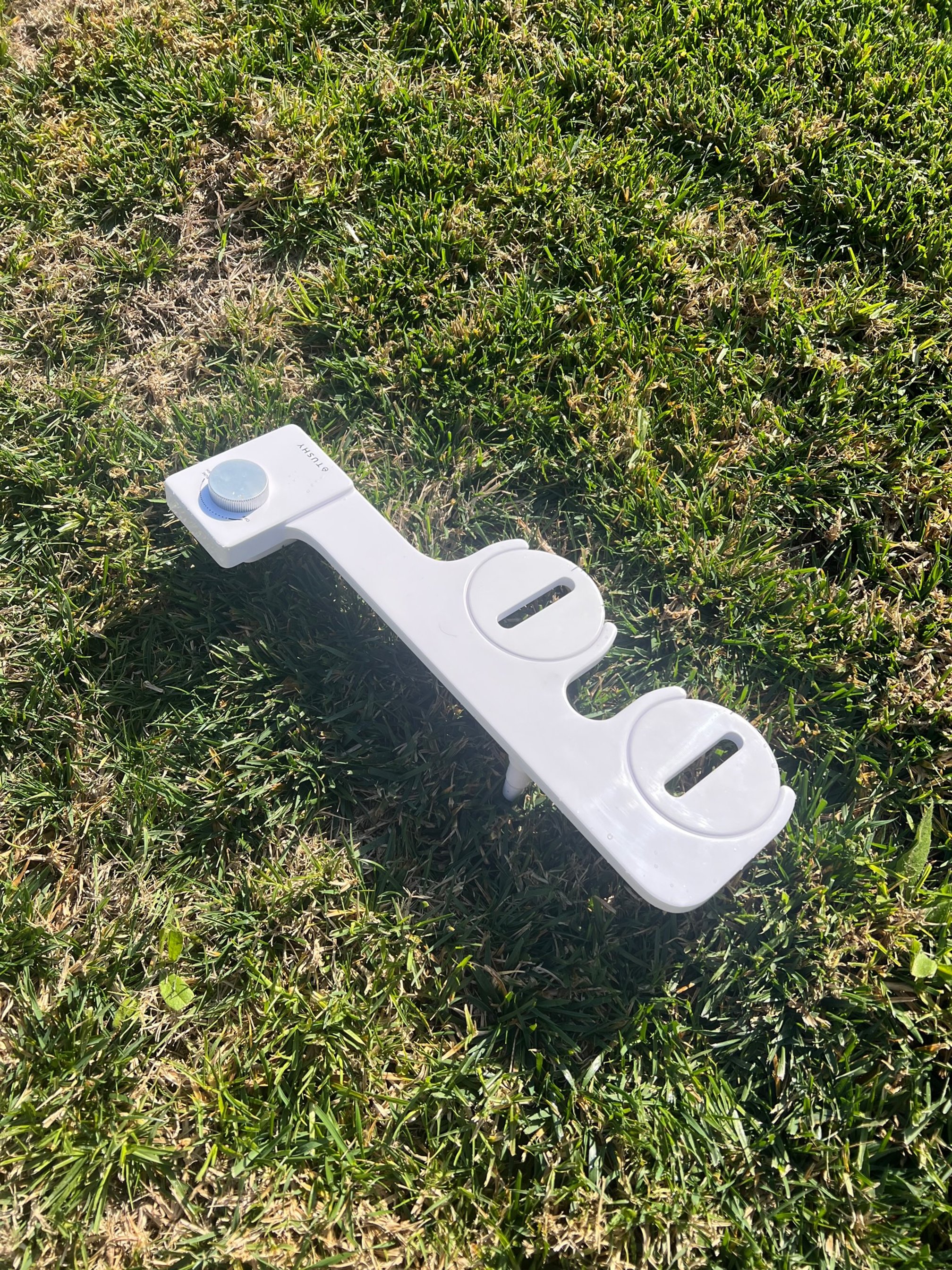
Tooling, Testing, Inspection, and Validation
There was a total of 6 new molds made for the Tushy Fresh
Top Housing
Bottom Housing
Flange
Diverter
Nozzle
Knob
T0 First Article Inspection
Heading up to the receival of the T0 Samples, I created a list of criteria and checklists with respective pass/fail values. Some of these inspection points included:
Injection Molding Visual Inspection
Warps, Knit Lines, Gaps, Bulging, Flash
Feature Check
Knob Torque, Valve Detents, Spray Range, Spray Alignment
Compatibility/Installation Check
Install Time, Seat Rise, Mounting Security
Internal Visual Inspection
Valve Clearance, Broken Ribs, Coupler Security, Tube Kinks, Diverter, Screws
Measurements
Dimensions, Weight
Failure Testing
Drop Testing, Vibration Test, Weight Limit, Console Critical Failure Load, Nozzle Deflection Critical Failure Load
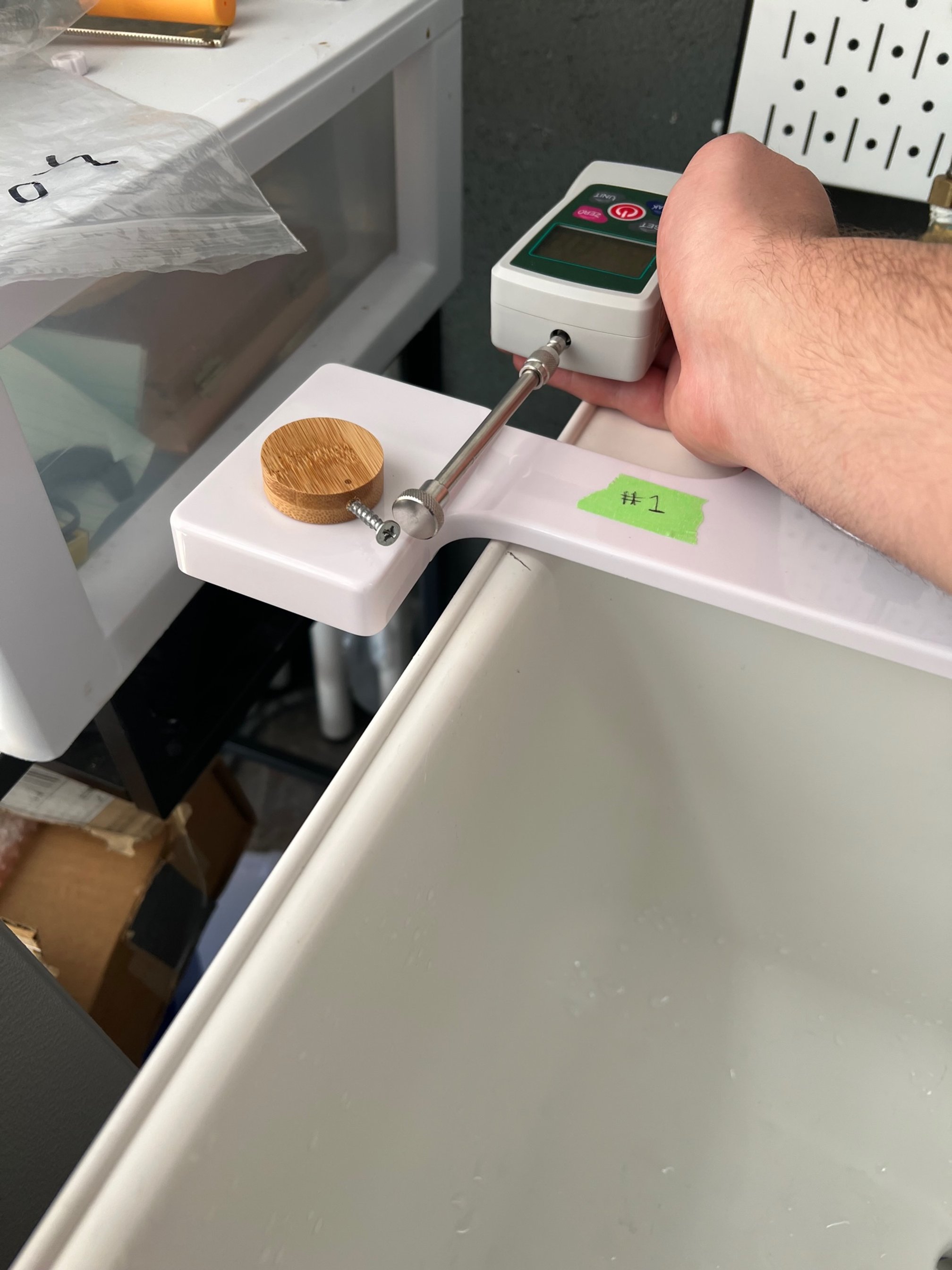

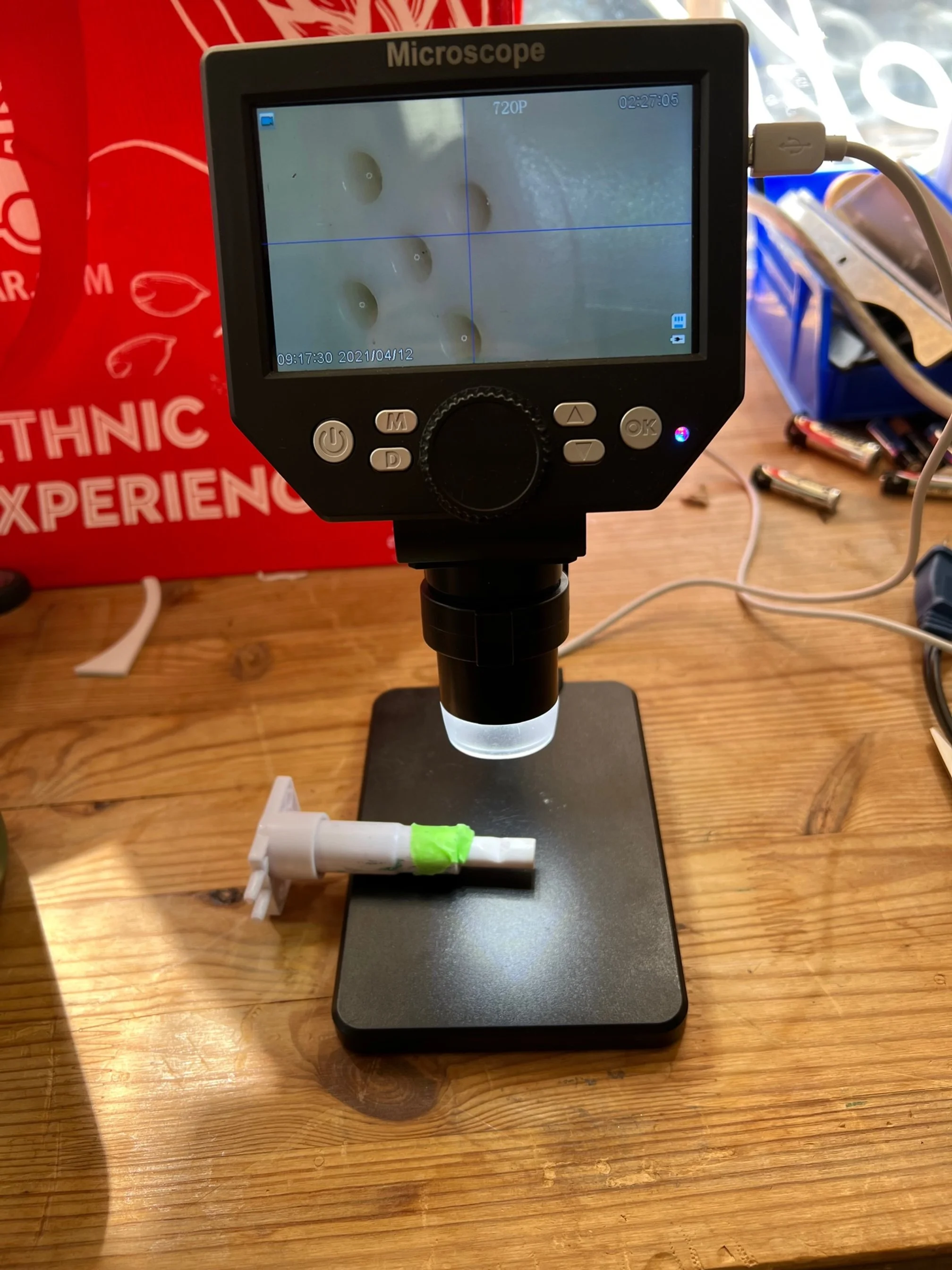
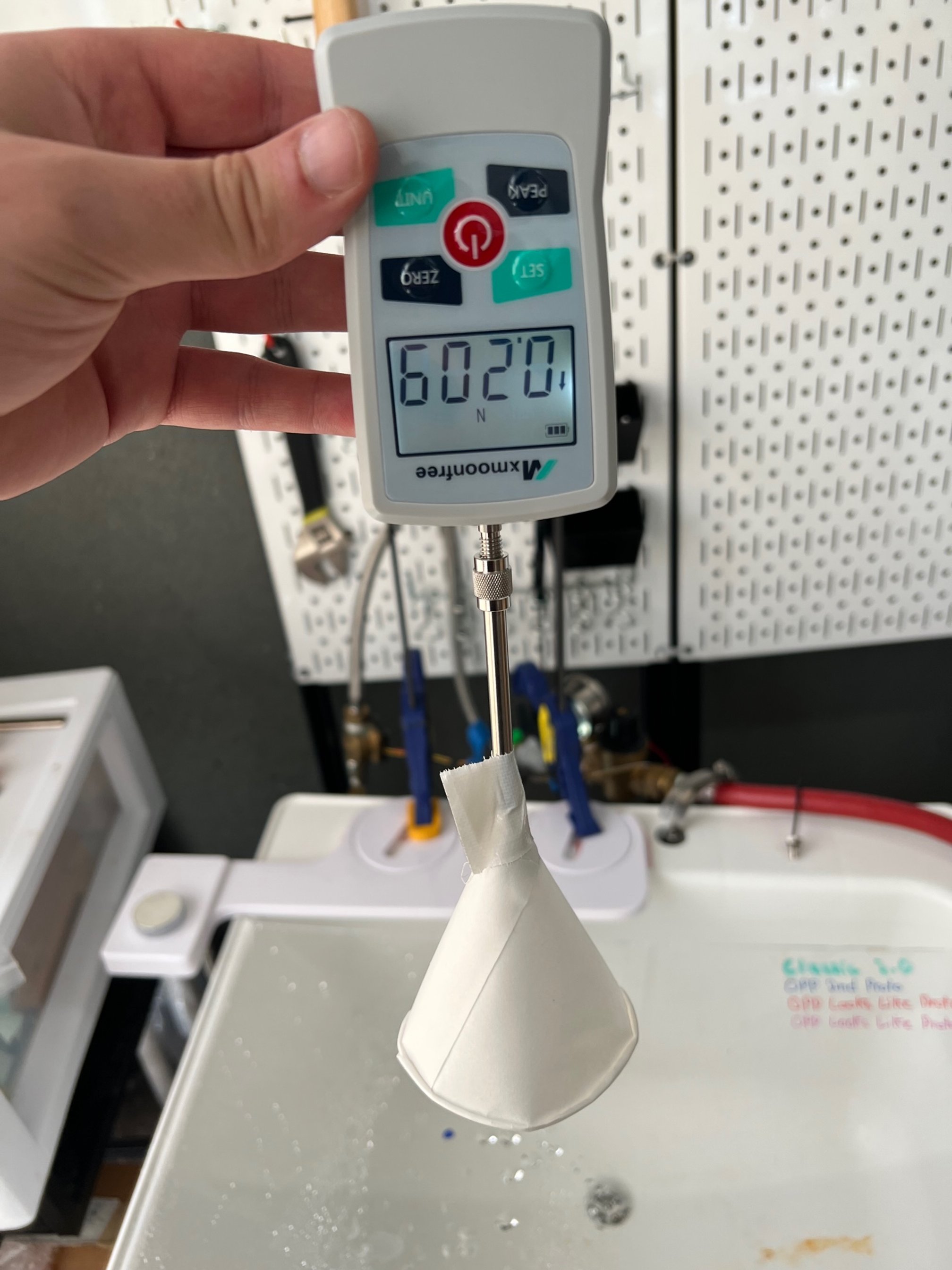
T1, T2, Pilot
Ultimately, the T0 inspection was quite good. There were some aesthetic issues with warps, sinks, and knit lines but these were easily fixable with some tool processing and adjusting the molding parameters. Feature and function wise, everything behaved as expected with the exception of the stream concentration. While the range was spot on, the pinhole streams would hit each other on some of the samples leading to deflection of some water, causing a mess. Upon discovering this, I recommended to polish the tool to reduce flash on the nozzle face. Additionally, to avoid this mistake in production I designed a jig test for the manufacturer to use in order to identify defective parts.
Conclusion
After finalizing the instruction manual and packaging, Tushy Fresh was ready for production. The project was completed in time for the launch in August 2023 and Tushy Fresh now finds itself top 10 in its category on Amazon.

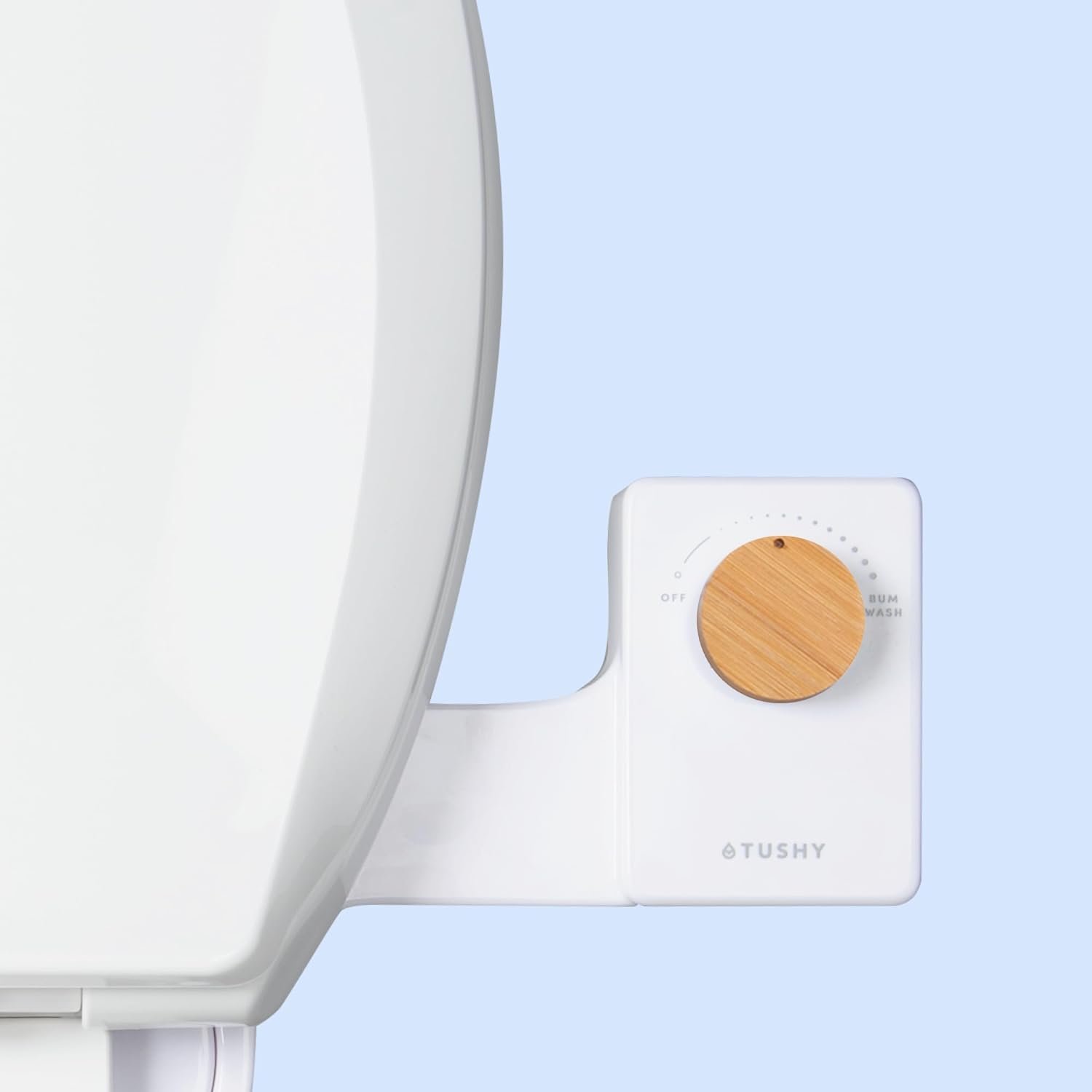
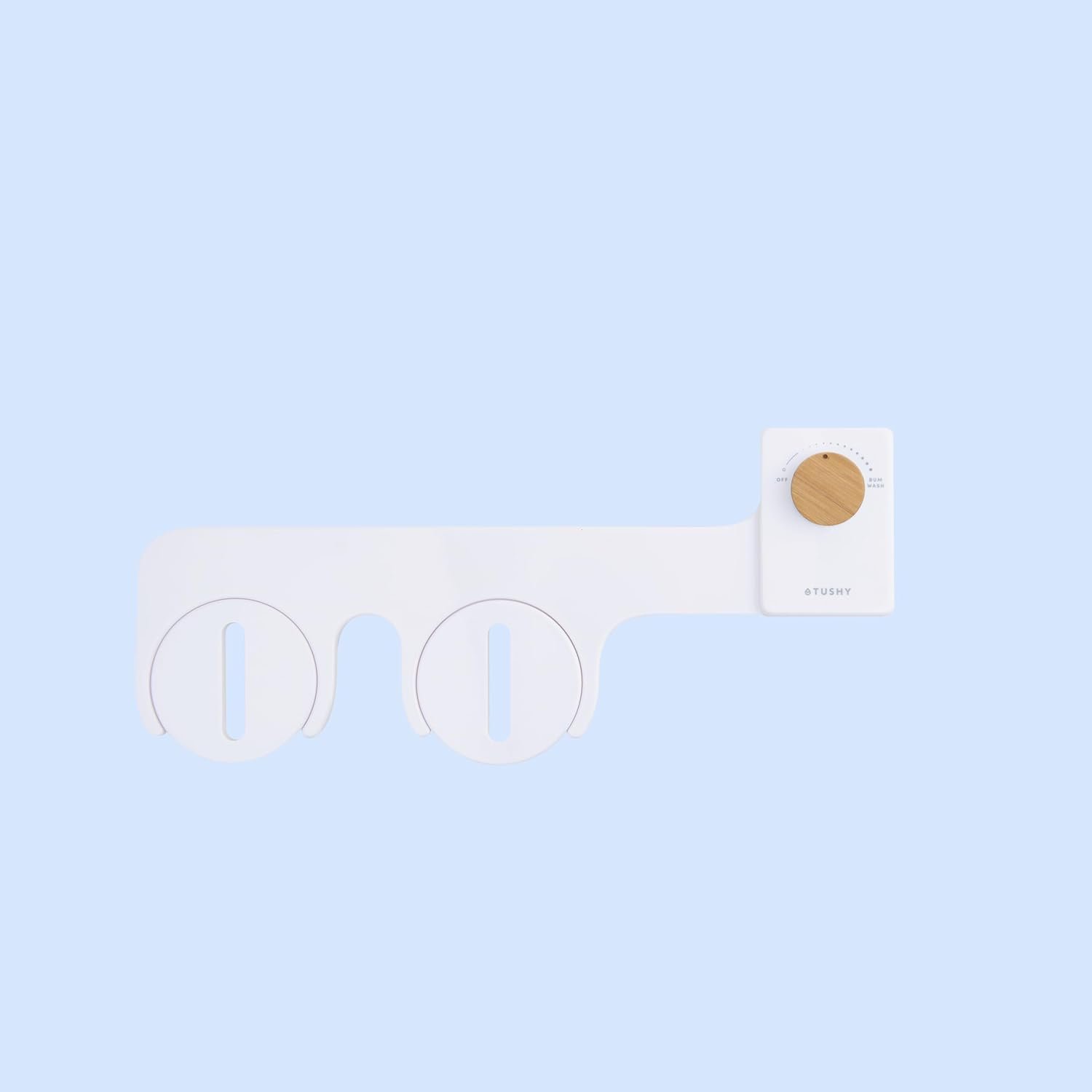
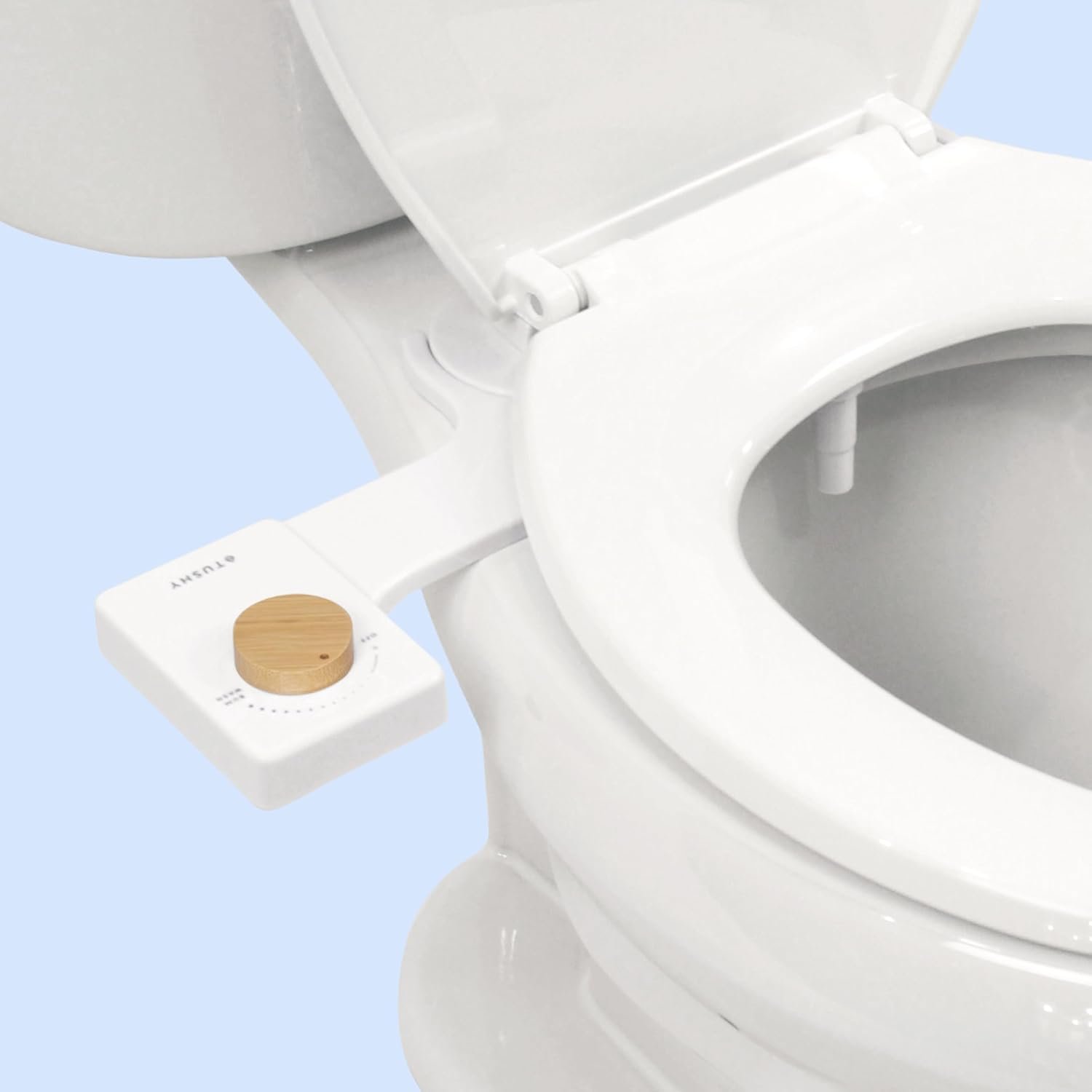